Abstract
Explosive welding was first exploited commercially during the 1960’s and is a form of impact welding which can specifically useful to join dissimilar materials with large surface areas.
General applications of explosive welding include joining pipes, remote joining in hazardous environments and most importantly the joining dissimilar materials for a range of applications.
Explosive welding was first exploited commercially during the 1960’s and is a form of impact welding which can specifically useful to join dissimilar materials with large surface areas.
A schematic diagram in Figure 2 shows the basic components for EXW. The explosive detonation is normally initiated at a point or along a line, and the relative velocities, between the explosive detonation front velocity and the flyer plate downward velocity, set the contact angle upon impact.
Changing initial standoff (the distance between the flyer plate and the target plate) can change the impact velocity and angle. The collision takes place across the entire surface along an impact line that moves from the detonator and produces the plasma jet. The jet atomically removes the oxide and cleans the surface.
The main process parameters for EXW include the surface finish and cleanliness, the placement of the detonator, the standoff distance, and the characteristics of the explosive used, particularly its detonation velocity and the pressure produced. These controlled variables are responsible for the impact velocity and impact angle that is developed.
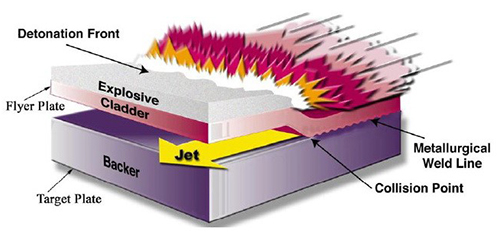
Figure 2: Schematic Diagram of EXW Process. Jet was generated from the collision point and propagated along the welded interface.
The advantages of explosive welding over conventional welding techniques are as follows:
- Used to join dissimilar metals.
- Achieves high bond strength.
- Maintains parent metal qualities.
- Achieves welds over large areas.
- Requires low capital outlay.
- Produces minimal distortion of parent metals.
- Enables remote welding to take place.
- Enables welding in hostile environments.
Also, the following adventages should be mentioned:
- Can bond many dissimilar, normally unweldable metals.
- Minimum fixturing/jigs.
- Simplicity of the process.
- Extremely large surfaces can be bonded.
- Wide range of thicknesses can be explosively clad together.
- No effect on parent properties.
- Small quantity of explosive used.
Usuall Applications are:
- Joining of pipes and tubes.
- Major areas of the use of this method are heat exchanger tube sheets and pressure vessels.
- Tube Plugging.
- Remote joining in hazardous environments.
- Joining of dissimilar metals - Aluminium to steel, Titanium alloys to Cr – Ni steel, Cu to stainless steel, Tungsten to Steel, etc.
- Attaching cooling fins.
- Other applications are in chemical process vessels, ship building industry, cryogenic industry, etc.
Limitations of the process are:
- The metals must have high enough impact resistance, and ductility.
- Noise and blast can require operator protection, vacuum chambers, buried in sand/water.
- The use of explosives in industrial areas will be restricted by the noise and ground vibrations caused by the explosion.
- The geometries welded must be simple – flat, cylindrical, conical.