Abstract
Twist extrusion is a common forming method that belongs to a group of techniques known as severe plastic deformation (SPD) which are designed to generate ultrafine-grained microstructure without any changes in material geometry.
TE, specifically results in an accumulation of large strain deformation in the material, refinement of microstructure and enhancement of mechanical properties and hardness.
Severe plastic deformation (SPD) is a family of metal forming processes which uses hydrostatic pressure to impose high strain values on the material in order to generate ultrafine-grained microstructure without any changes in material geometry. It includes several different techniques such as equal channel angular pressing (ECAP), high pressure torsion (HPT), accumulative roll bonding (ARB), multi-directional forging (MDF) and repetitive corrugation and strengthening (RCS).
Twist extrusion (TE) is one of the common methods in the area of severe plastic deformation.
TE process ensures accumulation of large strain deformation in the material, refinement of microstructure and enhancement of mechanical properties and hardness, but these exceptional properties concur with heterogeneity. The novel solution for this problem is to use a conventional metal forming technique such as rolling process subsequent to TE.
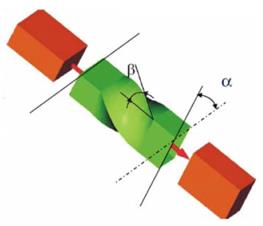
Figure 1: Schematic of the twist extrusion process
The crystallographic texture and microstructure of aluminium alloy AA6063 after twist extrusion was investigated in the paper of N. Shkatulyak.
The Figure 2 shows the structure of alloy AA6063 after twist extrusion. The traces of vortex-like strain are traced in cross-section perpendicular to the axis of pressure.
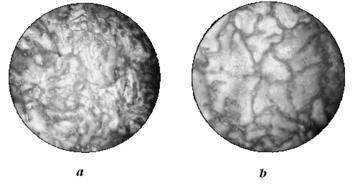
Figure 2: Structure of alloy AA6063 after 4 passes of twist extrusion. On pictures a, b is show the structures observed perpendicular and parallel to the pressure axis correspondingly. A magnification is 600x.
The experimental of inverse pole figures IPF of samples of alloy AA6063 are shown on Figure 3. The torsion axial texture with axis (1100 parallel axis of twist extrusion and vortex-like microstructure are formed during the twist extrusion. This means that the planes of type {110} coincide with the plane of shear and (uvw) crystallographic directions coincide with the shear direction. There is the gradient of texture along a radial direction of the work piece that indicates on intensification of axial texture torsion of type {110} (uvw) radially from the centre to the periphery of the work piece.
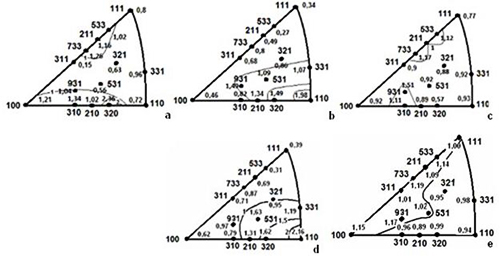
Figure 3: Experimental IPFs of alloy AA6063: a – initial sample (perpendicular to the axis of cylindrical workpiece); b, c – the central part of workpiece after TE (respectively perpendicular and parallel to the pressure axis of TE); d, e – the peripheral section of the workpiece (respectively perpendicular and parallel to the pressure axis of TE)
In the investigation of Sh Ranjbar Bahadori et al, the effects of post rolling after the twist extrusion process on commercially pure aluminum were considered. Aluminum alloy 8112 with the composition presented in Table 1 was selected for the present study. Its initial grain size was about 600 μm and an annealing treatment was performed to the as-received material (500°C for 2h), giving a grain size of about 859 μm.

Table 1: Chemical composition of commercially Al 8112
Table 2 summarizes the hardness values and the mean grain sizes of Al 8112 samples for center and edge regions in different stages. The as-annealed hardness of alloy is 39 +/- 2 HB. After employing the one pass TE, the hardness increases to 57 +/-3 HB and it enhances to 68 +/- 2 HB after cold rolling CR in the center region. The edge region hardness increases in a similar sequence from 65 +/-3 HB after twist to 72 +/-2 HB with subsequent rolling.

Table 2: The hardness values and grain sizes of Al 8112 in different stages
Figure 4 shows that after TE, the hardness values decrease from the edges towards the center encompassing a huge heterogeneity across the longitudinal section. In contrast employing CR resulted in an enhancement of the hardness and a reduction in the heterogeneity. After CR the hardness values almost approached an average value of 70 +/-2 HB throughout the longitudinal section.
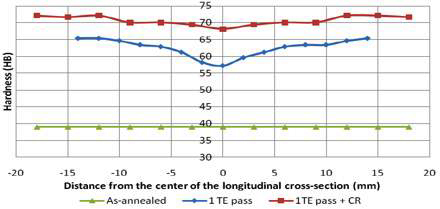
Figure 4: Hardness variations across the middle of the outer longitudinal cross-section of Al 8112 after TE and TE + CR