Abstract
HHigh chromium cast irons (HCCIs) exhibit exceptional mechanical properties and wear resistance, making them valuable for diverse manufacturing applications. A key advantage of HCCIs is their matrix structure versatility across different treatment states: austenite in the as-cast condition, pearlite after annealing, martensite following quenching, and tempered martensite after tempering. This structural flexibility, combined with their high carbide content, contributes to their superior wear resistance and mechanical performance. Heat treatment significantly influences the microstructure and corresponding properties, with tempered specimens demonstrating optimal comprehensive performance for industrial applications.
Introduction to High Chromium Cast Irons
High chromium white cast irons represent an essential category of wear-resistant materials in modern manufacturing. Their exceptional wear resistance primarily stems from their high carbide content, which forms alongside austenite during solidification as either pro-eutectic or eutectic phases, depending on the alloy composition—particularly the carbon and chromium concentrations.
The compositional range of high chromium irons suitable for wear-resistant applications typically falls within the austenitic phase field of the ternary liquidus surface on the iron-chromium-carbon diagram. Solidification occurs through a eutectic process, resulting in austenite and chromium-rich carbides of the (FeCr₇)C₃ type. In high chromium white irons with approximately 18–20 wt% Cr (hypoeutectic composition), solidification begins with the nucleation of dendritic primary austenite (γ), followed by the formation of γ + M₇C₃ carbide. This carbide morphology has been extensively documented by numerous researchers.
Microstructural Characteristics and Performance
High chromium white iron (HC-Wi) typically features an austenitic matrix structure at ambient temperature with chromium carbide dispersed throughout the matrix. The material achieves its wear resistance when abrasive particles or impact loads transform the unstable austenite into martensite through a strain-induced mechanism. This austenite-to-martensite transformation significantly increases surface hardness while reducing wear rate loss.
Carbon content plays a crucial role in multiple aspects of HCCI performance, including chromium carbide formation, carbide morphology, hardness, impact toughness, and wear resistance. Recent studies have investigated the effect of carbon content on microstructure, mechanical properties, and wear characteristics of HC-Wi compared to Hadfield steel.
Effects of Heat Treatment on Structure and Properties
In their significant research, G. Yingfeng and J. Zhanpeng conducted a comprehensive study on the structure and properties of high chromium white cast iron in different treatment states. Their findings revealed several important insights:
Matrix Structure Transformation
High chromium white cast iron exhibits different matrix structures depending on its treatment state:
- Austenite in the as-cast condition
- Pearlite after annealing
- Martensite following quenching
- Tempered martensite after tempering
All these structures contain (Fe,Cr)₇C₃ type eutectic carbide. Under the experimental conditions, heat treatment had minimal effect on the primary carbide structure. However, except for the as-cast samples, all other conditions contained secondary carbide, with martensite remaining present in both quenched and tempered states.
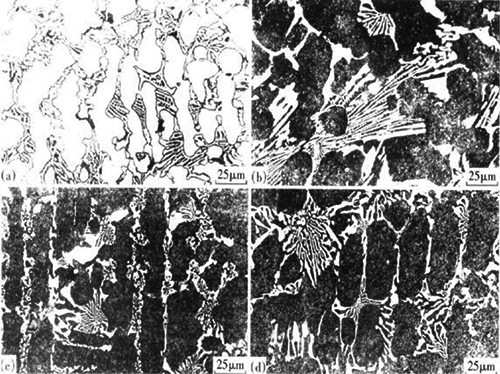
Figure 1: Metallographic structure of high chromium white cast iron in different treatment states: a-casting state, b-annealing state, c-quenching state, d-tempering state
Performance Variations with Microstructure
The performance characteristics of high chromium white cast iron vary according to its microstructure. The comprehensive performance is heavily dependent on the matrix structure. Samples in the annealed state demonstrated the lowest macro hardness, while shock tenacity values were highest in the as-cast and tempered states. Austenite showed a strong capacity to prevent crack propagation and exhibited better elasticity compared to martensite.
Optimal Heat Treatment Conditions
The researchers observed that both shock tenacity and macro hardness were higher in tempered samples compared to quenched samples. Overall, tempered specimens displayed superior comprehensive performance. Specifically, tempering at medium temperature (300°C) for a short duration (one hour) proved effective for enhancing material performance.