Abstract
Argon Oxygen Decarburization (AOD) is a critical metallurgical refining process used primarily in the production of stainless steel and high-performance iron, nickel, and cobalt-based alloys. This technique allows for significant improvements in efficiency, mechanical properties, and cost-effectiveness. AOD facilitates the use of lower-cost raw materials, enables near-complete metal recovery, and efficiently removes impurities such as carbon and sulfur without excessive chromium loss. Since its introduction in the 1960s, the process has largely replaced traditional methods due to its technical advantages and has become the global standard for stainless steel production.
Introduction to the Argon Oxygen Decarburization (AOD) Process
Argon Oxygen Decarburization (AOD) is a specialized metallurgical process used to refine iron, nickel, and cobalt-based alloys, offering notable advantages in alloy quality and production efficiency. During this process, a molten metal charge is transferred from the electric arc furnace (EAF) into the AOD vessel. Here, impurities such as carbon and sulfur are reduced, and the final alloy's mechanical and chemical properties are significantly improved.
The AOD process enables metal producers to use less expensive charge materials while achieving near-total recovery of valuable metallic elements. It also effectively removes dissolved gases, resulting in a superior end product. Among all available refining methods in foundries, AOD stands out for its unique capabilities and efficiency.
Historical Development and Global Adoption
Invented in the United States in the 1960s, Argon Oxygen Decarburization quickly gained global acceptance due to its operational simplicity and superior decarburization efficiency. By the end of the 20th century, more than 70% of the world's stainless steel production relied on the AOD process.
The core principle behind AOD's effectiveness lies in the use of inert gases—primarily argon or nitrogen—to dilute the carbon monoxide (CO) generated during the decarburization reaction. This dilution lowers the partial pressure of CO, enhancing the reaction rate and allowing efficient carbon removal without significant chromium oxidation. This capability is vital in producing high-quality stainless steel.
Integration with Electric Arc Furnace (EAF) and Process Efficiency
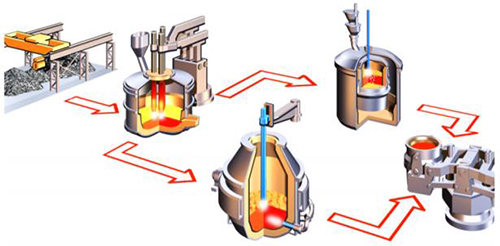
Figure 1: Typical process lines for EAF stainless steelmaking and refining of ferroalloys
AOD is typically paired with an Electric Arc Furnace (EAF) for stainless steel production. The EAF primarily melts scrap and ferroalloys, consuming about 450 kWh per ton of steel and requiring 75 to 80 minutes for a complete melt.
To reduce energy consumption and shorten processing times, some manufacturers have begun using hot metal as a raw material in the EAF. However, the higher carbon content in this hot metal demands rapid and efficient decarburization. To meet this challenge, many producers began using a top lance in the AOD vessel toward the end of the 20th century. This innovation supplies additional oxygen directly to the steel bath, accelerating the decarburization process and enhancing overall productivity.
Modern Applications and Advantages of AOD Technology
The AOD process is essential for the production of stainless, acid-resistant, and heat-resistant steel grades. One of its key benefits is that the converter treatment time under atmospheric conditions aligns closely with the casting time in modern continuous casting processes. This synchronicity ensures a streamlined and cost-effective stainless steel production cycle.
In addition to stainless steel, AOD technology is also employed in refining high-alloy steels and specialty ferroalloys. The ability to fine-tune chemical composition while minimizing material loss makes AOD a cornerstone of modern alloy production.