Abstract
Titanium alloys are becoming more widely used in a variety of industries with great advantage coming from superior mechanical and chemical properties as well as heat resistance, high specific strength and high corrosion resistance.
One specific study focusses on hardness evolution but looking at hardness characteristics for a range of specimens with varying layer thickness microhardness profiles.
Titanium alloys, thanks to their excellent strength to-weight ratio and excellent corrosion resistance, are widely used in aerospace, automotive, power plant, maritime, and many other industries.
The low surface hardness and low wear resistance limit the application of titanium alloys under conditions of friction and contact loads. Therefore, various methods for improving the surface properties and tribological characteristics of titanium alloys are applied. Tribological properties of titanium alloys may be improved or modified by coatings created on the surface, changing microstructure of surface layers or thermochemical treatments such as nitriding, carburizing, oxidizing or nitrooxidizing, etc..
In turn, nitriding of surface layers of titanium alloys is one of most widely used thermochemical treatments in the industry but all the processes of surface nitriding mentioned above have serious disadvantages. For example, plasma nitriding requires several hours of processing time. Moreover, some of the nitriding processes are performed at high temperatures, therefore the bulk of the nitrided sample or a part is exposed to high temperature, so the microstructure and mechanical properties of the bulk material can be also changed and additionally non-uniformity of surface microstructure can occur. Additionally, a serious disadvantage of the TiN coatings, reported in the literature, is poor ductility and significant reduction in fatigue wear resistance. In a case of hard coatings composed of titanium nitrides TiN deposited by PVD, CVD and plasma directly on the titanium or titanium alloy substrate, a failure at the interface between the coating and the substrate is very likely.
In the paper of A. Zhecheva, S. Malinov, experimental studies using differential scanning calorimetry (DSC) for nitriding of four titanium-alloys near α Ti–8Al–1Mo–1V, near α Ti–6Al–2Sn–4Zr–2Mo, α + β Ti–6Al–4V and near β Ti–10V–2Fe–3Al at different temperatures and for different periods of time are presented. Differential scanning calorimetry (DSC) apparatus was used for gas nitriding of all samples. The treatment was performed in pure N2 with a purity of 99.998% using a flow rate of 100 ml/min. After the nitriding experiments, the phase constitution at the surface of the samples was determined using X-ray diffraction (XRD).
Hardness evolution
In order to study the hardness behaviour in depth of the samples and the layer thickness microhardness profiles were prepared for all samples. Figure 1 presents microhardness profiles of Ti–8Al–1Mo–1V after gas nitriding at 850°C and 950°C for different periods of time. The hardness is very high in the surface layers, decreases through the diffusion zones, and approaches the basic microhardness of the matrix in the unsaturated core. The time prolongation results in an increase of the thickness of the hardened layer. The microhardness profiles (HK0.1) in the cross-sections of the Ti–6Al–2Sn–4Zr–2Mo samples are shown in Figure 2. The microhardness values increase with the time prolongation. The results for Ti–6Al–4V are presented in Figure 3. For most of the samples, the microhardness increases with the increase of the time.
The results for Ti–10V–2Fe–3Al are given in Figure 4.
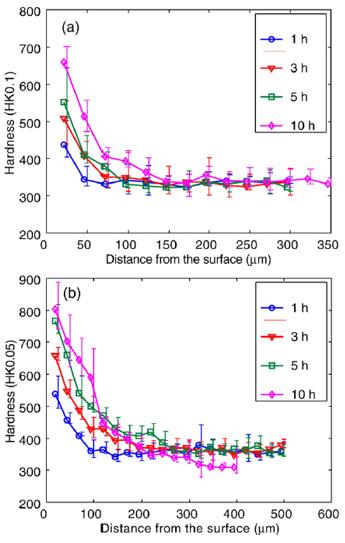
Figure 1: Microhardness profiles of Ti–8Al–1Mo–1V alloy after gas nitriding at (a) 850°C and (b) 950°C for 1, 3, 5 and 10 h.
