Abstract
Known also by a range of synonyms, Stress-Relief Cracking (SRC) is intergranular cracking in the heat affected zone (HAZ) or weld metal that occurs during exposure to in-service temperatures or post-weld heat treatments.
Although not definitive, there is general consensus that SRC is due to impurities, especially phosphorus, segregating to grain boundary/carbide interfaces or carbide-free grain boundary areas.
Stress Relief Cracking (SRC) is known by different names, viz. strain age-cracking, stress relief cracking, reheat cracking, stress assisted grain boundary oxidation (SAGBO), post weld heat treatment cracking and stress induced cracking.
Stress relief cracking is a common cause of weld failures in many creep resistant precipitation strengthened alloys.
Stress-relief cracking (SRC) is intergranular cracking in the heat affected zone (HAZ) or weld metal that occurs during exposure to in-service temperatures or post-weld heat treatments. Stress-relief cracking is often referred to as reheat cracking or post-weld heat treatment cracking. Cracking occurs along prior austenite grain boundaries. The fracture surfaces are usually smooth and featureless, but may show some cavitation and localized microvoid coalescence. SRC is observed only in those materials that undergo precipitation hardening such as ferritic creep-resisting steels, low-alloy structural steels, austenitic stainless steels, and some Ni-based alloys. For this reason, plain carbon steels do not undergo stress-relief cracking, but plain carbon steels lack the corrosion and creep resistance of the aforementioned materials. In the case of CrMo steels, reheat cracking has been shown to occur when the Cr content is approximately 3wt% or less, but has been observed in some steels containing more than 3wt% Cr. SRC occurs most often in the coarse-grained heat-affected zone (CGHAZ) due to the low ductility, high degree of grain growth, and susceptible microstructure associated with this region of a weldment. The SRC susceptibility is greatly dependent on the final microstructure which is determined by the composition and weld thermal cycle. The general mechanism of SRC in CrMo steels can be described as follows: during welding, the metal surrounding the weld pool is exposed to high temperatures and subsequent microstructural changes take place as described in previous sections. The CGHAZ experiences a temperature relatively high in the austenite region. During this time, carbides dissolve and grain growth occurs uninhibited. Because of fast cooling rates, alloying elements (vanadium, molybdenum, niobium) remain in solution and the austenite transforms to low-ductility, high dislocation density transformation products such as bainite and martensite. When the material is then exposed to a post weld heat treatment, the alloy carbides precipitate out in the grain interiors on dislocation jogs and intersections. These precipitates are usually subrnicron and are finely distributed causing considerable strengthening in the grain interiors. During tempering or PWHT, carbides precipitate and relieve some of the lattice strain from the supersaturation of carbon. It has been proposed that alloy carbide precipitation such as NbC, Mo2C, and V4C3 counterbalances the tempering effect of the precipitation of Fe3C carbides during post-weld heat treatment.
Mechanisms and controlling factors of stress-relief cracking (SRC)
As mentioned, in several precipitation-strengthened, creep-resistant steels such as the ferritic alloy steels, stress-relief cracking (SRC) is a known cause of many weld failures. SRC is generally intergranular cracking that occurs in the heat-affected zone (HAZ) or weld metal of welded assemblies during exposure to high temperature service or post-weld heat treatments (PWHT). During PWHT, residual stresses may be relieved via plastic deformation of the material. The CGHAZ is known to be the most susceptible region of a steel weldment to SRC. If a material’s microstructure has strong grain interiors that are resistant to plastic deformation along with weak grain boundaries, strain may be localized at the grain boundaries. During the arc welding process the base material closest to the fusion zone reaches temperatures close to the melting point which takes it into the austenite phase field of an Fe-C phase diagram. While in the austenite phase field, pre-existing carbides, carbonitrides, nitrides and some inclusions dissolve into the matrix and the amount of dissolution is dependent on the welding parameters. If dissolution occurs to a great extent, this allows austenite grains to grow to large sizes. During fast cooling, carbon and other dissolved alloying elements may remain trapped in solution while the austenite transforms to bainite or martensite. Upon elevated temperature exposure to PWHT or elevated service temperatures, carbides like M3C, M23C6 and M6C may precipitate out and may nucleate on dislocations within grain interiors which causes precipitation strengthening and secondary hardening. These precipitates are typically incoherent with the matrix, are stable at higher temperatures, retard dislocation movement and restrict relaxation of residual stresses. Carbides may also form on the prior austenite grain boundaries. The matrix adjacent to these boundaries may become depleted of alloying elements creating a denuded or precipitate-free zone which is softer and more ductile so strain may be localized in this region.
Some investigations have shown that one SRC mechanism is likely to be due to impurities, especially phosphorus, segregating to grain boundary/carbide interfaces or carbide-free grain boundary areas, especially under high thermal tensile stresses (developed on cooling). It was found that carbides have higher interfacial energies than grain boundaries. This means it is probable that impurities more strongly segregate to carbide interfaces than to grain boundaries and this leads to embrittlement at the carbide interfaces. The phosphorous concentration was found to be highest at the grain boundary/carbide interfaces, so it is here where intergranular cracking initiates. A precise heat treatment is recommended after the addition of intergranular carbide forming elements like titanium, vanadium or niobium in order to inhibit the formation and growth of carbides growing at the grain boundaries. Without proper PWHT, the strength of the grain boundary/carbide interfaces decreases. This decrease in strength along with the segregation leads to decohesion along these boundaries.
For illustration, in the Figures 1, is showed that for alloys with fast precipitation kinetics, cracking can occur during heating to temperatures above the precipitate solvus.
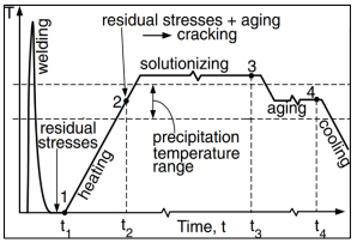
Figure 1: Schematic representation of typical thermal cycle for a weld HAZ.