Abstract
Slag is expensive. Though it’s a byproduct, steelmakers pay for the materials and energy that produce slag, and they pay to get rid of it or recycle it. So reducing the amount of slag is a hot topic among steelmaking companies.
Several low-slag processes offer a reprieve from the slag cycle, including one that has taken over a Japanese steel firm’s entire production.
Over the past decades steel production has increased and, consequently, the higher volume of by-products and residues generated have led to the reuse of these materials in an increasingly efficient way. In recent years new technologies have been invented, and some of them are still under development, to reduce the generation rates of slag.
Most steel is produced in one of two ways:
1. Iron-ore-based steelmaking, which represents about 60-70% of world steel production. The main raw materials are: iron ore from mining sources, coal, limestone and recycled steel scrap. The main production routes are: ironmaking from iron ore using a Blast Furnace (BF), followed by steelmaking in the Basic Oxygen Furnace (BOF); and ironmaking based on Direct Reduction of Iron ore (DRI), followed by steelmaking in an Electric Arc Furnace (EAF). In the BF method coke is the reducing agent of iron ore. Limestone or dolomite (fluxes) are added into the blast furnace where they react with iron ore impurities, such as silica. Steel is produced from pig iron, scrap and lime in the BOF, where oxygen is blown to burn off the carbon.
2. Scrap-based steelmaking, which represents about 30% of world steel production. This method uses steel from recycling sources in an EAF, where the main input is steel scrap and electrical energy which is needed to melt the scrap into fresh steel.
The low-slag steelmaking process refines low-silicon hot metal (HM) in converters. Decades ago it was noticed that reducing the silicon content of hot metal was effective in controlling the slag volume of converters. Based on this observation, the slag minimum refining process (SMP), low slag process (LSP), zero slag process (ZSP) and slag recycling process (SRP) were developed in the 1980s. After the desiliconization and dephosphorization processes, the low-silicon hot metal is charged to converters, the main tasks of the converter operation were reduced to decarburization and heating. A comparison of the slag volumes and other factors from a conventional converter and the slag minimum process, when starting with hot metal with 0.11% phosphorous content is shown in Table 1. Obviously, greater economic performance can be achieved.
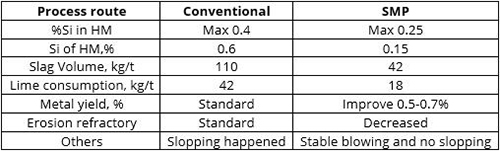
Table 1: A comparison between the conventional converter process and the slag minimum refining process (SMP) One example of these new steelmaking processes was developed by NKK (Nippon Kokan Kabushiki Kaisha) and is referred to as ZSP (Zero Slag Process). It is focused on reducing the amount of slag generated, and also stabilizing the composition of the slag, through hot metal pre-treatment.
NKK developed the Zero Slag Process (ZSP) and fully industrialized it in 1998 (see Figure 1). Hot metal in the transfer ladle is removed of silicon at the deSi station with O2 injection, then deslagged, subjected to desulfurization with KR and then to dephosphorization with deP flux blown through an immersed lance with O2 as a carrier gas. The amount of slag in the BOF after decarbonization blowing is reduced to 10 kg/t, and the total sum of the slags from deSi, deP and deC decreased to 60 kg/t, only about one half of the sum for conventional BOF operation. The operational benefits obtained were better end-point hit rate of C and T, improved iron yield and an increase in productivity of 20%. Also, the smelting reduction of Mn ore during deC blowing became favorable due to decreased loss of Mn ore in the reduced amount of slag from the BOF, which in turn decreases Fe–Mn alloy addition (38). Consequently, the annual crude steel production of 10 million tons at Fukuyama has been totally replaced by ZSP.
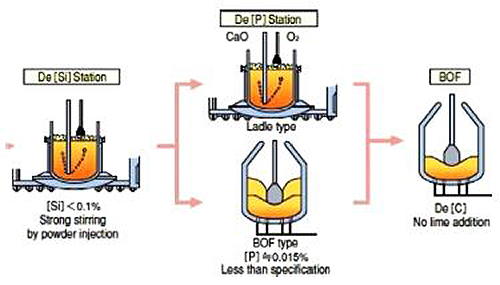
Figure 1: Zero Slag Process (ZSP) for Primary Steelmaking at NKK A thorough investigation by NKK on the dephosphorization mechanism revealed that lowering the silicon content in the hot metal to an ultimate level leads to a dramatic improvement in the efficiency of lime for dephosphorization. Based on this finding, a first in the world, an open-ladle-type desiliconization station was installed at Fukuyama Works in March 1998. The silicon content of the hot metal was minimized before dephosphorization, improving the efficiency of lime for dephosphorization. Moreover, slag generation through the entire steelmaking process was successfully lowered to an ultimate level. The phosphorous content of the steel was lowered to the level of the final product specification while still in the hot metal stage, and slag generation during dephosphorization in the converter was nearly eliminated.