Abstract
Dual phase (DP) steels represent a breakthrough material that perfectly balances mechanical properties and cost-effectiveness for the automotive industry. These high-strength steels feature a unique microstructure of hard martensite islands embedded in a soft ferrite matrix, creating materials with superior strength-to-weight ratios without sacrificing formability. Developed in the 1970s to meet automotive industry demands, DP steels continue to be essential in manufacturing vehicle components that require excellent crash resistance, formability, and weldability. This article explores the composition, microstructural features, mechanical properties, production methods, and automotive applications of dual phase steels, highlighting why they remain critical materials for lightweight, safe vehicle design.
Introduction to Dual Phase Steels
The term dual phase steels, or DP steels, refers to a class of high-strength steels composed of two distinct phases of the same alloy. Typically, DP steel contains a ferrite matrix with a dispersed second phase of martensite, retained austenite, or bainite. These steels were developed in the 1970s, driven by the automotive industry's need for high-strength materials that maintained excellent formability without increasing costs. The industry specifically demanded steel grades with high tensile elongation for formability, high tensile strength for fatigue and crash resistance, and low alloy content to maintain weldability without raising production costs. Decades later, the demand for DP steels remains strong.
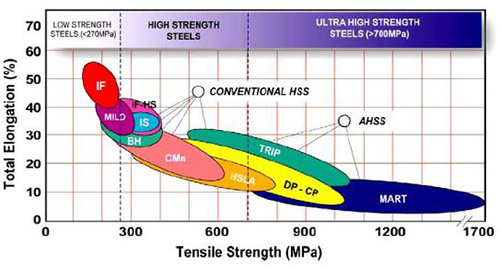
Figure 1: Strength-to-elongation relationships diagram for different steel grades
Considering their strength, formability, weldability, and cost, dual phase steel, as a category of advanced high-strength steel (AHSS), effectively meets automotive manufacturing requirements. The special microstructural characteristics—hard martensite embedded in a soft ferrite matrix—enable these steels to possess both exceptional formability and high strength.
Microstructural Composition and Development
Dual phase steels are characterized by a microstructure consisting of approximately 75-85% ferrite (alpha phase iron) with the remainder being a mixture of martensite, lower bainite, and retained austenite. Although the name "dual phase" was coined in the mid-1970s to describe ferrite-martensite microstructures, these steels usually contain more than two phases. Essentially, they are low-carbon steels that undergo thermomechanical processing to achieve better formability than ferrite-pearlite steels of similar tensile strength.
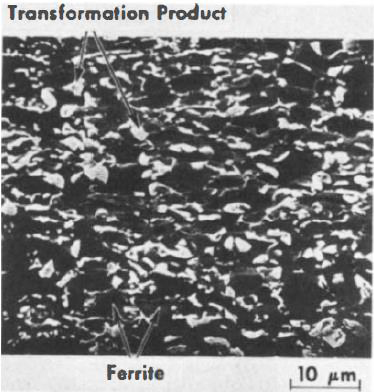
Figure 2: Scanning electron micrograph showing the microstructure of dual phase steel
Mechanical Properties and Advantages
DP steels offer unique mechanical properties due to their distinctive microstructure. These properties include:
- High strength
- Low yield-to-tensile strength ratio
- High initial work hardening rate
- Continuous yielding behavior
- Bake hardenability
- No room temperature aging effects
These characteristics primarily depend on the grain size, amount, distribution, and carbon content of the martensite phase. Compared to conventional high-strength steels and mild steel, DP steels demonstrate significantly greater strength without sacrificing formability. This combination allows for enhanced design flexibility and enables substantial thickness and weight reduction in structural components.

Figure 3: Comparison chart of different Advanced High Strength Steels
Production Methods and Variations
Dual-phase steels can be produced as both hot-rolled and cold-rolled materials. When cold-rolled, the properties develop along continuous annealing lines where there is greater control over thermal treatment. These steels can also be produced with various coatings including:
- Hot-Dip Galvanized
- Hot-Dip Galvannealed
- Electro Galvanized
Both hot and cold-rolled DP steels offer an advantageous combination of low yield strength, high tensile strength, excellent cold-working characteristics, and weldability due to their ferrite-martensite microstructure. The carbon content in dual-phase steels facilitates martensite formation at practical cooling rates, increasing the steel's hardenability. Generally, higher carbon content promotes stronger steel with a higher percentage of martensite.
In DP steels, the soft ferrite phase is typically continuous, providing excellent formability. During deformation, strain concentrates in the lower-strength ferrite surrounding the hard martensite islands, creating the characteristic high initial work-hardening rate of these steels.
Due to their high strain hardenability, dual-phase steels also exhibit excellent strain redistribution capacity. This property improves drawability and results in finished parts with higher yield strengths than the initial material. DP steels also benefit from the bake hardening effect—an important advantage over conventional HSLA materials. This effect increases yield strength during the elevated temperature aging that occurs during paint curing cycles.
DP grades can be produced with minimum tensile strengths ranging from 500 to 1200 MPa and total elongation of 5-35%.
Formability Characteristics
DP steels offer an excellent combination of strength and drawability resulting from their strain hardening capacity from the beginning of deformation. This capability ensures homogeneous strain redistribution and reduces local thinning during forming operations.
Dual-phase steels can be formed using conventional tools, provided the settings are properly adjusted. For example, drawing pressure may need to be increased by approximately 20% for a Dual-Phase 600 compared to a micro-alloyed (HSLA) steel of the same thickness.
Automotive Applications
Due to their high tensile strength, dual-phase steels are ideally suited for automobile components designed to absorb energy during impacts. These steels are commonly used in the following automotive applications:
- DP300/500: Roof outer panels, door outer panels, body side outer panels, floor panels
- DP350/600: Floor panels, hood outer panels, body side outer panels, cowl, fenders, floor reinforcements
- DP500/800: Body side inner panels, quarter panel inner parts, rear rails, shock reinforcements
- DP600/980: B-pillars, floor panels, engine cradles, seat rails
- DP700/1000: Roof rails