Abstract
Cladding is a surface treatment process which ultimately is used to create a higher wear resistance, improved corrosion resistance and to improve surface hardness.
Although first developed in the 1930’s as an electroslag cladding process the term Maglay cladding was only officially coined in Japan ten years later after further development.
Cladding is a process to deposit a fine layer of a material using strip or filler electrode that is fused under an agglomerated flux onto a non-alloyed or low-alloy base material to get good corrosion resistance, wear resistance & high hardness surface. The weld metal properties of the cladding are mainly determined by the chemical composition of the deposit which can be obtained with several different combinations of strip or electrodes, fluxes and welding parameters.
Large pressure vessels are used in hydrogen containing environments, for example, in the petroleum industry in hydrocracking, hydrodesulphurization and catalytic reforming processes as well as in the chemical and coal conversion industries. Many reactor vessels operate at high temperatures and at high hydrogen partial pressures, with 450°C and 15 MPa. The vessels are generally fabricated from low alloy, creep resistant steels which have good strength and structural properties but very low corrosion resistance. In chemical industries or petrochemical industries, it is difficult to resist the effect of corrosion in a highly corrosive atmosphere of hydrocarbons, stainless steel has very good corrosion resistance but it is very costly.
So, applying stainless steel or Inconel overlay on the inner surface of Carbon/Low alloy steel vessels economically serves both the purpose – required mechanical properties and good corrosion resistance properties.
The principle of strip cladding was developed in the USA around 1920 but in Europe the process retained detailed attention when the nuclear industry started (late 1950's). The nuclear power industry needed a method whereby thick- wall pressure vessels could be given a corrosion resistant inner surface. The electroslag process was invented by H K Hopkins of the M W Kellogg Company in 1936. At that time stainless clad plate was being produced by making submerge arc weld deposit of the required composition on one side of slab and then rolling out into plate.
The system works well for 12Cr cladding but with 18Cr 8Ni types the weld deposit cracked. Hopkins therefore stood the slab on end and applied the weld metal by traversing to and fro and at the same time moving upwards. In 1971, Seidel and Hass reported a new adaptation of electroslag processing for cladding in the flat position using strip electrodes and called it electroslag surfacing. Ten years later, this concept was also utilized by Nakano in Japan to develop Kawasaki’s electroslag surfacing techniques called “Maglay”.
The MAGLAY process utilizes the ESW process that employs Joule’s heating of slag instead of arc as a welding heat source. As a result, the weld dilution ratio is decreased to about 10% and the serviceable electrode width is expanded to 150 mm. Furthermore, fused slag and metal flow are controlled through the action of external magnetic field, thus improving bead smoothness. This process provides a considerable improvement over the conventional overlay processes.
The characteristic of the ESW overlay welding process lies in the mechanism of forming penetration of the parent metal. In order words, in the case of arc fusion, arc is generated from a part of the electrode as shown in Figure 1, and as it moves in the direction of electrode width, penetration is completed. Arc movement is not necessarily uniform: it may be without fusing the parent metal and thus tends to cause incomplete penetration. Since this phenomena becomes more significant as electrode width becomes wider, the electrode width is limited to 75 mm for practical reason. Also, on the occasion that slag of the preceding pass has not been completely removed from the weld toe, arc is not generated, and it becomes a defect as slag trapped in.
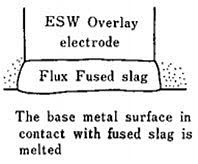
Figure 1:Penetration characteristic of ESW overlays On the other hand, in the case of the ESW overlay welding, the parent metal with which high-temperature slag has come in contact will fuse regardless of the presence of residual slag from the preceding pass, and stable penetration can be obtained. Particularly, in the case of the MAGLAY process, by means of action of the external magnetic field, high-temperature slag in the center of the molten pool is flown toward edges of the molten pool where defects are likely to occur, thus preventing insufficient penetration.
Accordingly, in the MAGLAY process, the external magnetic field is utilized to control flow direction and velocity of the fused slag and fused metal. This principle is shown in Figure 2. Lorentz force is generated by the interaction between the external magnetic field perpendicular to the parent metal and welding current, and the force from the center of the molten pool to its edges supplies the fused slag and fused metals to the edges.
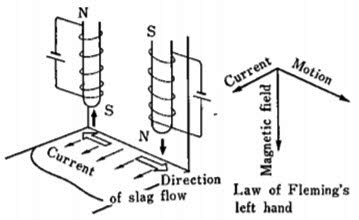
Figure 2:Control of slag flow with outer magnetic field The MAGLAY process has been developed as a high-efficiency and high-quality overlaying process. In this process, a newly developed flux of special composition is used. By converting the heat source from arc to Joule’s heat of slag, the dilution ratio is reduced by about 10%. And serviceable electrode width can be enlarged to 150 mm. Furthermore, by means of action of an external magnetic field, a flow of fused slag and fused metals is controlled, resulting in a very smooth overlay surface including lap bead.