Abstract
The strain induced melt activation (SIMA) process is a well-known semi-solid metal processing technology that helps to obtain a non-dendritic morphology by stirring the alloy in between the solidus and liquid point.
The SIMA process consists of four stages; casting, hot-working, cold-working and finally isothermal conditioning.
The main aim of semi-solid metal (SSM) processing is to obtain the non-dendritic morphology by stirring the alloy in between the solidus and liquid point. Semi-solid forming, which has been widely use in the field of automobile, spaceflight and aviation, is a promising method of materials processing.
Usually, the semi-solid slurry, prepared by stirring process known as rheocasting, is used directly for forming products. Thixoforming is another two step method where thixoformed feed stock is reheated to semi solid temperature to provide the SSM slurry subsequently used for component shaping.
A number of methods, such as mechanical or electromagnetic stirring, the addition of grain refining elements, spray casting, and rapid cooling, have been reported to obtain near equiaxed grain structures. Alternatively, the strain-induced melt activation (SIMA) process produces the desired structures by deformation and a following heat treatment in the mushy zone. Parameters such as heating time and temperature, and the degree of cold working, are critical factors in controlling the semi-solid microstructures in the SIMA process. It has been shown that the microstructure of an alloy prepared in the semi-solid state depends on its microstructure prior to partial remelting, so it is important to study the initial microstructure and subsequent evolution process during partial melting.
As one of the SSM process, the strain induced melt activation (SIMA) process developed by Young et. al. in 1980s is used to produce Mg alloys. This combines both casting and forging/rolling. For this method, residual strain is stored in a billet and a global structure is evolved by the strain energy stored in the billet after reheating. The process is based on scientific understanding that grain boundaries induced by plastic deformation and recrystallization will be wetted by liquid metal at the semi solid temperature, resulting in a fine and globular structure. In this study, various parameters which relate the microstructure and mechanical characteristics of thixoformed A356 alloy, such as grain size, solid fraction and shape of primary Al and morphology of silicon particles are addressed. Grain coarsening mechanism has also been discussed.
The SIMA process involves the four processing stages: casting, hot working, cold working, and recystallization and partial melting (RAP). In the SIMA process, an alloy having the sufficient stored energy by cold working is heated to a mushy zone. During heating, recovery and recrystallization occur before liquid formation with the aid of the stored energy. Reaching the mushy zone, liquid is formed by preferential melting at grain boundaries with high energy state, and penetrates into high angle boundaries of recrystallized grains. Accordingly, the amount and distribution of the stored energy by cold working is the most critical factor in the SIMA process since they control the recovery and recrystallization kinetics and the uniformity of the resultant microstructure.
SIMA process consists of four discrete stages. First the alloy is cast in convenient sizes to obtain a typical dendritic microstructure. Subsequently, it is hot worked so a directional microstructure is introduced and the thickness of the casting is decreased. The third stage involves the introduction of a critical level of stored energy in the alloy by cold working. Finally, the deformed alloy is semisolid partially remelted, and held isothermally for a short time. In SIMA, the strain is introduced into the materials through predeformation. In a general point of view, during soaking, recrystallization takes place, and once the liquid starts to form, grain boundaries are wetted and penetrated by it, leading to formation of fine equiaxed particles.
Deformation step can be carried out by some different procedures such as rolling, forging, upsetting and extrusion. All these methods have some restrictions in amount and homogeneity of the strain that can be induced in each pass. Some new technologies are under development that do not have these restrictions and can be used as commercial and engineering applications. It was well showed that in the SIMA process increasing the globalizing temperature increases the amount of the liquid at the grain boundaries. Due to the effects of surface tension and interface curvature, the convex edges of the dendrites melt and decrease the interface area of the dendrites leading to a lower free energy. Moreover, concentration of the solute in the concave parts of the grains is higher, which increases the amount of the liquid in these areas. When the liquid of the two concaves contacted with each other, the grains would separate into autonomous small grains. It should be noted that increasing the heat treatment temperature causes a further dissolution of the eutectics and spheroidization of the α-Al grains.
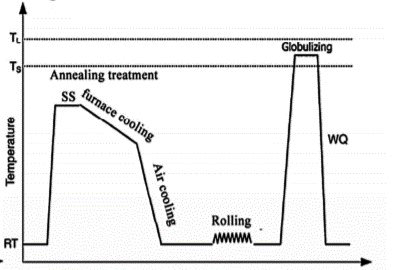
Figure 1: Schematic illustrations of SIMA Process: SS-Semi Solid, WQ-Water Quenched, RT=Room Temperature