Abstract
Sheet metal forming is one of the most significant manufacturing processes in industry today and is of particular importance in the automotive industry to drive advances in material technology and weight saving.
There are numerous forms of SMF including bending, stretch forming, and deep drawing.
Sheet metal forming is one of the most important manufacturing processes. This is particularly valid for the automotive industry where sheet metal forming has an even more important key position. The automotive industry is the leading sector in many countries and the main driving force behind sheet-metal-forming developments as well (Geiger, 2002).
The competition in car manufacturing is extremely strong leading to larger model variety and shorter model design cycles. The increased competition also leads to a very intense development activity to increase productivity and to reduce costs. Application of light-weight design principles is one of the most important trends to meet the above-mentioned requirements. Obviously, the new design concepts require new materials. The new materials often require new, innovative forming processes and new tooling concepts, as well.
The increased competition also requires to shorten the lead times from the concept to final realisation: to reduce the lead times, the application of various methods of Computer Aided Engineering (CAD/CAM/CAE and FEM techniques) are inevitable.
Sheet metal forming processes are mechanical processes, designed to make products from metal sheet without material removal, they are applied extensively by the manufacturing industry, to make products like kitchen sinks (deep drawing), tubes (roll bending), or panel sides for automotive applications (drawing/stretching).
The process is suited for mass production and products are pressed, fully automated, in large volumes with the help of mechanical or hydraulic presses. Each sheet metal forming process has its own characteristics features in terms of tooling and material flow. The set-up for a commonly applied deep drawing process is shown in Figure 1.
Thin, initially flat, sheet material is clamped between a blank holder and a forming die. The punch moves in the direction indicated by the arrow, and forces the sheet material to flow into the forming die. In this way the metal sheet is formed to a cup. Usually the sheet material is pre-coated with a metal forming lubricant to control friction and wear arises to sliding between the metal sheet and the blank holder and the forming die.
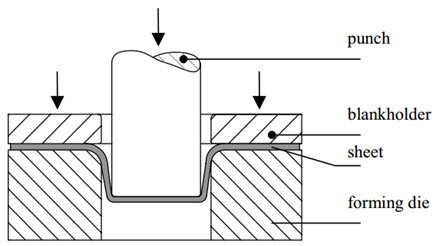
Figure 1: Deep drawing as an example of SMF-processes Bending
Bending is widely used SMF operation since different kinds of shapes are possible to produce with the same equipment. In V-shape bending the punch gradually presses the sheet into a V-shaped die see Figure 2. By stopping the process after a certain punch length different shapes can be produced.
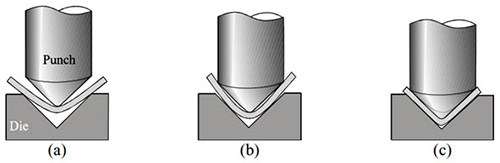
Figure 2: Schematic of the bending operation: a) free bending, b) initiating full punch and c) full punch Other types of bending operations are U-bending, roll bending and roll forming.
Stretch forming
In stretch forming the sheet (blank) is firmly clamped at its circumference after which a punch deforms the sheet, see Figure 3. The basic difference between deep drawing and stretching is that in stretching the steel sheet is not allowed to deform between the blank holder while in deep drawing the sheet deforms and slides between the blank holder.
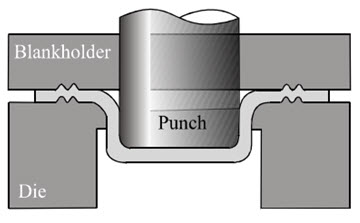
Figure 3: Schematic of the stretching process Deep drawing
In deep drawing, the sheet is clamped by a blank holder and deformed by a punch. The sheet is allowed to slide between the blank holder and the die in order to avoid wrinkling of the sheet, see region I Figure 4. In deep drawing local trybosystems and contact types can be identified. In region II the highest wear rate of the tool and the sheet is expected due to a bending and unbending deformation of the sheet and high contact pressures (P ≈ 100 MPa).
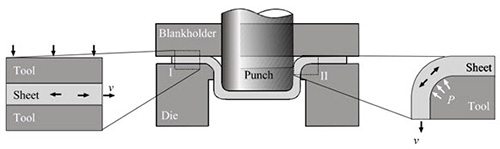
Figure 4: Schematic of the deep drawing and identified contact types