Abstract
In part two of this series we see the results of twist extrusion in microscopic detail. Two revealing studies show that twist extrusion, whether on its own or in combination with other methods, comes close to the goal of creating ultrafine-grained metals.
The twist-extruded materials surpass their untreated relatives in hardness and achieve grain structures that lead to better performance.
A paper by E. G. Pashinskaya, et al. discusses the characteristics of the formation of structure and texture in low-carbon steels subjected to warm twist extrusion (TE). A relatively new method, which makes possible a detailed study of the structure of metals, is electron backscattered diffraction (EBSD). EBSD has shown that warm TE increases the structure’s isotropy, thus leading to significant fragmentation and activation of the mechanisms of dynamic polygonization, recrystallization and grain-boundary sliding. These structural features lead to hardening of the material by 1.5 times, while maintaining a high level of plasticity.
The aim of the study was to analyze the specific features of the structure, texture and properties of low-carbon steels in various directions relative to the deformation axis during warm TE. Low-carbon construction steel was used as a test material (weight %: 0.24 C, 1.66 Mn, 1.2 Si, 0.14 Cr, 0.24 Ni, 0.01 Al, 0.06 Cu, 0.04 S and 96.41 Fe); it was annealed at 900°С (1 h) and subjected to warm TE.
A method of TE was used in which a prismatic sample is extruded through a die with a twist channel. TE was performed at a billet temperature of 400°С and the temperature of the equipment was 320°С. The extrusion pressure (P) did not exceed 1200 МРа and the applied backpressure was 100 МРа. The value of strain accumulated per pass was е ≈ 2, and the value of strain accumulated per three passes was е ≈ 6; Mechanical tests were carried out by using the upset method. A microstructural analysis was performed using transmission electron microscopy (TEM) of a carbon replica and EBSD.
The analyses of evolution of structure, presented in Figures 1(a)–1(f), demonstrate that warm TE results in substantial fragmentation of ferrite and pearlite structural components. The average grain size of ferrite, after deformation, is reduced from 15 to 5 μm. According to EBSD contrast maps, (Figures 1(а)–1(e)), it is seen that the structure after warm TE is modified. Along with fine grains, coarse uniaxial grains are observed in both longitudinal and transversal sections. TEM data (Figures 1 (b)–1(f)) show that warm TE results in the modification of perlite morphology. Cementite plates are substantially fragmented after deformation.
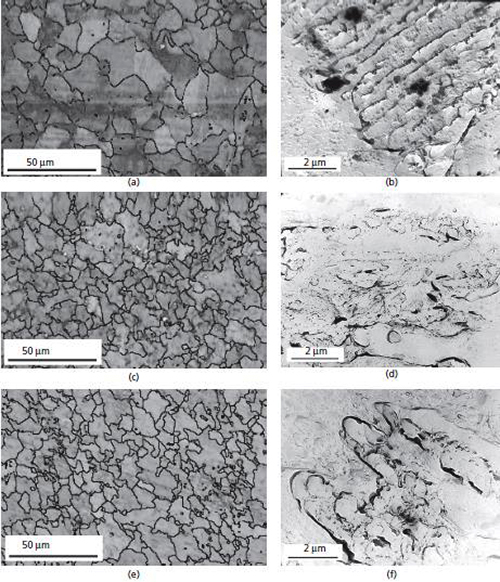
Figure 1: Microstructure of low-carbon steel 20G2S. (a, c, e) EBSD maps of band contrast; (b, d, f) TEM, ×5000; (a, b) initial state; (c, d) warm TE, cross-section; (e, f) warm TE, longitudinal section
The study demonstrates that warm TE results in the fragmentation of the structural components of low-carbon steel (i.e. ferrite and pearlite). Ferrite grains, after deformation, are reduced by a factor of 3 (from 15 to 5 μm) and characterized by a substantial share of HABs. The structure is distinguished by an un-equigranular structure with two types of grains: coarse grains of 10–30 μm in size and fine grains of 1.5–10 μm. At the same time, structural heterogeneity is observed where elongated grains, with a form factor equal to 2, prevail in the longitudinal section, contrary to the cross-section, with uniaxial grains prevailing. Also, it has been shown that, in the course of warm TE, the structure of low-carbon steel formed is affected by the sequential development of the mechanisms of dynamic recrystallization and polygonization, grain-boundary sliding and fragmentation. The structural features lead to an increase in strength by a factor of 1.5 with maintained high level of plasticity. A combination of SPD through TE and upset method gives an opportunity to achieve additional improvements in the mechanical properties.
In another study, by N. M. Shkatulyak, et al., the aim was to study the texture of low carbon steel at two stages of deformation treatment. In the first stage of deformation steel samples were subjected to TE. In the second stage of deformation the samples were subjected to cold rolling, both along and across the extrusion axis. Cast cylindrical billets of low-carbon steel (C, 0.14%; Mn, 1.66%; S, 0.035%; P, 0.035%; Ni, 0.30%; Cr, 0.30%; Cu, 0.30%) were used as starting material. The blanks were placed in a matrix with a helical channel (with parameters 𝛽max = 60° and ℎ = 50 mm). The cross section of the work piece was perpendicular to the pressing axis and constant along the axis.
The initial angle (𝛾) of helix inclination to the compression axis is zero. During the TE process this angle varies along matrix height (ℎ) (Figure 2)
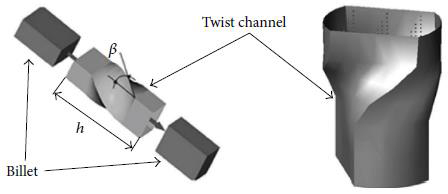
Figure 2: Circuit of processing by twist extrusion
Experimental values for inverse pole figures (IPFs) after TE of steel are shown in Figure 3. The maximal value of pole density (1.58) is observed at pole {011} on the IPF of the direction parallel to the TE axis (Figure 3(a)). The maximal pole density (1.56) also corresponds to pole {011} on the IPF of the direction perpendicular to the TE axis (Figure 3(b)). The second highest pole density corresponds to the {001} pole (resp., 1.28 and 1.33).

Figure 3: Experimental IPFs of steel after TE parallel (a) and perpendicular (b) to the axis of TE
Figure 4 shows the microstructure of extruded steel. Traces of vortex-strain are present. Images of the microstructure show that grain boundaries are tortuous and have tended to curl.
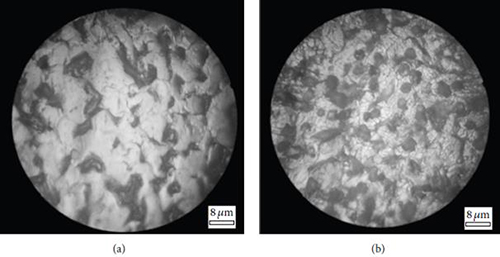
Figure 4: The microstructure of extruded steel in 2 passes: (a) parallel to the extrusion axis; (b) perpendicular to the extrusion axis