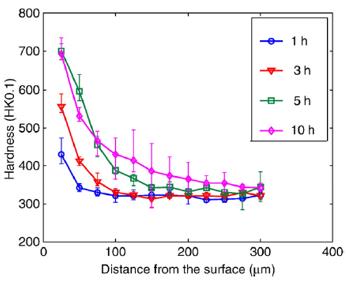
Figure 2: Microhardness profiles of Ti–6Al–2Sn–4Zr–2Mo alloy after nitriding at 850°C for different periods of time.
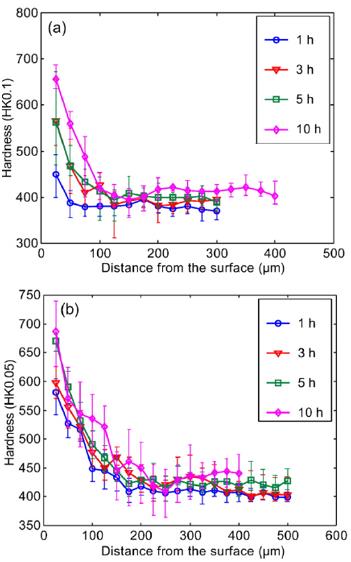
Figure 3: Microhardness profiles of Ti–6Al–4V alloy after nitriding for different periods of time at (a) 850°C and (b) 950°C.
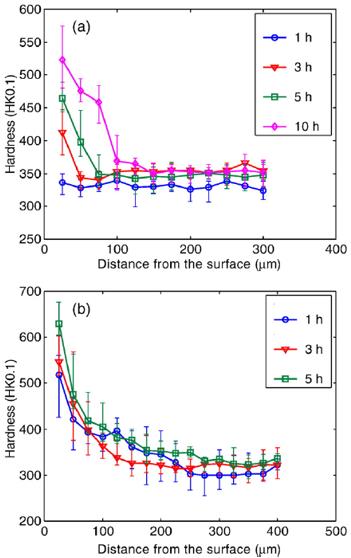
Figure 4: Microhardness profiles of Ti–10V–2Fe–3Al alloy after gas nitriding at (a) 750°C and (b) 850°C for different periods of time.
Summary and conclusions
Four commercial titanium alloys, Ti–8Al–1Mo–1V, Ti–6Al–2Sn–4Zr–2Mo, Ti–6Al–4V and Ti–10V–2Fe–3Al were gas nitrided at high temperatures of 750, 850, 950 and 1050°C in order to study and analyse the influence of the gas nitriding processing parameters on the phase modifications, the microstructural and surface morphology changes and the hardness evolution of these alloys. The results obtained in this study can be summarized as follows:
(1) The phase composition at the outmost surface layer after surface gas nitriding is α-Ti(N, O), TiN and TiO2. Titanium oxides are formed only on the surface top of the samples. Admittedly a sufficiently clean process was not achieved since significant amount of oxides were produced, but such a condition may better resemble real industrial practices where oxygen is usually present in the heat treatment systems.
(2) The microstructure of alloys nitrided at temperatures below their β transus temperatures for various periods of time is uniform and homogeneous. With the increase of the temperature to temperatures above their β transus temperatures the microstructure changes to irregular. This difference is due to the α⇔β phase transformations that appear at the higher temperatures of nitriding.
(3) The hardness values of the surface layers are very high and they decrease through the diffusion zones to approach the base microhardness of the matrix in the unsaturated core.
(4) The microhardness increases with the increase of the time and temperature of nitriding.
(5) Gas nitriding significantly increases the surface roughness of Ti–6Al–2Sn–4Zr–2Mo titanium alloy (up to the order of 21 times).
(6) The surface roughness increases with the increase of the nitriding time and there is no significant change of the surface roughness with the increase of the temperature from 950 to 1050°C.
(7) The increase of the surface roughness after gas nitriding is caused by the formation of titanium nitrides and titanium oxides on the surface of the materials.