Abstract
Ceramic (ferrite) permanent magnetics have a range of characteristic properties. As well as displaying positive attributes in application, they also have several processing challenges associated with them.
A preferred direction of magnetization results in both oriented (anisotropic) and non-oriented (isotropic) grades being available.
The raw material of Ceramic (ferrite) permanent magnets, iron oxide, is mixed with either strontium or barium and milled down to a fine powdered form. The powder is then mixed with a ceramic binder and magnets are produced through a compression or extrusion molding technique that is followed by a sintering process.
The nature of the manufacturing process results in a product that frequently contains imperfections such as cracks, porosity, chips, etc. Fortunately, these imperfections rarely interfere with a magnet's performance.
They are charcoal gray in color and usually appear in the forms of discs, rings, blocks, cylinders, and sometimes arcs for motors.
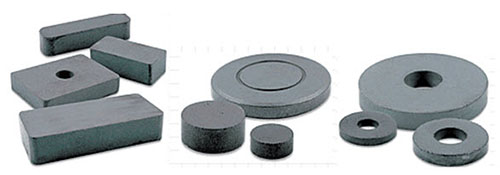
Figure 1: Ceramic magnets: a) Ceramic blocs b) Ceramic discs c) Ceramic rings
To enhance a ceramic magnet's performance, the ferrite compound may be biased by a magnetic field during the pressing process. This biasing induces a preferred direction of magnetization within the magnet, significantly reducing its performance in any other orientation.
Consequently, ceramic magnets are available in both oriented (anisotropic) and non-oriented (isotropic) grades. Because of its lower magnetic properties, the isotropic grade of ferrite, ceramic 1, is typically utilized where complex magnetization patterns are required, and in processes where biasing would be cost prohibitive.
Ceramic magnets are inherently brittle, and it is highly recommended that they are not utilized as structural elements in any application. Their thermal stability is the poorest of all the magnetic families, but they may be utilized in environments up to 300°C (570°F).
The dimensional repeatability as pressed components is difficult to control, consequently, components requiring tight tolerances necessitate secondary grinding operations to assure conformity.
Attributes of Ceramic Magnets
- High intrinsic coercive force
- Tooling is expensive
- Least expensive material compared to alnico and rare earth magnets
- Limited to simple shapes due to manufacturing process
- Lower service temperature than alnico, greater than rare earth
- Finishing requires diamond cutting or grinding wheel
- Lower energy product than alnico and rare earth magnets
- Most common grades of ceramic are 1, 5 and 8 (1-8 possible)
- Grade 8 is the strongest ceramic material available
Applications of Ceramic Magnets
Speaker magnets, DC brushless motors, Magnetic Resonance Imaging (MRI), Magnetos used on lawnmowers and outboard motors, DC permanent magnet motors (used in cars), Separators (separate ferrous material from non-ferrous), Used in magnetic assemblies designed for lifting, holding, retrieving, and separating.