Abstract
This study explores sensitization in austenitic stainless steels, focusing on its causes, mechanisms, and effects on material properties. It examines the influence of thermal treatment, carbon content, and chromium levels on sensitization processes, supported by Time-Temperature-Sensitization (TTS) diagrams and experimental data from AISI 316 stainless steel. The research highlights the critical relationship between temperature ranges (500°C–800°C), cooling rates, and susceptibility to sensitization, emphasizing the chromium depletion theory and its role in intergranular corrosion. Microstructural analysis using oxalic acid etch testing confirms that sensitization varies with exposure time and material composition.
Understanding Sensitization in Austenitic Stainless Steels: Mechanisms and Effects
Sensitization represents a critical metallurgical phenomenon that significantly impacts the performance and reliability of austenitic stainless steels. This condition, characterized by increased susceptibility to intergranular corrosion, develops through specific combinations of material composition and thermal treatment. The process fundamentally alters the corrosion resistance and mechanical properties of the material, making understanding and controlling sensitization essential for industrial applications.
Factors Influencing Sensitization: Key Observations and Mechanisms
Based on comprehensive research by Atkinson and Van Droffelar (1982), several critical factors determine the development and severity of sensitization in austenitic stainless steels. The process is particularly sensitive to thermal conditions, with the temperature range of 500°C to 800°C playing a crucial role. When materials experience slow heating or cooling through this range, sensitization becomes prominent. However, rapid cooling through the same temperature range can prevent sensitization, highlighting the importance of cooling rates in material processing.
Chromium Depletion and Microstructural Changes
The primary mechanism behind sensitization involves chromium carbide precipitation at grain boundaries. This process, known as the chromium depletion theory (Miller and Boulton, 1982), leads to localized reduction in corrosion resistance. While sensitized steel may appear visually unchanged, it exhibits:
- Reduced mechanical strength
- Decreased corrosion resistance
- Loss of characteristic metallic resonance
- Increased susceptibility to cracking during deformation
Time-Temperature-Sensitization (TTS) Diagrams and Practical Applications
Figure 1: Examples of AISI 316 microstructure obtained after oxalic acid etch test a) after solution annealing (step), b) after aging 800°C/10 min. (dual), c) after aging 800°C/10 h (ditch)
TTS diagrams serve as essential tools for understanding and preventing sensitization. These C-shaped curves map the relationship between aging time and sensitization temperature, effectively separating sensitized and non-sensitized regions. For the AISI 316 austenitic stainless steel studied:
- The critical temperature (nose of the curve) occurs at 800°C
- Minimum sensitization time (tmin) is 20 minutes
- The diagrams aid in determining optimal annealing conditions
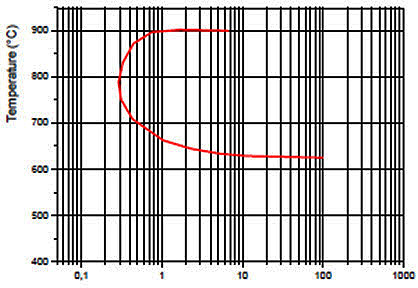
Figure 2: TTS diagram for AISI type 316 austenitic stainless steel established according to the test ASTM A262 practice A
Experimental Analysis and Methods
Table 1. Chemical composition in wt.% of austenitic stainless steel used in this study
Steel |
C |
N |
Si |
Mn |
P |
S |
Cr |
Ni |
Mo |
Fe |
AISI 316 |
0.05 |
0.032 |
0.47 |
0.86 |
0.0026 |
0.001 |
17.55 |
11.56 |
2.10 |
bal. |
The study employed rigorous testing methodologies to analyze sensitization:
- Solution annealing at 1050°C for 60 minutes followed by water quenching
- Oxalic acid etch testing (10% concentration)
- Electrolytic etching at 1 A/cm² for 90 seconds
- Microstructural examination at 250x magnification
The experimental results demonstrate clear correlations between processing conditions and sensitization susceptibility, providing valuable insights for industrial applications.