Abstract
Sinter rotary forging combines techniques of two well established other forging processes to create forged products from pressed and sintered metal powder preforms.
Sinter rotary forging has several advantages including small force requirement, good surface quality and low installation investment.
Rotary forging is a complex metalworking process in which only part of the workpiece is loaded at any instant. It offers potential advantages for the consolidation of PM workpieces:
• The nature of the incremental deformation produced means that relatively small loads are required. As illustrated in Figure 1 (see Part-1), the working zone is swept progressively through the workpiece and all elements of the material can be worked at some stage during the forming operation. In principle, the size, shape and position of the working zone can be controlled by the choice of process variables.
• Multiaxial tooling motions, offer a potential to produce component geometries which are outside the range currently available to uniaxial methods.
In order to obtain high property powder metallurgy products, at rotary forging process has often been used to further densify the sintered powder compact, but the densification law and property analysis have ever very rarely been studied, therefore the densification laws of sintered powder compacts being composed of %Fe-0.8;%Cu-4.0; %Cr-0.2 zinc stearate and formed as cylindrical shape by double action pressing, and then further densified as well in a rotary forging process was studied by orthogonal experiment and regression analysis. The experimental results presented in paper of G-C Wang, G-Q Zhao, Y.Jia, Y,Yang show that the H/D ratio and the rotary forging force are major factors affecting the density of the sintered powder compacts in the rotary forging process. The effect of the H/D ratio and the rotary forging force on the density were discovered. By determining both the density (D) and the hardness (H) of compacts, it was found that the density distributions show no differences from the hardness distributions and that the gradients of the density and the hardness in the axial direction are larger than those in the radial direction.
The rotary forging process not only has advantages such as small force requirement, good surface quality and low installation investment, but also easily makes complete densification owing to the large shearing deformation.
In order to minimize the shrinkage during sintering, FG70Cu4 is used as raw material which belongs to typical material series Fe-Cu-C used in the field of powder metallurgy. The composition of the sample was as follows Fe-0.8%C, 4.0%Cu, 0.2% Zn stearate. The samples were formed as cylindrical shape by the double action pressing in order to reduce the non-homogeneity of density. Sintering atmosphere is decomposing ammonia. The machine used in the experiment was a 300KN rotary forging press. Considering the poor plasticity and flowability of the sintered powder compacts, a set of flashes cold rotary forging dies was used.
The H/D ratio of the workpiece is a very important parameter in the rotary forging process. It affects not only the required rotary forging force but also the deformation homogeneity of the sintered powder compacts. Because the final density is affected by the non-homogeneous deformation of the sintered powder compacts in the rotary forging, the parameter H/D ratio seems very important.
Six series of different H/D ratios samples were forged on a 300KN rotary forging press under the other conditions. The curve of the density vs. H/D ratio is shown in Figure 1. The regression equation between the density and the H/D ratio is
ρ=0.95080-0.041349 ln(H/D) … (1)
The regression coefficient R=0.961362 (nearly equals 1.0) shows the accuracy of this equation is very high.
Figure 1 and Equation 1 show that the relationship between the reciprocal value of the H/D ratio and the density is logarithm, i.e. the density of the sintered powder compacts increases with the reduction of H/D ratio. When the H/D ratio is smaller than o.35, the average density can rise to 99%; when the H/D ratio is smaller than 0.25, the density can approach to 100%.
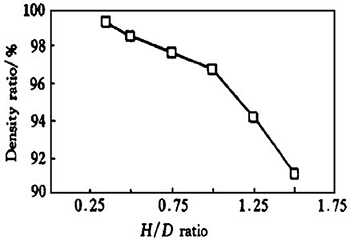
Figure 1:Relationship between density and H/D ratio
Effect of rotary forging force on density
The range value of the orthogonal experiment shows that the effect of the rotary forging force on the density is much similar to that of the H/D ratio. In the same way, seven series of samples were forged by the different rotary forging forces under the same other conditions. The curve of density vs. rotary forging force is shown in Figure 2. The regression equation between the density and the rotary forging force is given below:
ρ =p/1.008920+6.088029p … (2) where ρ is the relative density, p is the rotary forging force. The regression coefficient R=0.992417 (≈ 1.00) indicates that the imitated result is rather accurate.
Figure 2 and Equation 2 show that the density gets higher with the increase of rotary forging force. The non-homogeneity of the density becomes more difficult to eliminate with increase of the rotary forging force because of the restriction of the H/D ratio. When the rotary forging force is raised to 300KN, the density is only near 97%.
In addition, from the curve of Figure 2, we can see that the density increases fast when the rotary forging force is smaller than 200 KN and hardly increases when the rotary forging force continuously increases. The sintered powder compacts at low density are very porous. The yield stress of the compacts is very low so the yield criterion is rather easy to meet and the density increases fast. This phenomenon that the real loaded area increases with the decreases of the porosity is called “geometry-hardening”. At the same time, the work-hardening also raises the further densification forming resistance gradually with the increase of the density. Because of these two types of hardening, the density is very difficult to increase with increasing rotary forging force.
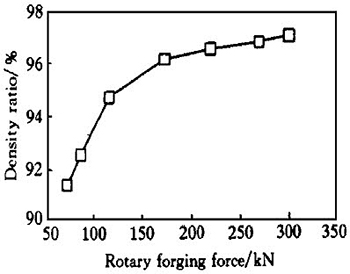
Figure 2:Relationship between density and rotary forging force