Abstract
In the Low Frequency Electromagnetic Casting process the mold is surrounded by a coil powered by an alternating current to endue an electromagnetic field.
One of the biggest advantages of using the LFEC process in comparison to conventional casting processes is a distinct improvement in the microstructure with LFEC ingots producing a very fine equiaxed grain structure.
In a typical (semi) continuous casting process, liquid material comes from a furnace and flows down from a ladle into a tundish and is continuously melted from there into a vertical water-cooled chill mold while a solid shell of the cast material, which contains melt in its center, is simultaneously extracted from the bottom of the chill-mold.
The mold has to be an excellent thermal conductor in order to extract heat rapidly from the melt. During the passage of the material through the mold, a solid shell must be formed that is stable enough to keep its shape unchanged while it is continuously extracted vertically from the mold.
When the material shell leaves the chill-mold it enters a series of cooling zones. The cooling medium is water, which is sprayed directly on the entire periphery of the casting. The principle of semi-continuous casting is demonstrated in Figure 1 (it applies well to continuous casting also). This is the conventional casting process, often called direct-chill casting (abbreviated and used in the text as DC).
In Low Frequency Electromagnetic casting (LFEC), the mold is surrounded by a coil powered by an alternating current. The current induces an electromagnetic field in the system. Figure 2 shows schematics of the LFEC and direct-chill (DC) processes. As will be seen, the presence of an electromagnetic field significantly alters the process.
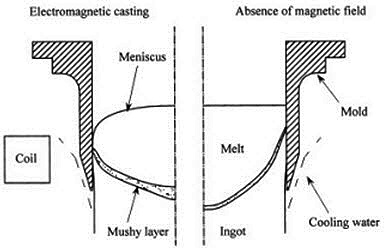
Figure 2: A cross-section schematic of the LFEC (left) and DC (right) processes. See [4] for details. In the paper of J.Cui, H.Zhang and H.Nagaumi the analyzed the effects of low frequency electromagnetic field casted of AA7055 aluminum alloy is studied on the macro-physical fields (flow field, temperature field and stress-strain field) during the semi-continuous casting process of aluminum alloys, the microstructure and crack in the ingots by the numerical and experimental methods.
Comparison of the results for the macro-physical fields in the LFEC process compared with that in the conventional DC casting process indicate the following characters due to the application of electromagnetic field: a vigorous forced convection of the melt; an entirely changed direction of melt flow; a remarkably increased velocity of melt flow; a uniform distribution of temperature; a decreased gradient of temperature; the elevated isothermal lines; the reduced sump depth; the decreased stress and plastic deformation.
Furthermore, the microstructure of the ingot is refined remarkably and the crack in the ingots is eliminated in the LFEC process because of modification of the macro-physical fields induced by the application of low frequency electromagnetic field.
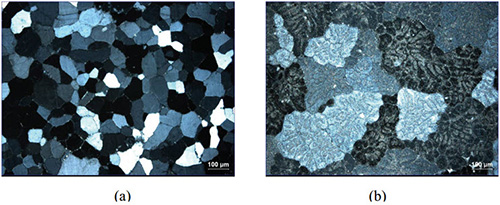
Figure 1: Microstructure of LFEC (a) and DC (b) ingots Figure 1 (a) and (b) show the microstructure of the ingots cast in the conventional DC casting and LFEC processes, respectively. It is observed from this figure that the microstructure of the ingots cast in the conventional DC casting process is usually coarse dendritic structure in the absence of the master alloy, but that in the LFEC process is very fine equiaxed grain structure.