Abstract
As technology increases to become more advanced and complex it puts an ever increasing demand on materials and their performance to keep pace.
Currently the application of high entropy alloys is restricted currently to protective coatings for high temperature components however it is a rapidly developing field which will soon diverge to cover materials which have high loading conditions coupled with extremely high temperatures.
As various technological fields like aerospace, energy, transportation and manufacturing are advancing they present new demands on materials. New materials are being sought that can be able to meet new demands presented by operating conditions in these high end applications. High strength to weight ratio, creep strength and thermal resistance are among other desirable properties in these high end applications.
Traditional commercial alloys can achieve these functions but show limitations which include a lower specific weight and high density which impact negatively on structural applications and has led to the development of High Entropy alloys as substitutes to currently available commercial alloys.
High Entropy Alloys or HEAs for short, are alloying systems composed of at least 5 elements at almost equal quantities. Their multicomponent nature, raises complexity in the system and thus makes it difficult to analyze and predict their behavior.
HEAs exhibit some quite exotic effects, most of which have only been observed in High Entropy systems. These phenomena are called “Core Effects” and they originate from complex interactions among the constituent elements. The most important of them are the “High Entropy Effect”, the “Sluggish Diffusion Effect”, the “Severe Lattice Distortion Effect” and the “Cocktail Effect”. The “High Entropy Effect” is the base on which HEAs are created.
It implies that a disordered solid solution phase can be stabilized when the entropy is sufficiently high. HEAs have an extremely high level of entropy as they are near equimolar. The “Sluggish Diffusion Effect” proposes that kinetic transformations in HEAs are very slow in comparison to conventional alloys. This is partly because of the increased activation energy for substitutional diffusion and partly due to local atomistic phenomena that eventually stall diffusion.
Furthermore, the “Severe Lattice Distortion Effect” suggests that the crystalline structure of HEAs is extremely deformed. Although disordered solid solution phases resemble common BCC, FCC or HCP structures, are altered significantly, due to the different size among constituent atoms. Finally the “Cocktail Effect” infers that the strength of a high entropy solid solution is much higher than simply the weighted average of the composing element strength. The addition of low strength and density alloying elements like Al, can actually make the system more resilient which is an additional effect originating from complex atomic interactions.
“Core Effects” endow HEAs with extraordinary properties, very useful in various applications. In general single phase FCC systems tend to be very ductile, whereas single phase BCCs exhibit increased yield strength due to a pronounced solid solution strengthening. A mixture of FCC and BCC phases takes advantage of both properties, resulting in a high strength ductile material. Precipitation of sigma phase can further increase the yield stress, however it greatly diminishes ductility.
For example, AlCoCrFeNiTi0.5 has been reported to have a yield strength of 2.26 GPa and a plasticity of 23%. Furthermore, many HEAs perform exceptionally well at elevated temperatures as a result of the decreased kinetics. They have excellent creep behavior as they are very stable and resist thermal softening, even at very high temperatures. In addition, due to their low diffusivity HEAs have found implementation as diffusion barrier coatings.
Recent studies have also shown that several HEAs are able to withstand a range of highly corrosive environments even at elevated temperatures. It should be noted that although their remarkable properties, HEAs have not yet found widespread application other than as protective coatings and high temperature components. The main reason for that is the increased cost associated with the material and the large scale manufacturing.
The development of high entropy alloys is important in solving the shortcomings of conventional alloys in applications where operating conditions of loading and temperature are extreme. The pioneering work on High Entropy alloys was in Taiwan, with the first findings on these alloys reported in 2002. High Entropy alloys are composed of at least five major metal elements and with compositions that can give a range of properties. Their definition was also extended to be an alloy with four components and one of the elements may exceed 35%. Composition of minor elements may not exceed 5%.
Generally, when a solid solution contains a high number of principal elements it has greater tendency to form solid solutions and not intermetallics or other phases. This is the basis for the design of High-entropy alloys. Unlike the design of traditional alloys which is based on adding solutes to a single ’base‘ element, High Entropy alloys are designed by choosing elements that will form solid solutions when mixed at near-equiatomic concentrations. Dependent upon their composition and processing route, High Entropy alloys possess a wide range of microstructures and properties. Those containing Fe, Mn, Cu, Cr, Co and Ni are similar to austenitic stainless steels and perform well in structural applications.
Elements that can be used in High entropy alloys are shown below in Table 2. The main constituents of HEAs comprise metallic elements can be selected form metallic group and non-metallic elements which include C, B, Si, P, S H.
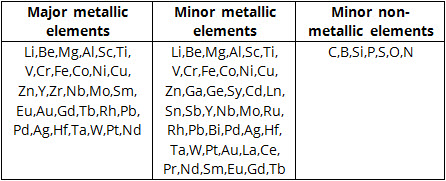
Table 2: Candidate major constituent elements for possible use in HE alloys