Abstract
Sandwich panels are generally compiled by the presence of two thin but stiff and dense sheets separated by a material exhibiting lower density, strength and stiffness than the two external panels.
For sandwich panels with metallic cores there are a number of successful welding techniques which can in the end produce excellent fatigue properties.
The most common type of sandwich structure consists of two thin, stiff and strong sheets of dense material separated by a low density material which have a lower stiffness and strength compared to the materials used as top and bottom faces.
Naturally, during the production process or after welding of faceplates plates and core together, the steelx sandwich panels can also be filled with some polymer, mineral or rock wool, concrete etc. to improve the behavior for specific targets.
The type of filling material used in an application largely depends on the desired properties, fabrication method and price. The correct design of sandwich panel constructions has similar importance as the analysis of deflections, stresses and buckling loads. Furthermore designing the joint of one sandwich panel to another or to other structures is one of the key elements in the practical applications of these structures.
In Figure 1 is shown various solutions for the core profiles to be applied in steel sandwich panels.
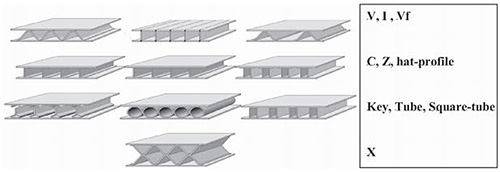
Figure 1: Various solutions for the core profiles to be applied in steel sandwich panels
In the traditional design of sandwich panels, the properties of interest in the face sheets are high stiffness to provide high flexural rigidity and high tensile and compressive strength. The properties of interest in the core are generally weaker than those in the face sheets.
Table 1 lists the results from the tensile tests on the different sandwich panel materials. The values listed in the table represent the average of five tests; the numbers in parentheses are the calculated standard deviation.
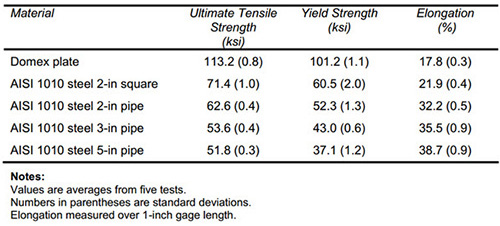
Table 1: Tensile Properties of Sandwich Panel Materials

Figure 2: A comparison of the strength to weight ratio of sandwich panels and a solid plate with equal structural properties by prof. Dan Zenkert 1998
Various manufacturing techniques, such as resistance and spot welding, weld bonding and adhesive bonding are applied for sandwich panels with metallic core. Laser welding combines high productivity and low heat input with excellent fatigue properties. Austenitic stainless steel is ideally suited for laser welding thanks to the low heat input and high welding speeds. Laser welding minimizes metallurgical changes that could impair the corrosion resistance of the weld metal. Another advantage of using laser welding austenitic stainless steels is the small weld distortion produced by the low heat input and the laser weld shape.
In the paper of J.Säynäjäkangas and T.Taulavuori it was concluded that the laser welded stainless steel sandwich panels have big potential in a wide range of attractive design solutions. The correct design of the details of the sandwich constructions is of great importance as well as the analysis of deflections, stresses and buckling loads. The joint of one sandwich panel to another or to other structures is one of the key elements in the practical application of these constructions.
The results of the studies have indicated that austenitic stainless steel grade 1.4301 (AISI 304) can be used in laser welded sandwich panels offering good mechanical properties and corrosion resistance. The use of higher strength austenitic stainless steel as sandwich panels was shown to be reasonable when substantial weight reduction of load bearing structures is desired.
In addition to laser welding the development of resistance and spot welding, adhesive bonding and weld-bonding processes will increase the variety of efficient techniques in manufacturing of stainless steel sandwich structures in the future.

Figure 3: Stainless steel corrugated core panel