Abstract
Cryo-rolling is effectively deformation of materials at liquid nitrogen temperature (LNT) that assists in producing ultra-fine grained microstructures.
In specific specimens studied it was found that ultra fine structure was eventually formed by a huge level of deformation twinning followed by extensive shear banding.
Large deformation at cryogenic temperatures is sometimes considered as a promising cost-effective method for producing bulk ultra-fine grain materials. In the paper of T. Konkova, S. Mironov, A. Korznikov, G. Korznikova, M.M. Myshlyaev, S.L. Semiatin, the high-resolution electron backscatter diffraction (EBSD) was used to study grain structure development during cryogenic rolling of Cu–29.5Zn brass. Microstructure evolution was found to be broadly similar to that occurring during rolling at room temperature.
Specifically, favorably-oriented grains (Copper {112}<111> and S {123}<634>) experienced profuse deformation twinning followed by extensive shear banding. This eventually produced an ultrafine structure with a mean grain size of 0.2 μm. On the other hand, grains with crystallographic orientations close to Brass {110}<112> and Goss {110}<100> were found to be stable against twinning/shear banding and thus showed no significant grain refinement. As a result, the final structure developed in heavily-rolled material was distinctly inhomogeneous consisting of mm-scale remnants of original grains with poorly developed substructure and ultra-fine grain domains.
The main conclusions from this work are as follows.
- Grain refinement was primarily related to deformation twinning and shear banding. The more typical grain-subdivision process associated with the development of dislocation boundaries was very limited. The latter behavior was attributed to low stacking fault energy and the cryogenic temperature, both of which suppressed climb and cross slip.
- Microstructure evolution was found to be broadly similar to that occurring during rolling at room temperature. At very low reductions, a series of low-angle dislocation boundaries aligned with {111} plane traces were formed. After 30-pct. reduction (true strain 0.4), profuse twinning was observed in grains having crystallographic orientations close to Copper {112}<111> and S {123}<634> (see Figure 1). Once activated, twinning continued to 90 pct. reduction (true strain 2.3). Subsequent slip in the twinned areas produced a {111} γ fiber texture. After 50-pct. reduction (true strain 0.7), extensive shear banding developed in the twinned areas which rotated the γ fiber toward Goss {110}<100> and Brass {110}<112> orientations. Shear banding gave rose to marked microstructure refinement, eventually producing a mean grain size of 0.2 μm. (see Figure2)
- Grains with crystallographic orientations close to the Brass and Goss orientations were found to be stable against twinning/shear banding and thus underwent no significant grain refinement. As a result, the final structure developed in heavily-rolled material was distinctly inhomogeneous consisting of coarse remnants of original grains with poorly developed substructure and ultra-fine grain domains.
- The decrease of the rolling temperature to the cryogenic range shifted the onset of twinning and shear banding to lower strains but was unable to activate these two mechanisms in grains with the Brass and Goss orientations. As a result, cryogenic rolling did not lead to the formation of a homogeneous ultra-fine grain microstructure.
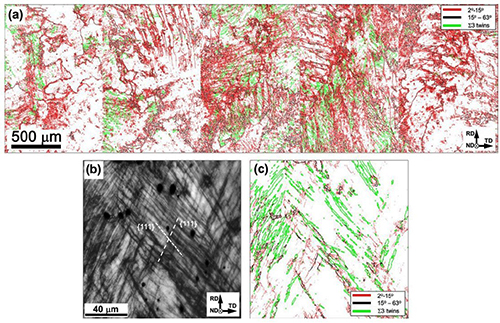
Figure 1: Microstructure after 30-pct. thickness reduction (true strain of 0.4): (a) low-resolution, composite EBSD grain-boundary map (grain-boundary color code is given in the upper right corner), (b) high-resolution Kikuchi-band-contrast EBSD map taken from the twinned area, and (c) grain-boundary EBSD map from the same location as (b). The broken lines in (b) show the {111} plane traces closest to the twin habit planes.
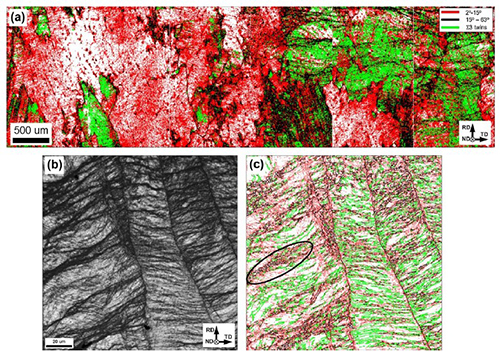
Figure 2: Microstructure after 50-pct. thickness reduction (true strain of 0.7): (a) low-resolution, composite EBSD grain-boundary map (grain-boundary color code is given in the upper right corner), (b) high-resolution Kikuchi-band-contrast EBSD map illustrating shear banding, and (c) grain-boundary EBSD map from the same location as (b). The dark bands in (b) are shear bands; the circled area in (c) illustrates substructure within the bands.
The effect of annealing treatment on the mechanical properties and microstructure of cold-rolled Cu- 20% Zn alloys was investigated in the work of X. Wu, Y. Gong, S. Ren, J. Tao, Y. Long, L. Cheng and X. Zhu. Mechanical properties changed dramatically with the increase of temperature. According to the microhardness test, it can roughly concluded that 150 ℃ is the optimal annealing temperature for deformation, at which a uniform elongation increased from 1.4658% before annealing to about 6.89%, and the elongation to failure increased from 7.426% to 16.81% with the same strength almost retained. The changes of microstructure during the annealing process are mainly distributed to the improvement of mechanical properties.
Cu-20% Zn was produced by induction vacuum melting. Hot-rolling was conducted to these as-cast after they were made into plates with a thickness of 7.9 mm. To minimize the effect of mechanical processing, the plates were homogenized at 600°C,750°C and 800°C for 4 hours in argon atmosphere respectively. During cold rolling process, the samples were soaked in liquid nitrogen for about 5 minutes before each rolling pass. These plates were cold rolled from a thickness of 7.9 mm to 0.5 mm producing a total strain of 93.67%.
The variations of microhardness at different annealing temperatures for RT and LN Cu-20%Zn are shown in Figure 3. As indicated in Figure 3, the microhardness of LN Cu-20% Zn was greatly enhanced at the temperature of 150°C,where the microhardness can be achieved as high as 189 HV. The microhardness changes for RT Cu-20% Zn showed different trend. As can be seen in Figure 1, no hardening is observed during the annealing process.
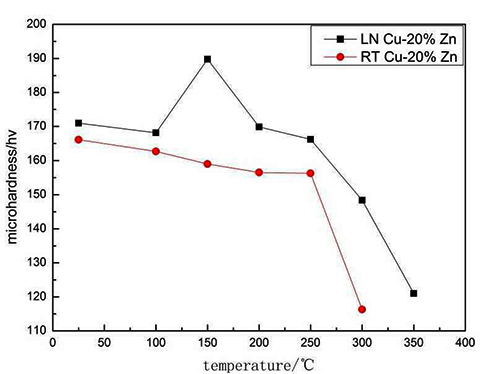
Figure 3: The variations of microhardness in different annealing temperatures