Abstract
Aluminum is well established at the front of the pack with regards to providing the technological answer to the increasing challenges of light weighting whilst maintaining integrity of the material for the desired applications.
Semi solid rheocasting is a development within the casting sector which enables improved quality in die casting without increasing cost.
In the automotive and electronics industries, increasing demand for high-performance equipment forces scientists to improve the capabilities of many applications by innovating new creative solutions.
The major driving forces for improvement is to find the possibilities for weight minimization and even higher reliability of the components in service. Therefore, selecting a suitable alloy and the best possible manufacturing method is a critical matter from an engineering and scientific perspective.
Looking at constraints in the industry from both the angle of business image and the need for advanced technical material solutions, such as low-density, corrosion resistance, high strength, and high thermal/electrical conductivity, aluminum alloys emerge as suitable candidates.
For advanced technical production solutions of aluminum alloys, extrusion, or forging for simple shape components, as well as casting and machining for more complex shapes, are very common manufacturing methods. In most cases, compromises in specified criteria such as cost, dimensions, design features, and material property requirements, limit the range of candidate processes and lead to the use of the most effective process.
For some potential die-casting applications, the porosity level obtained with the traditional process isn’t sufficient to satisfy customer mechanical property requirements. Today, demanding leak tests and defect-free machined surfaces sometimes are requested. The application of a vacuum and squeeze pins can improve the quality of the castings, but those measures complicate the process and increase maintenance requirements.
However, an alternative die casting process—semi solid rheocasting (SSR), developed by the Idra Group SRL, Travagliato, Italy, and based on a Massachusetts Institute of Technology patent—has been effective in improving metallurgic casting quality without increasing costs.
It utilizes a graphite agitator as functional equivalent to conventional rod agitators. The purpose is to rapidly cool and apply convection from within the melt to create the globular microstructure. The critical factor for formation of thixotropic slurry in SSR is the combination of rapid cooling and convection while crossing the liquidus temperature. After a small fraction of solid is created, further agitation is not necessary to continue globular growth. A superheated alloy is initially agitated and cooled for roughly 5-20 s. Then the rotating rod is removed and the quiescent melt is cooled to the desired forming temperature (see Figure 1). The process is implemented using a rheocasting machine, designed based on technology of existing die casting machines. During a cycle, a ladle cup of molten metal is brought to the station by a robot. The station cycle is designed to be less than the cycle of the die casting. It is claimed that this technique exhibits a number of advantages as compared to other rgeocasting methods. Many of them are attributed to the way of cooling/agitation: (i) heat removal outside of machine reduces the cycle time: (ii) a spinning rod ensures uniform cooling within the alloy volume; (iii) the rapid cooling/stirring combination creates fine microstructure which does not require a long time to transform into globular forms.
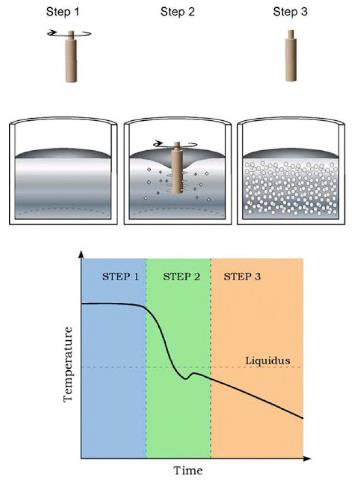
Figure 1: Schematic view of the SSR process: Molten alloy is held above the liquidus (Step 1), then rapidly cooled and agitated for a controlled duration to a temperature below the liquidus (Step 2) before agitation and cooling ceases (Step 3)
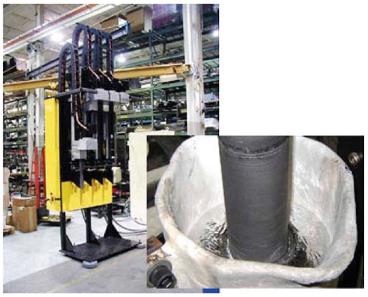
Figure 2: SSR cell and graphite stirring rod in melt
Compared to traditional die-casting, SSR:
- reduces porosity, which eliminates secondary operations like impregnation and machining;
- allows the application of T5 and T6 heat treatment to the parts and makes them weldable;
- reduces casting cycle times by 25%, depending on part thickness;
- leads to longer die life due to lower metal temperature and injection velocity;
- reduces draft angles to 0.2 degrees and achieves near-net-shape;
- lowers consumption of release agent;
- achieves wall thicknesses from 2.5 to 12 mm.