Abstract
Specifically aimed at the sheet metal industry, CMT welding processes are a prospective set of methodologies where there is a deep requirement for control over welding distortions or deformations.
In comparison to a conventional pulsed arc, the droplet in CMT is notched by a current impulse, rather it is a defined rearward motion of the welding wire which brings about controlled droplet detachment.
Analysis of welded products in industry shows an important share of welding thin sheet metal. During welding, temperature variations in welds and parent metals have important effects on material characteristics, residual stresses as well as on dimensional and shape accuracy of welded products.
This is especially important in the case of thin sheet metal products, where control over welding distortions or deformations is difficult. On the other hand, in most aerospace, nuclear power plants, automobiles, boiler applications, it is extremely necessary that the fusion arc welding process has low thermal input. The Cold Metal Transfer - CMT process is considered as a prospective welding process for sheet metal industry with narrow fabrication tolerances, high demands for product quality and high productivity. To improve quality, flexibility and productivity of the welding performance, the process automatization using welding robots is important. Available information about welding parameters of the CMT process is scanty, but it is essential for programming welding robots and creating welding procedure specifications (WPS).
As mentioned above, the Cold Metal Transfer Welding is one of the potential welding processes with low heat input welding. Of course, the term “cold” has to be understood in terms of a welding process: when set against conventional GMAW, CMT-GMAW is indeed a cold process with its characteristic feature of alternating thermal arc pool, i.e. hot when an arc is initiated and cold when the arc is extinguished and the wire is retracted.
The CMT process is characterized on the innovative solution for the weld drop detachment. Unlike in a conventional pulsed arc, the droplet is notched by a current impulse, rather it is a defined rearward motion of the welding wire which brings about controlled droplet detachment (Figure 1).
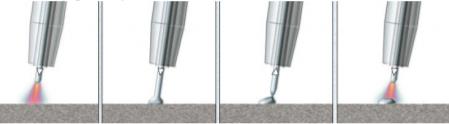
Figure 1: The principal phases in the new CMT process (from left to right)
In Figure 1 are represented the different phases that characterize this process:
- During the arcing period, the filler metal is moved towards the weld-pool.
- When the filler metal dips into the weld-pool, the arc is extinguished. The welding current is lowered.
- The rearward movement of the wire assists droplet detachment during the short circuit. The short-circuit current is kept small.
- The wire motion is reversed and the process begins all over again.
The principal innovation is that the motions of the wire have been integrated into the welding process and into the overall control of the process. Every time the short circuit occurs, the digital process-control both interrupts the power supply and controls the retraction of the wire. This forward and back motion take place at a frequency of up to seventy times per second (70Hz). The wire retraction motion assists droplet detachment during the short circuit.
UTILISATION
Materials
The CMT process has a universal range of application. The specific know-how can be used for all materials.
Applications
Whether as an automated or a manual application, the CMT Process is suitable for use in all industrial sectors: from the automotive and supplier industries to industrial plant and pipeline construction, to maintenance and repair work.
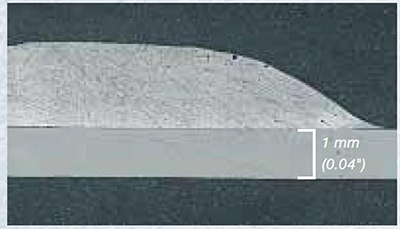
Figure 2: CMT joint between steel and aluminium. Welded on the aluminium side; brazed on the steel side.