Abstract
Steels commonly used in the power generation industry have a finite life and are subject to the phenomena known as creep.
The materials are designed to possess specific properties to withstand loads at high temperatures over a defined period of time by creating an extremely stable microstructure that can cope with relatively extreme thermal exposure.
Steel is a major material for the construction of power generating units where it may have to withstand a temperature up to 600°C for a period of 20 to 25 years. Any material when it is subjected to load at a temperature beyond 0.4Tm (Tm denotes melting point in degree C) undergoes a time dependent deformation called creep. As a result, its load bearing capacity would decrease with time. When it falls below a specified limit it must be replaced otherwise it would fail or rupture. Therefore, a high temperature material has a finite life.
The load bearing capacity of such a material is expressed in terms of its rupture strength for a specified period at a given temperature. For example, if 100,000hr (approximately 11years) rupture strength of steel at 600°C is known to be 40MPa means it can withstand this stress for 11 years. Clearly you need very long hours of testing to evaluate the ability of steel (or any other material) to withstand high temperature. There are standard methods of accelerated testing procedures where tests are done at a little higher temperature. For example, to get an estimate of long term rupture strength at 600°C you may need tests at 650°C.
Prolong thermal exposure may favor a number of phase transformations in steel during use. This includes graphitization, coarsening of carbides and formation of new precipitates. One of the earliest creep resistant steel is one having 0.5%Mo. The structure of such steel consists of ferrite and carbide. Ferrite is no doubt stable but carbide (Fe3C) is a meta‐stable phase. It decomposes into ferrite and graphite (Fe3C = 3Fe + C). Such transformations lead to a loss of its load bearing capacity. In order to avoid this, the subsequent improved grades of steel have higher amounts of carbide forming elements. One of the most popular grades of creep resistant steel has 2.25%Cr 1%Mo. The presence of Cr in carbide increases its stability. Creep resistant steel has higher high temperature strength. Its flow stress is likely to be higher. However, ferritic steels are hot rolled when it is in austenitic state. Most of the carbides would go into solution. Therefore, its flow stress may not be very high. Nevertheless, forming of creep resistant steel is always more expensive.
To increase the steam temperature of the power boiler, creep-resistant steel for high temperature application is necessary. In addition, the length of heavy-wall steam pipe may be longer than 100 m so as to transport the high-temperature steam from the boiler to steam turbine in such a large volumetric plant. Therefore, the thermal stress induced fracture might occur due to the start-and-stop of the plant and the controlled elevation of the steam temperature. Small thermal expansion coefficients of ferritic steel can avoid thermal stress fracture. Therefore, the ferritic creep-resisant steel is always applied to the piping system. However, the creep strength of ferritic steel is relatively low compared with those of austenitic creep-resistant steels due to the high diffusion rates of transition elements in ferritic steels. The basic principles of alloy design for creep resistance are therefore well established and well founded on experience. The steels must have a stable microstructure which contains fine alloy carbides which resist the motion of dislocations; however, changes are inevitable over the long service time so that there must be sufficient solid solution strengthening to ensure long term creep deformation.
To obtain a steel that can function at the higher temperature where power plants operate without failure for extended life, pure iron is alloyed with other elements such as C, Cr, Ni, Mn, Mg, W, Ti, V, Mo, and Nb and then heat-treated to produce steel with required creep properties. Creep steels are able to survive for such long periods as 30 years because the operating temperature is only about half of the absolute melting temperature, making the migration of atoms very slow to cause any significant change in the steel microstructure.
There are three main, well-established groups of ferritic power plant steels usually designated 2, 9, and 12 wt% Cr steels. The 9–12 wt% Cr steels are currently undergoing the most research and development due to their high strength and good corrosion resistance. However, research has been done and currently going on in the development of 15Cr1Mo creep resistant steels for power plant temperatures up to 700°C.
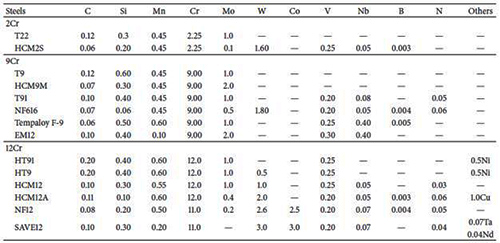
Table 1: Nominal chemical compositions (wt%) of ferritic steels.