Abstract
Any strain aging process is heavily dependent on both time and temperature, with temperature for example having a strong influence on solute diffusion and binding energy along with the movement of dislocations.
In contrast to static aging processes, during dynamic strain aging, deformation and aging typically occur simultaneously.
Strain aging occurs when solute atoms are present and they have sufficient diffusivity with comparable dislocation movement. Time and temperature are thus the important determinants of strain aging. Temperature has a strong influence on the diffusion of solutes, on binding energies of solutes, as well as on movement of dislocations, so that rate of aging increases with increasing temperature.
The role of time can have two meanings depending on the rate of aging. If the rate is slow, and aging occurs clearly after deformation, the process is termed static strain aging (SSA). The extent of SSA increases with amount of time passed after deformation. However, if rate of aging is relatively high, aging can occur simultaneously with deformation. Then time has no similar meaning as in SSA. Rather, time corresponds to the rate of deformation. This is called dynamic strain aging (DSA), where deformation rate can be compared to time between loading and reloading in SSA.
Dynamic strain aging (DSA) is a phenomenon in metals and alloys resulted from the interaction between the diffusing solute atoms and the moving dislocation. It has been found that DSA occurs in many alloys during uniaxial tension or compression process. In traditional metal forming process, such as extrusion and rolling, it is difficult to control the DSA process because of the limited deformation time and deformation reduction. By contrast, the DSA process can be effectively controlled during the Sever Plastic Deformation (SPD) by constantly increasing accumulative strains.
Dynamic strain aging (DSA) is one of the hardening mechanisms affecting many materials, which manifests itself by “jerky” or serrated plastic flows and inhomogeneous yielding. These instabilities are referred to as Portevin Le-Chatelier effect, corresponding to temperature dependent strain localisation within a specific range of strain and strain rate as a consequence of DSA. DSA may be attributed to the interaction between diffusing point defects, such as solute atoms and mobile dislocations, during plastic flow. Serrations may be attributed to a repeated snowballing effect of locking and unlocking of dislocations by these defects, leading to heterogeneous deformation with an alternating increase/decrease in plastic activities, despite of a monotonic straining.
The occurrence of dynamic strain aging (DSA) has been extensively studied in many engineering alloys, which are applied in the nuclear power industry. DSA occurs in alloys containing solute atoms which can rapidly and strongly segregate to dislocations during straining. This phenomenon leads to an inhomogeneous plastic flow or serrated yielding during straining at elevated temperatures and results often in a remarkable degradation of mechanical properties. In nickel-base alloys and superalloys interstitial (H and C) and substitutional (Cr) solute atoms are usually responsible for jerky flow.
The aim of H. Hänninen et al investigation was to study the DSA phenomenon in Inconel 600 and 690 alloys and its effects on their mechanical properties. By means of internal friction (IF) technique the investigation of DSA mechanism of Inconel alloys was extended to interstitial atom diffusion.
A series of uniaxial tensile tests was conducted in the laboratory air under axial displacement control with constant cross-head speeds corresponding to initial strain rates of 1×10-3, 1×10-4, 1×10-5 and 1×10-6 s-1. The tests were carried out over a range of temperatures from ambient up to 700°C. All tests were performed in laboratory air. A 25 kN MTS 858 testing machine was used in the tensile tests. Materials were supplied as two metal plates in mill-annealed condition with thickness of about 14 mm for Inconel 600 and 5 mm for Inconel 690. Average grain size of the studied alloys was about 100 μm for Inconel 600 alloy and about 30 μm for Inconel 690 alloy. Materials were cut using water-jet cutting and sparkerosion techniques to form the flat specimens. The specimen surface was polished using SiC emery paper down to 800 grit to remove surface defects and to obtain dimensions of 1.9 × 6 × 32 mm.
Constant elongation rate tensile (CERT) tests were conducted in order to obtain the map of DSA serration appearance depending on strain rate and temperature for commercial grade Inconel 600 and 690 alloys. The effect of DSA on mechanical properties of the studied alloys is also investigated. Typical engineering stress-strain curves obtained at the strain rate of 10-5 s-1 are shown in Figures 1a and 1b.
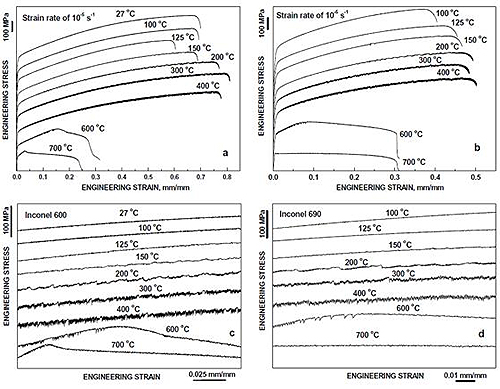
Figure 1: Engineering stress-strain curves obtained at the strain rate of 10-5 s-1 for Inconel 600 alloy (a and c) and for Inconel 690 alloy (b and d). (c) and (d) present magnified parts of the engineering stress-strain curves showing serration appearance.
DSA serrations are observed in both Inconel alloys in the range of temperatures. It can be seen from Figs. 1 c and d that at strain rate of 10-5 s-1 the DSA range extends from 150 to 600°C.