Abstract
Creating sub-microcrystal and nanocrystal materials has the potential to radically improve the characteristics of well-known metals. Severe plastic deformation production techniques promise to achieve this goal.
Enter twist extrusion of metals, one production method that uses severe plastic deformation (SPD) to change the crystalline structure of steel. Part one of this article tells you how it’s done.
Methods of severe plastic deformation (SPD), such as torsion under high pressure (HPT), 3D forging, equal-channel angular pressing (ECAP), accumulative roll bonding (ARB), cyclic extrusion and compression (CEC), repetitive corrugation and straightening (RCS), and twist extrusion (TE), are increasingly being used for the production of bulk ultrafine grained (UFG) materials.
Developing technologies to create an optimal texture in sheets can serve as an important resource for improving the properties of products in many ways. Such technological processes typically include a combination of different kinds of plastic deformation and heat treatment. For example, a bar or rod with a circular or square cross section is the final product of ECAP. This form is suitable for use in forging operations, but not suitable for obtaining sheets or plates.
It is well known that severe plastic deformation results in materials that combine high strength with plasticity. Numerous structural studies have been carried out on SPD-processed materials such as Aluminum, Titanium, Copper and their alloys. SPD is a promising method for the production of submicrocrystal and nanocrystal materials. A well-known SPD method is twist extrusion (TE).
Twist extrusion (TE) is based on pressing out a prism specimen through a die with a profile consisting of two prismatic regions separated by a twist part (see Figure 1). As the specimen is processed, it undergoes severe deformation while maintaining its original cross-section. This property allows the specimen to be extruded repeatedly in order to accumulate the value of deformation, which changes the specimen’s structure and properties. TE is performed under high hydrostatic pressure in the center of deformation. The pressure is created by applying backpressure to the specimen when it exits the die.
There are four disinct deformation zones observed when processing different materials with twist extrusion. Deformation Zones 1 and 2 are located at the two ends of the twist part of the die (see Figure 1). The mode of deformation in these zones is simple shear in the transversal plane (TP), as in High Pressure Torsion. The shears in the two zones have opposite directions. The zones appear as steps in Figure 1 ¬, which shows how the equivalent strain depends on the coordinate along the extrusion axis. Deformation Zone 3 (shown in light gray in the cross-sections in Figure 1) is located in the twist part of the die between Zones 1 and 2. The mode of deformation in Zone 3 is simple shear in the rotating longitudinal plane (LP), which is indicated by the position of the markers in the three relevant cross-sections.
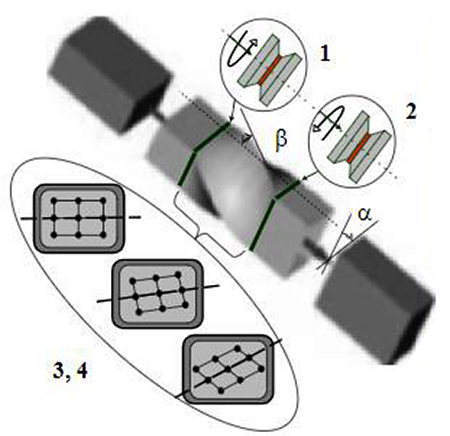
Figure 1: Twist Extrusion scheme: the four main deformation zones (1-4), inclination angle of the twist line β and rotation angle α between initial and final cross-sections of the die. The markers in the cross-sections are placed on a grid to better illustrate the shift occurring in zone 3.
There are two types of twist dies: clockwise (CD) and counter-clockwise (CCD). When transitioning from CD to CCD, the shears in each of the four deformation zones reverse its sign. This gives us two main routes of TE:
Route I: CD+CD (or CCD+CCD),
Route II: CD+CCD (or CCD+CD).
In longitudinal plane, route I gives a monotone deformation while route II gives a cyclic deformation. Different loading paths can lead to different structures and properties.