Abstract
High chromium cast irons (HCCIs) are specialized ferrous alloys that demonstrate exceptional wear resistance and mechanical properties, making them vital in manufacturing and mining applications. This article examines the microstructural characteristics, mechanical properties, and effects of heat treatment on HCCIs. Through controlled heat treatment processes, these materials can be optimized to achieve enhanced strength, hardness, and ductility for specific industrial applications. The study particularly focuses on the relationship between heat treatment parameters and resulting material properties, demonstrating how proper heat treatment can significantly influence the performance characteristics of HCCIs.
Introduction
High-chromium white iron represents a crucial category of wear-resistant materials in manufacturing applications. Its widespread use in mining and minerals processing stems from its outstanding abrasion resistance, attributed to the presence of hard alloy eutectic carbides within its microstructure. These materials exhibit excellent mechanical properties, including high as-cast hardness and consistent property retention under varying conditions.
Table 1. Chemical composition of high-chromium wear resistant irons
Grade |
Content of elements / % |
C |
Mn |
Si |
Cr |
Ni |
ICHH28I2 |
2,7 - 3,0 |
0,8 - 1,4 |
0,5 - 0,8 |
28 - 30 |
1,5 - 3,0 |
ICHH15M3 |
3,0 - 3,5 |
0,3 - 0,6 |
0,5 - 0,9 |
12 - 18 |
- |
ICHH14G2N |
2,0 - 2,4 |
0,5 - 0,7 |
1,8 - 3,2 |
13 - 15 |
1,2 - 2,0 |
Microstructural Characteristics and Properties
The mechanical performance of HCCIs is primarily determined by several key factors: the type, size, quantity, and morphology of hard carbides, combined with the matrix structure (γ or α). For wear-intensive applications, hypereutectic HCCI containing large volumes of hard carbides is preferred. However, it's important to note that coarser primary M7C3 carbides, which form during hypereutectic alloy solidification, can potentially compromise wear resistance.
Industrial Applications and Performance
HCCIs have established themselves as essential materials in mining, milling, earth-handling, and manufacturing industries, where exceptional wear and corrosion resistance are paramount. Their superior wear resistance stems from the high volume fraction of hard chromium carbides, complemented by matrix toughness. The carefully controlled chromium content serves dual purposes: inhibiting graphite formation and stabilizing carbides.
Table 2. Heat treatment parameters for individual samples
No. |
Sample name |
Hardening |
Tempering |
Soft annealing |
0 |
Beta |
As cast |
1 |
Beta1 |
930°C/ 7h/ air |
500°C/ 3h/ air |
950°C 1h/ cooling to temp 810°C during 1h/ cooling to temp 600°C for 2h/ air cooling |
2 |
Beta2 |
950°C/ 7h/ air |
3 |
Beta3 |
970°C/ 7h/ air |
4 |
Beta4 |
1000°C/ 7h/ air |
5 |
Beta5 |
1050°C/ 7h/ air |
Heat Treatment Effects and Optimization
Recent research by D. Kopyciński et al. has provided valuable insights into heat treatment effects on HCCI properties. Their study, conducted on cast samples, investigated various hardening temperatures followed by tempering and soft annealing processes.
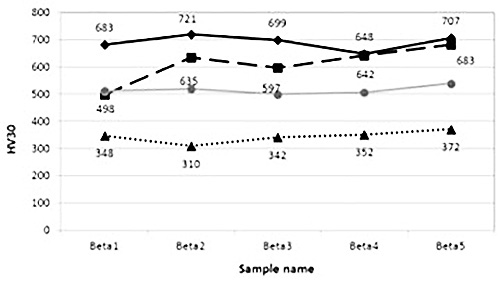
Figure 1: The Vickers hardness of the samples tempering and soft annealing, and as-cast
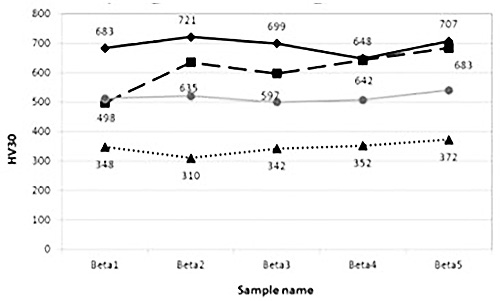
Figure 2: The Rockwell hardness of the samples after hardening, tempering and soft annealing, and as-cast
Results and Conclusions
The research demonstrates that precise control of heat treatment parameters enables customization of hardness and microstructural composition. While hardening enhances casting hardness, tempering and soft annealing improve ductility. Optimal properties were achieved with hardening at 950°C, with higher temperatures resulting in hardness exceeding 60 HRC units.