Abstract
Press hardening steel answers several challenges within the automotive industry by successfully meeting the requirements of increased safety whilst at the same time contributing to lighter, more eco-friendly materials.
Strength levels can be up as high as 1500MPa meaning application in passive safety systems such as side impact beams works very effectively.
Today’s car bodies have to meet various different and partly contrary requirements in the automotive industry. Higher demands on passive safety tend to result in weight increase while ecological aspects like reduction of fuel consumption and carbon dioxide emission call for light weight constructions. The application of high strength steels was the first answer to ensure the required safety directives in a light weight car body construction. Although high strength steels have superior mechanical properties, stamping operations become more difficult. High strength goes parallel with reduced formability, increased spring back behavior and excessive tool wear in cold forming applications.
Press hardening steel has become a much used material in car body manufacturing due to its excellent safety and lightweight potential. In some recent car models press hardening steel has reached already a weight share by more than 20% in the body structure while it is estimated that it could reach even around 40% in the future. However conventional press hardening steel based on the alloying concept 22MnB5 was designed originally not for automotive application. In spite of the high strength level, press hardening steel has generally low toughness due to the relatively high carbon content and its martensitic microstructure.
Particularly important is the ductile-to-brittle transition temperature at low temperature, which might lead to unexpected failure in cold climate regions. Furthermore, hydrogen embrittlement is a major concern in press hardening steel as previous results indicated that only a few ppm of hydrogen could induce delayed cracking. Generally it is important that impact energy should be absorbed by the material to avoid unexpected disintegration of the structure. This material capability is usually characterized by the toughness. All these characteristics have not yet been systematically investigated in press hardening steel. Consequently, no attempts have been made to optimize conventional press hardening steel for obtaining better toughness, lower ductile-to-brittle transition temperature and reduced sensitivity to hydrogen induced cracking.
As mentioned above, press hardening is an effective technique to fulfil the contradicting requirements of very high strength levels (1500 MPa) in combination with a high complexity of geometry. Hardenable boron steel (between 0.002% and 0.005% boron) is austenitised at a temperature above 850°C and then quenched between cold tools with cooling rates greater than 25 K s-1 to attain martensitic transformation.
The utilization of hardenable steel in combination with press hardening applications began in the 1990s and is mainly used for producing passive safety components such as side impact beams, bumper beams and different types of reinforcement components. Besides passive safety and weight reduction, corrosion protection is another major aspect for materials in the automotive industry. Systems of particular interest are those which are able to act as a sacrificial anode for the base material like the zinc coating of galvanized steel. The use of continuously galvanized steel sheet as feedstock material for indirect press hardening leads to components of very high strength with classical cathodic corrosion protection.
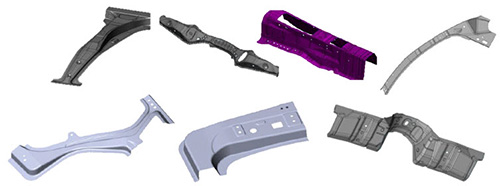
Figure 1: Press hardening-sample geometries