Abstract
Copper foil manufacturing has become increasingly vital in modern electronics and industrial applications. This article examines two primary manufacturing methods: electrodeposition and rolling processes. These techniques produce copper foils with specific characteristics suited for various applications, particularly in electronic devices and printed circuit boards (PCBs). The manufacturing processes, including hot and cold rolling techniques, surface treatments, and quality control measures, are discussed in detail, highlighting their importance in meeting the growing demand for high-quality copper foils in technology applications.
Introduction
Copper, alongside aluminum, stands as one of the most versatile non-ferrous metals in industrial applications. The demand for copper foil has experienced significant growth, particularly in electronic products such as mobile phones, digital cameras, and various IT devices. This surge in demand has led to continuous improvements in manufacturing processes and quality control methods.
Manufacturing Methods
Electrodeposition Process
The electrodeposition method produces copper foils through a sophisticated electrochemical process. High-grade copper is first dissolved in an acid solution to create a copper electrolyte. This solution is then pumped into a system with partially immersed, electrically charged rotating drums. The process involves:
- A titanium rotating drum serving as the cathode
- Copper solution containing the anode
- DC voltage source application
- Controlled rotation speed for thickness management
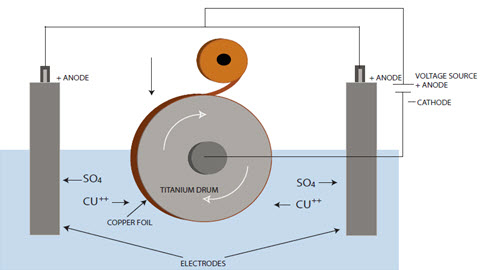
Figure 1: Electrodeposited Copper Manufacturing Process
The resulting copper foil features distinct characteristics on each side: a smooth drum side and a rougher opposite surface. The thickness of the deposit is inversely proportional to the drum's rotation speed. Surface treatments are subsequently applied to both sides to enhance adhesion properties and prevent oxidation, particularly crucial for PCB applications.
Rolling Process
The rolling method represents a more traditional approach to copper foil production.
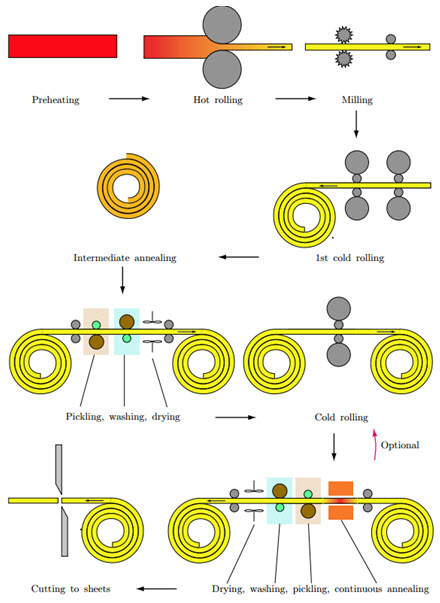
Figure 2: The rolling process of copper foils
The process involves several key stages:
- Initial heating of copper blocks (approximately 5m x 1m x 130mm) to 750°C
- Hot rolling to reduce thickness by 90%
- Scale removal through milling
- Cold rolling to achieve approximately 4mm thickness
- Heat treatment at 550°C to restore malleability
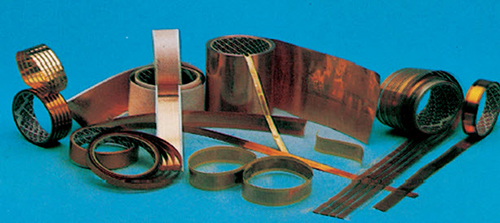
Figure 3: Copper foil products