Abstract
Cold work tool steels are specialized high-carbon steels enhanced with alloy additions including tungsten, manganese, chromium, and molybdenum. This article examines their composition, properties, and industrial applications, with particular focus on their hardenability and wear resistance characteristics. These steels offer excellent dimensional stability during heat treatment and provide cost-effective solutions for various tooling applications, operating effectively at temperatures up to 200°C. The comprehensive analysis covers different steel classifications, their constitutional properties, and specific industrial applications.
The Evolution and Significance of Electroslag Remelting Technology
Cold work tool steels represent a significant portion of tool steel production due to their cost-effectiveness and excellent dimensional stability during heat treatment. Their balanced composition of high carbon content and carefully selected alloy additions makes them particularly suitable for short-run applications where minimal distortion is crucial.
Constitution and Composition
In the annealed condition, these steels comprise ferrite and carbide, primarily Fe3C, with additional carbide formers present. Using O1 steel as an example, the manganese and chromium content in the matrix substantially increases depth hardening capabilities, enabling complete hardening in sections up to 40mm diameter.
The O series demonstrates exceptional versatility through its various grades:
- O1 steel shows reduced cracking tendency in intricate sections due to its 0.5% chromium and tungsten additions, combined with lower manganese content, which effectively restricts grain growth and controls hardening temperatures.
- O2 steel exhibits minimal movement during heat treatment, attributed to its higher manganese content and lower austenitizing temperature.
- O7 steel provides superior wear resistance within the series, though with lower hardenability, both characteristics linked to its high tungsten content.
- O6 steel features high silicon content, serving dual purposes: increasing hardenability and promoting partial carbon graphitization. This unique characteristic improves machinability in the annealed condition and enhances wear resistance when hardened. The additional 0.25% molybdenum further improves hardenability.
Table 1. Cold work tool steel types, according to the US UNS, AISI and SAE classification.
Tool Steel Type |
Prefix |
Specific Types |
Cold Work |
W = Water Hardening |
W1, W2, W5 |
O = Oil Hardening |
O1, O2, O6, O7 |
A = Medium Alloy Air Hardening |
A2, A4, A6, A7, A8, A9, A10, A11 |
D = High Carbon, High Chromium |
D2, D3, D4, D5, D7 |
Modern Applications and Requirements
Contemporary tools manufactured from cold-work steels must meet increasingly stringent requirements driven by modern production facilities and optimized manufacturing processes. Operating at temperatures up to 200°C, these steels maintain high wear resistance while providing appropriate toughness for specific applications.
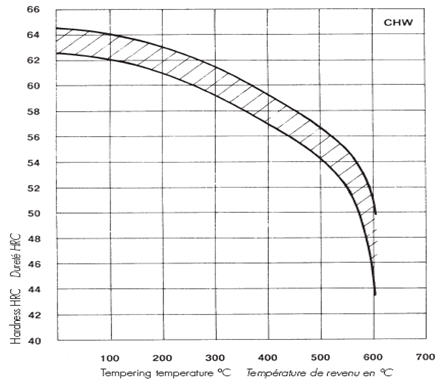
Figure 1: Tempering diagram of high chromium cold work steel X210CrW12
The alloy composition critically determines the material properties suitable for specific applications. Manufacturers carefully control the proportions of chromium, molybdenum, tungsten, and vanadium while minimizing undesirable elements to achieve optimal performance.
Industrial Applications
These steels serve in numerous applications including: Gauges, blanking dies, drawing and piercing dies, shears, forming rolls, lathe centers, mandrels, broaches, reamers, taps, threading dies, plastic molds, and knurling tools. They also find use in wire cutting operations, rolling cutters, shaping wheels for the steel tube industry, and screw manufacturing equipment.
Table 2. The common properties of cold work tool steels.
Type |
Properties |
Water Hardening Tool Steels (W series) |
- Essentially these are carbon steels with 0.60 to 1.10% carbon.
- Lowest cost tool steels.
- Soft core (for toughness) with hard shallow layer (for wear resistance).
- Use of W-series steels is declining.
|
Oil Hardening Tool Steels (O series) |
- 0.90 to 1.45% carbon with Mn, Si, W, Mo, Cr.
- They contain graphite in the hardened structure along with martensite. (Graphite acts as a lubricant and also makes machining easier.)
- Tungsten forms tungsten carbide, which improves abrasion resistance and edge retention in cutting devices.
|
Medium Alloy Air Hardening Steels (A series) |
- 5 to 10% alloying elements (Mn, Si, W, Mo, Cr, V, Ni) to improve the hardenability, wear resistance, and toughness.
|
High Carbon High Chromium Steels (D series) |
- All D-series contain 12% Cr and over 1.5% C.
- Air or oil quench.
- Low distortion, high abrasion resistance.
|