Abstract
High carbon steel, containing 0.60-1.00% carbon and 0.30-0.90% manganese, is a crucial material in industrial applications requiring superior strength and wear resistance. This article examines the properties, microstructure, and applications of high carbon steel, highlighting its advantages and limitations. While offering exceptional hardness and wear resistance, these steels present reduced ductility and weldability compared to mild steel. The article also explores various industrial applications and manufacturing standards, emphasizing the balance between carbon content and desired material properties.
Introduction to High Carbon Steel Composition
High carbon steels typically contain 0.60 to 1.00% carbon with manganese contents ranging from 0.30 to 0.90%. The distinctive pearlitic microstructure of these steels results in exceptional hardness, though this comes with increased brittleness and reduced ductility compared to mild steel variants.
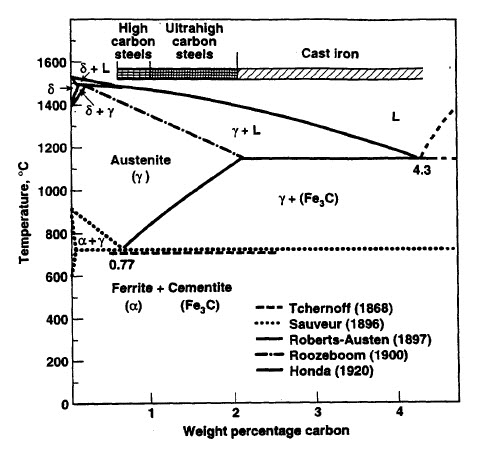
Figure 1: Historical Description of the Fe-C phase diagram
Properties and Microstructural Characteristics
The microstructure of high carbon steel with approximately 0.8% carbon content consists primarily of pearlite, a fine mixture of ferrite and iron carbide. This structure appears as a characteristic "wormy" texture under microscopic examination. While the fine pearlitic structure provides excellent hardness and wear resistance, it simultaneously reduces the material's ductility and impact resistance.
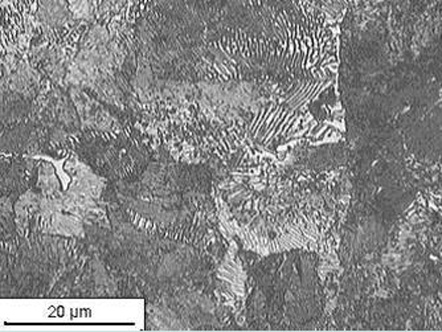
Figure 2: Microstructure of high carbon steel
Industrial Applications and Performance
High carbon steels excel in applications demanding superior strength, hardness, and wear resistance, including:
- Cutting tools and chisels
- Spring materials and high-strength wires
- Railway wheels and rails
- Gear wheels and chains
- Saw blades and shear blades
- Wire rope and tire reinforcement
- Pre-stressed concrete applications
Manufacturing Standards and Specifications
Common standards for high carbon spring steel wire include:
- ASTM A-227 Class I/II
- ASTM A-417 Class I/II
- ASTM A-407 Type A/B/C/D/E/F/G/H
- ASTM A-228 Music Wire
Performance Optimization
To maximize performance in specific applications, manufacturers often increase carbon content to the highest practical level. However, this optimization must consider application-specific limitations:
- For forging steels: toughness and weldability constraints
- For high-strength wire: eutectoid carbon level limitations
- For wear-resistant applications: balance between hardness and brittleness