Abstract
Sacrificial anodes are purposefully cheaper pieces of metal which are used to deflect a corrosive force away from the focus material in the structure.
For marine applications, the most common sacrificial anodes are aluminum and zinc with aluminum preferred due to longer term reliability.
Sacrificial anodes are relatively cheap pieces of metal. They are designed specifically to corrode instead of the more expensive metal parts.
The three most active materials used in sacrificial anodes are zinc, aluminum and magnesium and each have different properties and uses. The first property to consider is their electrical potential. All metals generate a negative voltage (as compared to a reference electrode) when immersed in water. The lower – the more negative - the voltage, the more active the metal is considered to be, for example:
Magnesium generates -1.6 Volts, i.e. negative 1.6 volts.
Aluminum sacrificial anode alloy generates -1.1Volts
Zinc, -1.05 Volts
Bronze generates -0.3 Volts
Steel, -0.6 Volts
Aluminum, such as that used in hulls, sterndrives or outboard motors generate -0.75 Volts.
Commercial anodes are either aluminum or zinc alloys for marine applications. Aluminum anodes have reliable long term performance, and also have better current and weight characteristics than zinc anodes. Aluminum anodes can improve the performance by controlling alloy composition. Al-Zn-In, Al-Zn-Mg and Al-Zn-Sn alloys are commonly used as sacrificial anodes in marine environments. In the paper T-M Tsai the behavior of several Al-Zn-In alloys used as anodes for cathodic protection in seawater is investigated. Table 1 shows the nominal chemical composition of Al alloy anodes in wt.% while Table 2 shows the results of performed test.
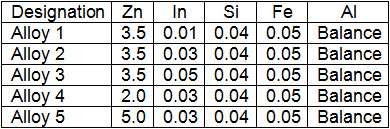
Table 1: Nominal chemical composition of investigated Al alloys
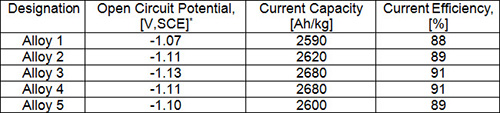
Table 2: Results of performance test
* SCE - saturated Calomel Electrode
On the basis of his investigation it may be concluded that a small amount of In (0.05%) in Al-Zn-In alloy is very beneficial. Also, the effective cathodic protection potentials for mild steel in seawater was -0.78 V,SCE for a corrosion rate less than 1 mpy. The protective area ratio of steel to sacrificial anode is determined i.e. steel can be protected under the area ratio up to 4000-5000.
On the other hand in the report of M.Funahashi and W.T.Young No FHWA-RD-98-058 for a study to evaluate the use of sacrificial cathodic protection for reinforced and prestressed concrete bridge is concluded that:
1. The aluminum – zinc-indium alloy anode provided higher current than the zinc anode. Indeed, the current output of the aluminum alloy might be more than necessary for a warm marine climate, such as Florida.
2. The current output of both anode materials fluctuated with changes in relatively humidity, temperature, and wetness of the concrete.
3. The high level of current from the aluminum alloy anode resulted in higher levels of cathode depolarization than the zinc anode. The depolarization achieved by the aluminum alloy anode exceeded 100mV during the 2-yr test period.
4. The zinc did not discharge enough current to provide depolarization levels sufficient to meet the cathodic protection criterion of 100 mV, except in wet areas and when wet conditions existed.
5. The aluminum alloy anode continued to adhere well to the piles during the 2-yr test period, and exhibited adhesion values the same as those of the zinc anodes after 2 yr.
6. Both anodes can be expected to provide a reasonable life expectancy-above 15 year at 12 mils (305 μm) thickness.
7. Topcoating of the aluminum alloy anode is not necessary, and might result in disbondment of the coating from corrosion products on the outside face of the anode.