Abstract
The explosive bonding of materials uses the substantial energy of a detonation to bond similar or dissimilar materials together.
The technique has several key associated benefits besides the flexibility of joining different materials together including high strength, resistance to abrasion and corrosion, and increased toughness.
The explosive welding process is capable of joining high surface areas due to its ability to distribute high energy density through explosion. Up to now, similar metals (low carbon steel, steel to steel, Al–Al, stainless steel to steel) , dissimilar metals such as steel and aluminum , steel and titanium, nickel film and aluminum alloys , iron and copper , aluminum, copper and magnesium , copper, titanium and steel , aluminum and copper and also metallic glasses were cladded successfully.
At the collision point of the two material plates, a metallic jet is formed. Numerous methods of coatings on materials by explosion have been applied because the cladding methods basically give good advantages.
One of them is achievement of high strength, resistance to abrasion and corrosion, or toughness in the applied surface layer of material, with the complete finished product being able to be made from several different materials.
Bonding methods also significantly reduce material costs. For example the production of a so-called welding heat exchanger is one of possible areas of explosive welding application. Generally, the welding connectors are metal composites having e.g. steel layer on one side and titanium alloy layer on the other.
Over 260 various similar and dissimilar metal and alloy combinations can be welded by using explosive welding techniques. Explosive selection and detonation velocity are important to obtain good welds.
The collision velocity Vc and the plate velocity Vp should be less than the velocity of sound in either welding component. The velocity of sound in engineering materials is typically 4.5–6 km/s, whereas the detonation velocity in common explosive (plastic explosive) is typically 6–7 km/s.
The work of D. Ostroushko, and E.Mazancová reports results of the investigation of the microstructure-properties relationship in explosively welded duplex stainless steel-steel on the as clad condition. There is only a small amount of information about the anticorrosion Cr18Ni10 steel-titanium sandwich available and hence why the presented work is focused on some metallographic parameters and fatigue response after explosion bonding and after followed heat treatment (HT).
The experimental works were focused on the investigation of micro-structure and mechanical properties after explosion bonding and the subsequent heat treatment (HT). Investigation of micro-structure using light microscopy methods was completed including grain size, wave amplitude, period and total waves length.
Further on, an analysis of fatigue crack propagation was carried out. It showed that in the samples without HT the crack propagates right to the basic material at lower stresses. Under higher loadings the crack only propagates to the weld and then continues along the welded joint.
In a sample with the HT at higher stresses the situation is the same as in the material without HT. Under lower stresses the crack does not propagate into the basic material as distinctly as in the sample without the HT.
Through explosive welding the materials are joined by the pressure generated at detonation of an explosive placed on the top of surface of the welded material as can be schematically seen in Figure 1. Where Vv represents velocity of the air, Vk the rate of impact, Vd velocity of explosion and Vc the velocity of welding. The β expresses angle of material welding.
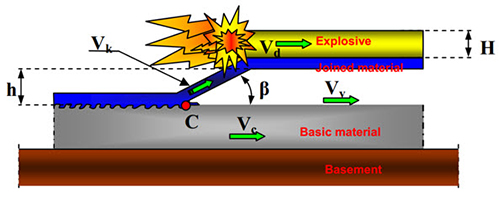
Figure 1: Course of explosive In the work by the above mentioned authors, relating to the study of Cr18Ni10 stainless steel and titanium matrix welded by explosion were used. Titanium was of a commercial grade and the anticorrosion steel had the following chemical composition (in wt. %): 0.04C, 0.45Si, 1.96Mn, 18.42Cr, 9.74Ni, 0.065P and 0.011S.
The samples of stainless steel and titanium sandwich were machined by mechanical cutting to avoid any change in microstructure. The thickness of the anticorrosion steel and the titanium layer corresponded to 110 mm and to 6 mm (given in sequence). For metallographic evaluation of microstructures, including micro-joints in the welded area, samples of dimension 20 x 20 x 40 mm were made. For fatigue evaluation joint test bars in the shape of fries of the dimensions 12 x 10 x 100 mm were prepared.
Five samples were used after the following heat treatment (HT) was applied: annealing at 600°C, followed 1.5 hour dwell at the isothermal temperature and afterwards the material was cold on the air. Specimens for microstructural examination were prepared by standard metallographic techniques. The bimetal was etched in nitric acid and fluorhydrick one and in a water solution of hydrochlorid and nitric acid. For both material types metallographic evaluation included the grain sizes of bonded materials, the average wave amplitude and the total wave length.
The light microscope Olympus X70 and the electron microscope SEM JEOL JSM-6490 LV equipped with an energy dispersion analyzer (EDA) OXFORD INCA Energy 350 were used. The fatigue response was tested by use of the MTS 810 machine at the Technical University of Warszawa (Polytechnika Warszawska) with a loading extent of 400 to 1000 MPa by three-point bend. Wöhler curves were generated both for the explosive bonded plate and for the heat treated material.
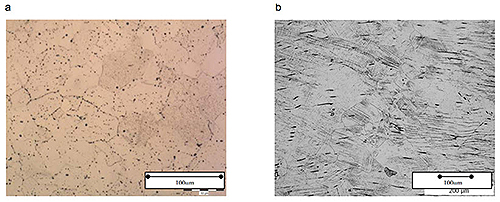
Figure 2: Micrograph of the stainless steel a) without the HT, b) with the HT