Abstract
Magnesium alloys have long since placed as an extremely valuable group of non-ferrous metals which allow the ever-increasing demands of light-weighting to be met, but without comprising the integrity of the project.
Here we take a look at some of the coating technologies of Mg alloys help increase corrosion resistance and increase the overall service life of the material.
For several years, there has been a visible interest in non-ferrous alloys, including magnesium alloys, which are the subject of research in many research and development centers, as well as in major manufacturers of the machine-building, chemical, energy, textile, electronic, office, aeronautical, and in particular the automotive, shipbuilding, aviation and sports industries. The growing trends in the production of magnesium alloys indicate an increased need for their use in the global construction industry, and, thus, these alloys will become one of the most commonly used construction materials of our century, so it is extremely important to maintain a high pace of research on the problems of light alloys.
Magnesium offers a set of highly attractive properties for the manufacturing industry. The most obvious of which is magnesium’s low density, but there are many more. Magnesium has a low specific heat capacity namely 1025 J/KgK and a relatively low latent heat of fusion 368 KJ/Kg; both properties desirable for all sort of casting processes resulting in a significant reduction in energy consumption in its processing. Moreover, this element has a low affinity to steel. Due to this property, steel moulding tools used for the casting of magnesium alloys, last three to four times longer than those used to cast aluminium. Other attractive properties are excellent castability, high dimensional stability, easily predictable shrinkage, high strength-to-weight ratio, low melting temperature, shock and dent resistance, excellent damping properties, practically transparent to high energy neutron radiation, and good electromagnetic shielding. Magnesium is abundant. It is the eighth most common element; seawater, the main source of supply, contains 0.13% Mg, which represents a virtually unlimited supply. Magnesium is also recyclable, and instituting a recycling system would extend supplies and save energy.
As mentioned above, the low density of magnesium-based alloys make them attractive for the aerospace and automobile industries, although they must be balanced by their susceptibility of corrosion in aqueous environment. A number of methods to prevent magnesium alloys from corrosion or delay the speed of corrosion are used. First, corrosion of magnesium alloys can be controlled by changing the environmental factors since it usually occurs in the pH<12 moist conditions. However, environmental factors cannot be controlled in most of the times. Consequently, numerous coating technologies have been used to protect the magnesium from corrosion.
Magnesium and its alloys have been extensively studied, for their excellent physical and mechanical properties, in many countries such as USA, Japan, China, and Germany. A great number of techniques have been invented for corrosion protection and surface treatment of Mg alloys. There are a number of coating technologies related to the corrosion protection of magnesium and its alloys. These include conversion films, electrochemical plating, surface coatings and multiple surface treatments.
STATE-OF-THE-ART COATING TECHNOLOGIES
Chemical Conversion Coating Conversion coatings are superficial films of substrate metal oxides, chromates, phosphates or other compounds produced by chemical or electrochemical treating of a metal surface. The superficial films are chemically bonded to the metal surfaces. The films provide to magnesium alloys not only corrosion protection but also good paint-base properties.
Plating The plating process can be subdivided into two categories: electroplating and electroless plating. In both cases a metal salt in solution is reduced to its metallic form and deposited on the surface of a work piece. In electroplating, the electrons are supplied by an external power source. In electroless plating, the electrons are supplied by a chemical reducing agent in the solution.
Surface Coating Surface coating technologies have been used to form protective layers on substrates via thermal spraying, overlaying welding and hot-dipping. Coating layers can be metal alloys, ceramics, paints etc.
Organic Coatings An organic coating is typically used in the final stage of a coating process. It can enhance corrosion resistance or specific decoration. Organic coating involves a variety of processes such as painting, powder coating, cathodic electrocoating (E-coating ) and the application of lacquers, enamels and varnishes.
Multiple Surface Coatings A single surface treating might not meet the requirements of magnesium alloys in some working conditions. Therefore, surface treatment technologies that combining two or more kinds of surface treatment together to form multi-layer surface coating have been developed rapidly in recent years.
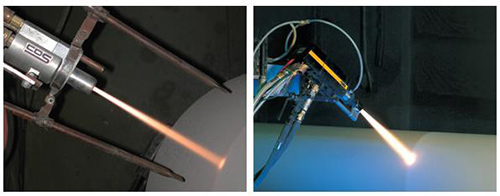
Figure 1: Advanced Spraying Coating