Abstract
Aluminizing is a critical thermo-chemical diffusion treatment that enhances material surface properties to prevent engineering failures. This comprehensive review examines various aluminizing techniques, including pack coating, vapor phase coating, and chemical vapor deposition (CVD). Operating at temperatures between 800-1000°C, the process involves impregnating materials' surface layers with aluminum to improve corrosion resistance, hardness, and creep resistance. The article explores both traditional high-temperature and emerging low-temperature processes, their applications in industrial settings, and the resulting material characteristics that make aluminizing essential for modern engineering applications.
Introduction to Surface Treatment
Surface properties play a crucial role in preventing engineering failures, as most material deterioration begins at the surface level. While only the surface interacts with external environments, its condition significantly impacts component longevity and performance. Various surface modification techniques exist to enhance material properties through targeted coating applications.
Fundamentals of Aluminizing
Aluminizing represents a sophisticated thermo-chemical diffusion treatment where aluminum is deliberately introduced into a material's surface layer. Though primarily applied to steels, this process also benefits nickel and cobalt-based alloys, significantly improving their creep resistance, hardness, and corrosion resistance properties.
Temperature Considerations and Process Optimization
Traditional aluminizing operates at 800-1000°C with extended soaking periods to facilitate proper diffusion. Recent research has explored low-temperature alternatives below 700°C to minimize grain growth, carbide precipitation, and material distortion. While lower temperatures reduce diffusion rates, surface plastic deformation techniques can enhance diffusion in surface and near-surface regions.
Commercial Aluminizing Techniques
Several established methods exist for commercial aluminum layer application:
- Electrolytic coating
- Cladding
- Pack aluminizing
- Gas aluminizing
- Spray metalizing
- Hot-dip aluminizing
Advanced Coating Methodologies
Pack Coating Process
This method utilizes aluminum-containing compounds within a powder mixture of aluminum oxide and an activator. The resulting metal halide vapor deposits onto the workpiece surface, creating a protective layer.
Vapor Phase Coating Technology
This advanced technique positions workpieces above donor materials, preventing surface contamination through powder contact. Vapor Phase Aluminizing (VPA) and Vapor Phase Chromizing (VPC) exemplify this methodology.
Chemical Vapor Deposition (CVD)
As the most sophisticated coating method, CVD controls deposition rates through precise temperature and gas flow management, creating protective layers either inside or outside the coating chamber.
Performance Characteristics and Applications
Key benefits include:
- Enhanced oxidation resistance
- Improved carburization resistance
- Reduced hydrogen permeation
- Superior sulfidation resistance
Primary applications include oil and gas infrastructure, industrial furnace components, and catalyst trays.
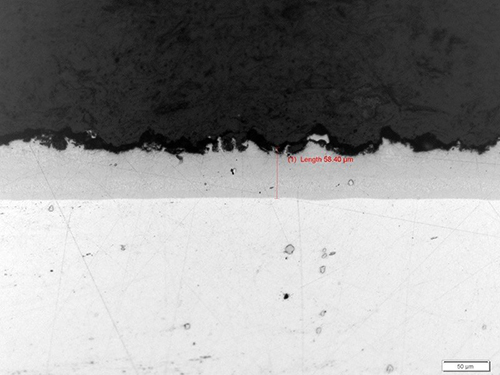
Figure 1: Aluminizing effects on Inconel 718