Abstract
The hydroformed part takes on the shape of the die and finally the hydroformed part can be removed.
When used with high strength steels hydroforming is able to produce structurally superior parts with thinner sections at a reduced mass.
Tube Hydroforming is a well-accepted production technology in the automotive industry while sheet hydroforming is used in selected cases for prototyping and low volume production. Research in advanced methods (warm sheet and tube hydroforming, double blank sheet hydroforming, combination of hydroforming and mechanical sizing, use of multi-point and elastic blank holders) is expanding the capabilities of hydroforming technologies to produce parts from Al and Mg alloys, as well as Ultra High Strength Steels.
A simplified overview of the hydroform process:
Raw tube is loaded into hydroforming dies → Hydroforming press closes → The sealing rods engage the part, seal the ends and fill it with water → Pressure inside the part increases → The sealing rods push the tube into the die (endfeed) and the internal pressure is ramped to its maximum value.
The hydroformed part takes on the shape of the die and finally the hydroformed part can be removed.
Figure 1 shows the steps of the hydroforming process,.whilst Figure 2 shows the same tube after hydroforming.
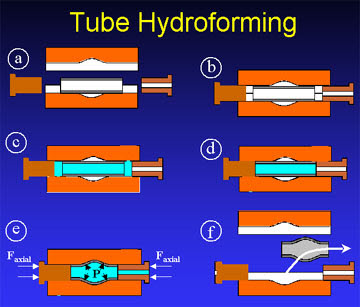
Figure 1: The steps of the hydroforming process
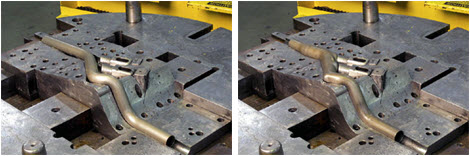
Figure 2: The tubes after hydroforming process
This method provides the following unique benefits compared to conventional technology:
- Higher precision of the part
- Complex parts produced in one single tool
- Increased possibilities for product design
- Low weight due to reduced volume of material
- Higher structural strength of the part
- Less material thin-out
- Fewer operations
- Reduced mass
- Reduced tooling costs
- Part integration and reduced part costs
- Integration of piercing and/or punching operations
- Elimination of pinch weld flange
- Improvements to dimensional repeatability
When used with high strength steels hydroforming is able to produce structurally superior parts with thinner sections at a reduced mass.