Abstract
Development of third generation, advanced high strength steels (AHSS) is well underway and is focused on advancements to provide even more superior strength-ductility ratios than in the currently available materials such as dual phase or TRIP steels.
Carbide free bainitic (CFB) steels may well contribute to these developments and in this article we explore the unique contributions that they can make.
Recently, there has been increased interest in the development of the third generation of advanced high strength steels (AHSS), i.e., steels with strength-ductility combinations significantly better than exhibited by the first generation AHSS i.e. steels that possess primarily ferrite-based microstructures such as dual phase (DP), transformation-induced plasticity (TRIP), complex-phase (CP), and martensitic (MART) steels.
These “3rd Generation” steels are designed to fill the region between the dual-phase/TRIP and the Twin Induced Plasticity (TWIP) steels with very high ductility at strength levels comparable to the conventional AHSS. Enhanced quenching and partitioning (Q&P) steels may be one method to achieve this target. Other ideas include TRIP assisted dual phase steels, high manganese steels and carbide-free bainitic (CFB) steels. Finally the post hardened steels (PHS) are an important component of the strategy of future vehicles.
Carbide-free bainitic (CFB) microstructure of steel contains only two phases, bainitic ferrite and retained austenite (RA). In comparison to conventional lower bainite, any carbide precipitates are not present. First experiments regarding low temperature CFB and discussing this kind of structure were published in early 1980s. Since then, the knowledge about its nature and morphology has been greatly improved, but there are still many scientific issues to resolve. Even though the development of CFB steels is still in progress, few applications have been found, i.e. rails and armours, but there are few other application possibilities, which are investigated by researchers (i.e. railway wheels, ball bearings and elements for the automotive industry).
Design methodologies based on diffusionless bainite transformation theory were applied to develop steels with a carbide-free bainitic (CFB) microstructure consisting of a mixture of bainitic ferrite, retained austenite, and some martensite. Using thermodynamics and kinetics models, CFB steels with a 0.2 and 0.3 wt.% carbon content were designed and manufactured following a conventional hot rolling practice. The designed steels present significant combinations of strength and ductility, with tensile strengths ranging from 1300 to 1800 MPa and total elongations of over 14%.
Earlier developments of CFB steels
Edmonds and co-workers showed that CFB is, in principle, an ideal microstructure from many points of view. An example of the microstructure of CFB is presented in Figure 1; instead of the classical structure of bainitic ferrite laths with interlath carbide, it consists of bainitic ferrite laths interwoven with thin films of untransformed retained austenite. In particular, the steel has a high resistance to cleavage fracture and void formation due to the absence of fine carbides. There is a possibility of simultaneously improving the strength and toughness because of the ultrafine grain size of the bainitic ferrite plates, and of further enhancing the ductility by TRIP effect. Original experiments by Bhadeshia and Edmonds were carried out in order to demonstrate the role of the To curve in greatly influencing the mechanical properties of carbide-free bainitic steels. The experimental alloys developed for this purpose were not necessarily the optimum alloys from the point of view of mechanical properties.
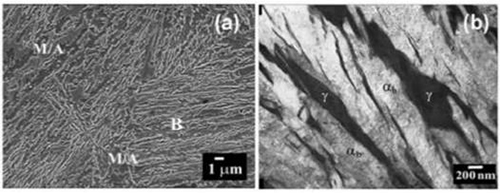
Figure 1: (a) Scanning and (b) transmission electron micrographs of carbide-free bainitic microstructure. M/A is martensite/austenite constituent; B is bainite; αb is bainitic ferrite and γ is retained austenite.