Abstract
Lost Foam Casting (LFC), also known as Evaporative Pattern Casting, represents a significant advancement in metal manufacturing technology, particularly in the automotive industry. This process uses polystyrene foam patterns that evaporate when molten metal is introduced, creating precise, solid metal components with reduced production costs compared to conventional casting methods. LFC has gained prominence in automotive manufacturing due to its ability to produce lightweight aluminum engine components, contributing to improved fuel efficiency and reduced vehicle weight. This article explores the LFC process, its applications, benefits, and its growing importance in modern industrial manufacturing.
Introduction to Lost Foam Casting Technology
Vehicle manufacturing has become extremely complex, costly, and competitive during the past 30 years. Global competition, vehicle technology, and consumer demands have driven innovations ranging from electronic stability control to the most efficient and intricate engines ever produced. These advances in product technology necessitate corresponding advances in manufacturing processes.
A significant portion of modern vehicles sold in the U.S. feature all-aluminum engines. This lightweight metal reduces vehicle weight, increases fuel efficiency, and reduces ownership costs. Lost Foam Casting (LFC), also called Evaporative Pattern Casting, has emerged as a popular manufacturing process for these aluminum components. As the name suggests, castings are created using polystyrene foam patterns that evaporate once molten metal enters the sand casing.
The Rising Importance of LFC in Modern Manufacturing
Lost Foam Casting has grown substantially in importance over the past two to three decades. Approximately 30% of components previously manufactured through die casting are now produced using the LFC process. This shift is largely due to LFC's cost-effectiveness compared to conventional methods like sand casting.
The automotive industry has been at the forefront of LFC development, with significant research focusing on new polymers, bead expansion techniques, and optimal alloy selection. This research has yielded valuable scientific data regarding superheats, heat transfer, flow length, and other critical parameters for both cast iron and aluminum alloy applications.
The Lost Foam Casting Process Explained
The LFC process begins with creating a precise foam mold. Craftsmen cut polystyrene foam into the exact shape of the desired finished product using hand or power tools. For applications requiring exact dimensions, power tooling is preferred to ensure consistent shaping of the foam. Once shaped, the mold is thoroughly coated with materials such as sheetrock mud or plaster.
After the foam mold is completed, it is buried in a container filled with compacted sand, typically a metal drum. The ends of the foam shape remain exposed to allow the entry of molten metal. Specialized tools can enhance this process further. For example, a hinged cylinder that opens and closes along the side using long handles can be placed around the foam piece. When metal is poured, these cylinder walls contain it and allow pressure to build up, resulting in a more thorough casting.
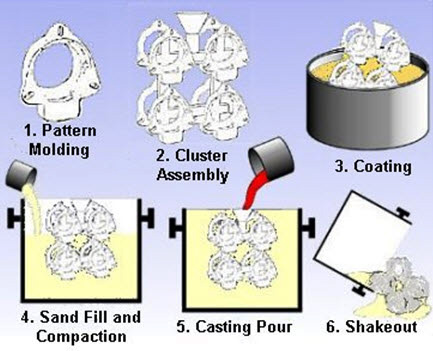
Figure 1: The Lost Foam Casting process, showing the key stages from foam pattern creation to finished metal component
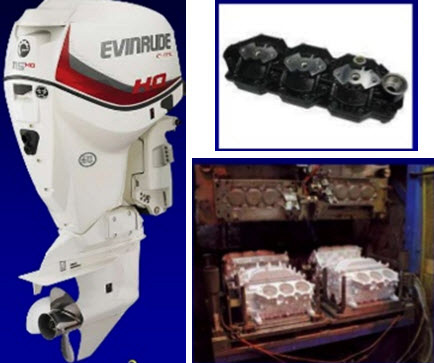
Figure 2: Lost foam casting LFC products
Industrial Applications and Key Benefits of Lost Foam Casting
Lost Foam Casting has found particular success in marine applications, where it is used to manufacture outboard engine components including engine blocks and cylinder heads. The process allows for the creation of complex, lightweight parts that are crucial for efficient marine engine operation.
The LFC process offers numerous advantages that make it increasingly attractive for modern manufacturing:
- The process requires no additives or binders, simplifying production and reducing chemical usage.
- LFC provides exceptional design flexibility, allowing for the creation of complex shapes that would be difficult to achieve with conventional casting methods.
- Traditional cores are not required, further streamlining the manufacturing process.
From a sustainability perspective, LFC generates minimum scrap and requires less machining and finishing work. This makes the process more environmentally friendly while reducing energy consumption. The smaller manufacturing footprint and reduced manpower requirements translate to operational cost savings.
Additional business benefits include reduced insurance premiums due to the safer nature of the process compared to some traditional casting methods.
Conclusion
Lost Foam Casting represents an important advancement in manufacturing technology, particularly for the automotive and marine industries. As demand for lightweight, efficient components continues to grow, LFC offers a cost-effective, environmentally friendly solution that delivers high-quality results. The continued development and adoption of this process will likely play a significant role in future manufacturing innovation.