Abstract
Cold Crucible Induction Melting is an innovative process for melting particularly reactive metals using a water cooled metallic crucible to virtually eliminate contamination.
Applications of the resulting materials include titanium gold club heads, specialized automotive parts and much more.
The cold crucible induction melting (CCIM) is an innovative process to melt high temperature reactive materials.
The CCIM design is based on inductive coupling of a water-cooled high-frequency electrical coil with the glass, causing eddy currents that produce heat and mixing. A critical difference is that inductance coupling transfers energy through a nonconductive solid layer of slag coating the metal container inside the coil, whereas the joule heated design relies on passing current through conductive molten glass in direct contact with the metal electrodes and ceramic refractories. The frozen slag in the CCIM design protects the containment and eliminates the need for refractory, while the corrosive molten glass can be the limiting factor in the JH melter design. The CCIM design also eliminates the need for electrodes that typically limit operating temperature to below 1200°C.
The melting of extremely reactive materials in conventional ceramic crucibles at high temperatures leads to an inadmissible contamination of their liquid phase. This prevents the manufacturing of high purity metals such as, e.g., Titanium, Tantalum, Niobium and Molybdenum. However, the induction cold crucible process makes it possible to melt down these metals without them being contaminated by the crucible material. In the case of floating-zone silicon, the crystallographic perfection of homogeneously doped dislocation-free single crystals of today’s 200 mm diameter is a further challenge for the manufacturers. Only the contact-less induction melting technology can fulfil such manifold requirements.
This very pure melting process is based on the water-cooled metallic crucible, which makes the melt solidify immediately when coming into contact with the cold crucible wall (Fig. 1). A solid crust is formed. This so called skull protects the crucible against the hot melt and permits a melting process without any disturbing impurities. The energy, necessary to heat-up, melt down and overheat the charge, is transferred via the electromagnetic field of an inductor. To provide sufficient electromagnetic transparency, the metallic crucible is usually slitted, and consists therefore of several segments that are electrically isolated against each other.
The fascinating idea of preventing any contamination of highly reactive melts by the application of water-cooled metallic crucibles instead of ceramic ones is not new. The ceramic-free induction melting of such metals and their alloys in a water-cooled container was already patented in 1931 by the Siemens und Halske Company, Germany.
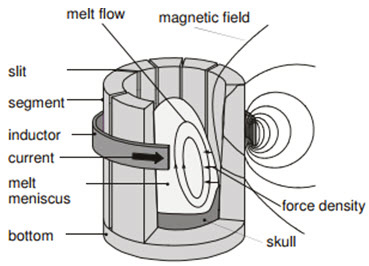
Figure 1: Induction cold crucible furnace, schematically Technology Advantages
- No refractories that can be damaged or corroded,
- No electrodes that corrode at high melt temperatures,
- Self-cleaning – the molten glass does not adhere to the water-cooled walls, enabling easier and more complete melter cleaning and decontamination, and
- High purity – without metals or refractories that interact with the melt, high purity melts are achieved.
Applications
- Titanium golf club heads;
- Titanium aluminide automobile valves;
- Structural and engine parts (titanium castings) for the aerospace industry;
- Implants for human medicine;
- Hot-end turbo charger wheels;
- Production of reactive metal powders;
- Zirconium pump casings and valves for the chemical industry and offshore drilling.