Abstract
Slag metal reactions during welding remains a complex and largely unknown subject area with regards to creating practical and effective welding consumables.
Most studies use thermodynamic considerations to understand when the most optimized temperature equilibrium is achieved, this however comes with additional issues.
Slag metal reactions are of importance in many fusion welding processes, but comparatively little is known about mechanisms which control them. The predominant reason for this is that slag-metal reactions have been associated primarily with the arc welding of ferrous materials, and they are therefore only a part of the difficult problem of developing practically effective fluxes and electrode coatings.
Most researchers of slag-metal reactions during welding have used thermodynamic considerations in their analyses and have considered reactions such as
x[M] + y[O] = (MxOy) ..... [1]
and
x[M] + y(FeO) = (MxOy) + y[Fe] ..... [2]
The equilibrium constants for the above two reactions are
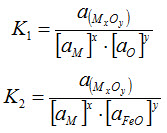
In determining the chemical composition of the weld metal and slag, researches have computed mass action indices for Equations [1] and [2]. If one assumes that an “effective reaction temperature” or pseudo-equilibrium temperature is attained during welding, these mass action indices may be related to the equilibrium constants K1 and K2.
In this way, a set of effective reaction temperatures may be obtained. A summary of such studies is shown in Table 1. Based on these results, some researchers concluded that equilibrium was attained and others maintained that the slag and metal did not reach equilibrium. In addition to the different conclusions drawn by different researchers (Table 1), these purely thermodynamic analyses have two very serious shortcomings:
(1) They do not take account of the initial compositions of the electrode and the baseplate, though these are as important as flux chemistry in determining final weld metal composition.
(2) These analyses do not take into account the influence of welding parameters, such as welding voltage, current, and travel speed, although the effect of these parameters on weld chemistry is significant, as shown in Table 2.
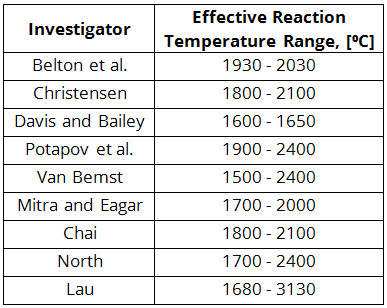
Table 1: Values of the Effective Reaction Temperature Obtained by Different Investigators
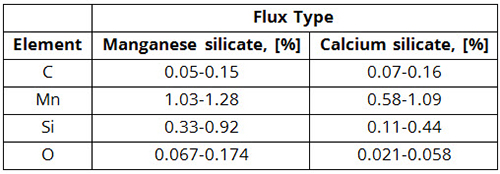
Table 2: Weld Metal Chemistry Variations Observed on Changing the Welding Process Parameters for Two Types of Fluxes
Besides the above two factors, most analyses based on metallurgical thermochemistry do not distinguish between the dependent and the independent variables. For example, if Equation [3] is used, then the amount of alloying element M (dependent variable) may be determined only if the oxygen concentration (independent variable) is known. Consequently, in view of these shortcomings, any analysis based solely on metallurgical thermochemistry cannot provide a prediction of weld metal composition with general utility.