Abstract
Since its commercial launch in the 1980’s semi-solid processing (SSP) has offered possibilities to manufacture components from alloys which otherwise would have been impossible to achieve, in particular within the automotive and aerospace industries.
Thixocasting and rheocasting are two main routes following the SSP process and although both are confined to specific casting niches, both can produce excellent quality product with much improved mechanical properties when compared to traditional processing methods.
Semi-solid processing (SSP) of alloys has been used commercially since the early eighties for the manufacture of components in the automobile and aerospace industries. The thrust of the early development has been in aluminum and copper alloys. The nature of the process makes it an ideal candidate for the manufacture of components in alloys which are either difficult or virtually impossible to forge by conventional means. Alloys such as tool steels, stellites and superalloys, offer the possibility of a lucrative niche for commercial exploitation.
The key difference of the semi-solid process is the reduced temperature when compared to the casting of superheated melts. The generally accepted advantages of hardware performance and energy economy, achieved due to reduced operating temperatures, are universally positive for all alloys and include the following: lower energy consumption, no handling of liquid metal, longer die life, better yield from the raw material due to lower oxidation and evaporation, and fewer other losses related to melt overheating.
While these benefits are related to hardware performance, the reduced processing temperature also replaces a molten alloy with a semi-solid slurry. Then, further reduction in temperature below the liquidus changes the solid/liquid ratio and slurry properties which in turn affect the final product, not only in terms of its internal integrity, but also its microstructure.
It should be noted that semi-solid processing bases were established by studying low melting point alloys such as aluminum and magnesium alloys which are now commercialized. So far, the SSP technology has not been applied on an industrial scale for high melting point alloys such as steels, but over time there have been several key researches on several steel grades that are more likely to be processed by this new technology.
The two major routes that are used to form semi-solid metal are thixocasting and rheocasting. In thixocasting, grain–refined billets are reheated to the semi-solid range and formed into near-net-shape parts. Thixocasting can yield high-quality parts with high mechanical properties. In contrast, rheocasting involves preparing semi-solid metal from the melt using a specific technique. High feedstock material cost and high capital investment of thixocasting make it desirable only in niche applications.
Figure 1 shows a common SMM process routes.
Semisolid metal processing (SSM) or thixoforming is a new technology that offers several advantages over liquid processing and solid processing. This process utilizes semisolid behavior as well as reduces macrosegregation, porosity, and forming forces during the shaping process. A lot of research work has been carried out by various researchers in order to exploit the potential of this process to produce different products especially for the automotive industry.
In the paper of Salleh M.S. et al. the rheological behavior of aluminum alloys in semisolid slurries, thixoformability of modified aluminum alloys, the effect of feedstock production method on mechanical properties, and the importance of developing low-cost raw materials for semisolid processing are summarized.
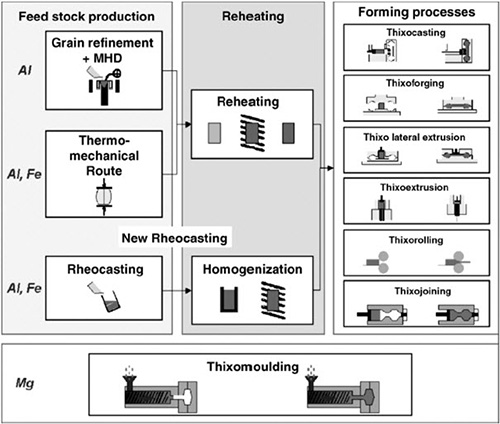
Figure 1: SMM process routes