Abstract
Magnesium alloys have long since placed as an extremely valuable group of non-ferrous metals which allow the ever-increasing demands of light-weighting to be met, but without comprising the integrity of the project.
One method of increasing life lies in the High Velocity Oxygen Fuel (HVOF) spraying method which improves the durability and life time of machine parts, both the new and regenerated ones, by changing the surface layer properties.
In recent years, magnesium alloys have become a subject of interest in many industrial sectors, e.g. the automotive and aircraft industries as well as biomedical and mechanical engineering. Due to fact, many different applications are used to perform surface treatments and coating processes to prevent corrosion.
Coatings manufactured by thermal spraying are used to improve the durability and life time of machine parts, both the new and regenerated ones, by changing the surface layer properties.
In the field of the development of modern techniques, which improve and/or regenerate the component’s surface properties, High Velocity Oxygen Fuel (HVOF) spraying of carbides or metals and their alloys is a good alternative method to other conventional surface engineering ones, including magnesium foundry alloys. Coatings manufactured by thermal spraying are used to improve the durability and life time of machine parts, both the new and regenerated ones, by changing the surface layer properties.
As mentioned the most commonly used methods is supersonic thermal spraying of HVOF, which allows the production of coatings with special properties, among others: low oxidation, very low porosity and high adhesion. These coatings are free of oxides, which is often required due to their operational properties, and is difficult to obtain by other thermal spraying methods.
In the HVOF process, molten or partially molten material particles are sprayed onto the substrate surface with a high-speed, high-temperature gas stream. The coating material is heated and accelerated with a gas stream jet, and then hits the surface of the deposited element. In this process, the gas stream is produced by mixing and igniting oxygen and fuel (gaseous or liquid) in the combustion chamber, ensuring a rapid flow of gas under high pressure through the nozzle. The velocity of the gas stream that lifts the particles is supersonic. Particles of the coating material are introduced into the stream, heated and directed to the surface of the element. The mixture of oxygen and fuel creates high pressure in the combustion chamber, and then passing through the expanded Laval nozzle forms a shock wave. Gases that explode inside the shockwave melt the powder particles and transport it towards the substrate on which the coating is formed, see Figure 1.
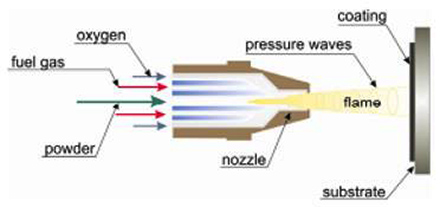
Figure 1: Scheme of the high velocity oxygen fuel (HVOF) spraying process, adapted from
What are the Advantages of Using a HVOF Coating?
Advantages of HVOF spraying over other thermal spray processes primarily relate to improved coating quality, such as:
• Higher density (lower porosity) due to greater particle impact velocities
• Higher strength bond to the underlying substrate and improved cohesive strength within the coating
• Lower oxide content due to less in-flight exposure time
• Retention of powder chemistry due to reduced time at temperature
• Smoother as-sprayed surface due to higher impact velocities and smaller powder sizes
• Better wear resistance due to harder, tougher coatings
• Higher hardness due to less degradation of carbide phases
• Improved corrosion protection due to less through thickness porosity
• Thicker coating due to less residual stresses
What are the Disadvantages of Using a HVOF Coating?
The disadvantages associated with HVOF spraying include:
• HVOF sprayed coatings can be extremely complex, with their properties and microstructure depending upon numerous processing variables
• Powder sizes are restricted to a range of about 5 - 60µm, with a need for narrow size distributions
• HVOF spraying requires experienced, qualified personnel to ensure safe operation and to achieve consistent coating quality
• As with all the thermal spraying processes, particular health and safety issues should be addressed. HVOF spraying usually needs to be undertaken in a specialised thermal spray booth, with suitable sound attenuation and dust extraction facilities
• HVOF equipment requires more investment than other thermal spraying processes, for example flame and arc spraying
• Manual operation of an HVOF spray gun is not recommended and automated manipulation of the gun is usually needed
• Deposition of coatings is difficult or impossible to achieve on to internal surfaces of small cylindrical components, or other restricted access surfaces, because HVOF spraying needs line of sight to the surface and a spray distance of 150-300 mm
In the work of E. Jonda, L. Łatka, and G. Więcław the results of HVOF sprayed coatings deposited onto AZ31 magnesium alloy substrate with a 5 mm thickness are reported. The feeding material was composite powder Cr3C2–NiCr. The feedstock material for the coatings manufacturing was Cr3C2—25 wt.% NiCr. The powder particles size distribution was in the range of −30 to + 5 μm. Before spraying all samples were sand blasted with corundum to get a surface roughness in the range of Ra equal to 17 μm. Samples for metallographic observations were prepared by standard grinding and polishing techniques. Microstructure observations were made using a scanning electron microscope, SEM (Supra 35, Zeiss, Oberkochen, Germany) using secondary electron and backscattered detectors. The coatings were investigated in terms of their microstructure and selected mechanical properties. For structure examinations, microscopy studies (light and scanning ones) were used as well as phase composition analysis.
The cross section micrographs show that obtained coatings are characterized by a homogeneous and dense structure. It was revealed that coating was well bonded to the substrate, there was no discontinuity at the interface. The porosity was low and the average pore size was also small. It could be observed, that the Cr3C2 particles were surrounded by the Ni–Cr matrix, which well adhered to the carbide particles. Figure 2 shows the cross-section of the manufactured coating.
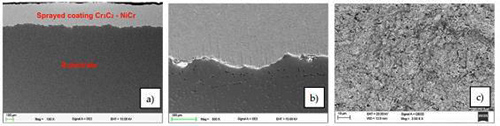
Figure 2: Cross-section of manufactured coating: (a) mag. 150×, (b) mag. 500× and (c), mag. 2500×
Based on the results of the investigations, it was found that the microhardness of the coating increases, and the maximum value is obtained as 790 HV0.3, while the minimum hardness is about 180 HV0.3, which means that the produced coating has increased in hardness compared to the substrate (AZ31) by about 338% (Figure 3.).
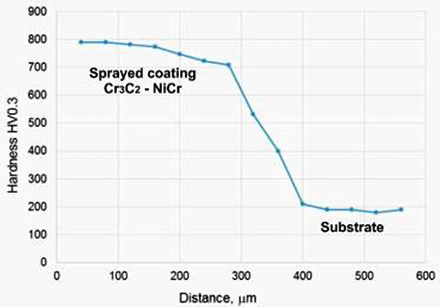
Figure 3: Hardness distribution of coated sample from the surface to substrate
Based on the carried out investigations, the following conclusions can be drawn:
1. The obtained coating is characterized by a homogeneous and dense structure, also no cracks or discontinuities were found on the surface of the produced Cr3C2–NiCr coating.
2. The thickness of the manufactured coating was about 300 ± 15 μm.
3. Measurements of the microhardness distribution in the sprayed coating indicate an increase up to 790 HV 0.3 (substrate material was equal to 180 HV 0.3).
4. In the sprayed coatings are two main phases, namely Cr3C2 and CrNi3.
5. The dominant mechanism of wear is a classic adhesive one.