Abstract
When bonding material through ultrasonic welding, the energy required comes in the form of mechanical vibrations.
During ultrasonic metal welding, a complex process is triggered involving static forces, oscillating shearing forces and a moderate temperature increase in the welding area.
Joining and adhesion technology is an essential technology across multiple fields. Welding in the automotive, shipbuilding and architectural industries, and brazing in electronic components manufacturing are good representative examples. Miniaturization and increased weight saving, are a continuation in the recent trend in the manufacture of electric appliances and automobiles and, in these cases, the technology for joining dissimilar materials is absolutely indispensable.
Traditionally, when joining dissimilar materials, solid phase joining or adhesion and mechanical joining are used. Solid phase joining includes various methods, such as friction welding, explosion bonding , ultrasonic welding (Imai and Matsuoka, 2005), and diffusion bonding. For example, using these methods, it is possible to join aluminum and copper together.
Bonding materials of aluminum and copper can be useful, particularly when aiming to reduce weight and increase thermal and electrical conductivity. Therefore, the application of solid phase bonding methods have been examined for the welding of aluminum and copper. At present, a novel brazing technique (Timsit and Janeway, 1993) and a method using soldering of Zn–Al alloy are influential joining methods.
Of these methods, ultrasonic welding allows relatively easy joining in a short time and with a simple facility in practically, any environment such as in water and under vacuum. Additionally, it has the important advantage of direct joining of dissimilar materials such as Cu/Al without the requirement for flux.
Ultrasonic welding is a technological process to get permanent connections. Mostly it is used to weld non- ferrous metals like coppers for example. The technology of ultrasonic welding is used in various areas but mostly in electronics, electrics industry and automotive industry. When bonding material through ultrasonic welding, the energy required comes in the form of mechanical vibrations. The welding tool (sonotrode) couples to the part to be welded and moves it in a longitudinal direction with the part to be welded onto remaining static. The parts to be bonded are then simultaneously pressed together with the simultaneous action of static and dynamic forces causing a fusion of the parts without having to use additional materials (flux). This procedure is used on an industrial scale for joining metals (figure 1).
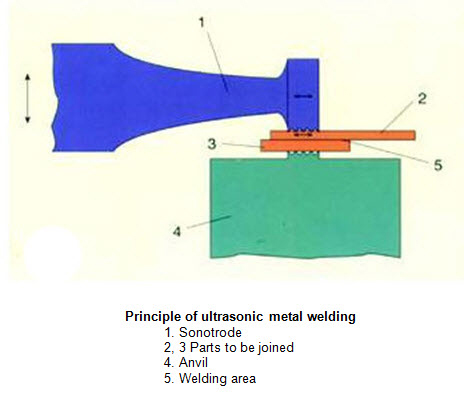
Figure 1: Ultrasonic metal welding
During ultrasonic metal welding, a complex process is triggered involving static forces, oscillating shearing forces and a moderate temperature increase in the welding area. The magnitude of these factors depends on the thickness of the workpieces, their surface structure, and their mechanical properties.
The workpieces are placed between a fixed machine part, i.e. the anvil, and the sonotrode, which oscillates horizontally during the welding process at high frequency (usually 20 or 35 or 40 kHz) (figure 1).
The most commonly used frequency of oscillation (working frequency) is 20 kHz. This frequency is above that audible to the human ear and also permits the best possible use of energy. For welding processes which require only a small amount of energy, a working frequency of 35 or 40 kHz may be used.