Abstract
Studies performed by the US Army Engineering Research and Development Center (ERDC) in Vicksburg, Mississippi have demonstrated that the use of high strength rebar can build structures with increased blast resistance.
In many cases HSLA-V steels can be substituted for low carbon steels with minimal redesign. The manufacturing processes (e.g., forming, welding, etc.) remain essentially the same.
HSLA-V can be found in following applications:
- Bridges
- Suspension Components
- Building Structures
- Vehicles/Transportation
- Tubular Components
- Heavy Equipment
- Rails
- Off-shore/Platforms
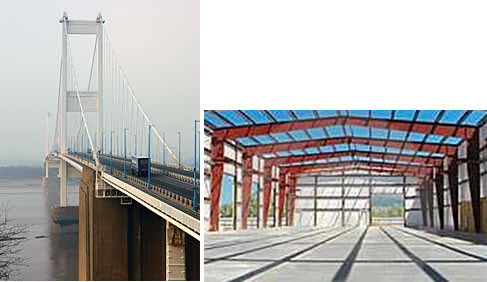
Figure 1: HSLA –V applications
Studies have shown that HSLA-V steels produce weight and cost savings for use in long-span joists, rebar-reinforced concrete, and bridging applications. Detailed experimental, computational and design studies show that long-span joists and girders can be reduced in weight by up to 25%, allowing structures to reduce their overall steel usage in girders and joists by 17% (see Figure 1). The Army are one group which take a particular interest in lightweight construction, primarily for sustainability. Doing the same job with less steel means that less energy was used to produce and transport the steel, saving money and reducing the environmental footprint of the building process. HSLA-V rebar can provide the same benefits in reinforced concrete structures: less steel for the same outcome.
Alternatively, it can provide enhanced capabilities, whereby an identical quantity of HSLA-V steel can provide more protection to the structure. Studies performed by the US Army Engineering Research and Development Center (ERDC) in Vicksburg, Mississippi have demonstrated that the use of high strength rebar can build structures with increased blast resistance. In a similar approach, the high strength rebar also enhances the earthquake resistance of the structure.
Transportation applications
Lightweight materials pay dividends over the entire life cycle of vehicles and transportation equipment, as weight reductions are a proven means to save fuel. Furthermore, the logistics of getting fuel to remote battlefields magnifies those savings and makes weight reduction a priority for the armed forces. A case study completed by a producer of high strength steel and a flatbed trailer manufacturer has shown that the use of HSLA-V steels can reduce the weight of conventional steel trailers by 21% (see Figure 2). Weight savings will reduce fuel usage every time a trailer rolls out on a mission. There are materials even lighter than HSLA-V steels that can further reduce fuel consumption, (e.g., aluminum, magnesium, and polymer composites) and the use of these materials will also continue to expand as fuel prices increase. However, HSLA-V steels still represent great value to the engineering designer and to the Army.
In many cases HSLA-V steels can be substituted for low carbon steels with minimal redesign. The manufacturing processes (e.g., forming, welding, etc.) remain essentially the same. Finally, the cost of components produced using HSLA-V steel remains about the same, since any increase per pound to use HSLA-V steel is directly offset by the fact that less steel is used. All in all, HSLA-V steels represent a great overall value to the Army.
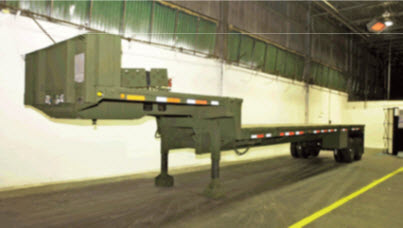
Figure 2: The use of HSLA-V steels in tactical trailer applications can reduce weight by up to 21% compared to conventional steels