Abstract
Even a small amount of boron, added to the most common Titanium alloy, can have a significant effect on the alloy’s properties. The Benefits are not without trade-offs, though. There is a critical amount to be added, or the benefits will be lost.
What’s more, the industry that needs it the most might not be able to use this new form of Titanium alloy, due to the very behavior that makes the alloy possible.
In experiments by Yang Yu, et al. the addition of 0.1wt% Boron had a remarkable effect on the dynamic compression properties of Ti-6Al-4V (Ti-64A) alloy when tested by Split Hopkinson Pressure Bar (SHPB). The study also analyzed relative damage mechanisms. The results show that the as-cast microstructure of the alloy is refined due to the addition of Boron. The researchers found lower non-uniform distributions of strain, stress and local concentration due to non-harmonic deformation. Both dynamic strain and average dynamic flow stress are improved, with a reduction in the sensitivity to adiabatic shear behavior.
In cases of microstructure deformation at high strain rates with specimens containing 0.1wt% boron, dynamic strain and maximum absorbed energy is decreased by 10%~30% compared to that observed in normal Ti-64A alloys. In both Ti-64A and Ti-6Al-4V-0.1B (Ti-64B), the average dynamic flow stress is similar, and under high-speed impact loads it exhibits a damage of adiabatic shear and TiB phases bear the load during fracture.
Adiabatic shear band happens to be one of the root causes of fracture failure of Ti-64A and Ti-64B alloys after analysis of the deformed specimens’ microstructure. Adiabatic shear band formation and expansion can therefore be considered a precursor of material shear fracture failure. Deformation cavities can be formed between the TiB phase and the matrix during the deformation process, but this is not the main reason for material fracture failure.
Ti-64A and Ti-64B (nominal compositions) alloys were used in this study. The true stress-strain curves of Ti-64A and Ti-64B alloys, with different microstructures, are shown in Figure 1. During the dynamic loading process, the samples undergo elastic deformation, plastic deformation, and adiabatic shear localization. For the same microstructures, after plastic deformation, flow stress remains stable with increasing strain rate. This means that the plastic flow stress is not dependent on the microstructure and strain rate. However, the uniform plastic strain increases with increasing strain rate. The dynamic flow stress and uniform dynamic plastic strain of different microstructures are shown in Table 1.
Uniform dynamic plastic strain, which is the strain between the true stresses, does not change but decreases with the increase of strain. The dynamic flow stress is the average value of the flow stress in the uniform dynamic plastic strain.
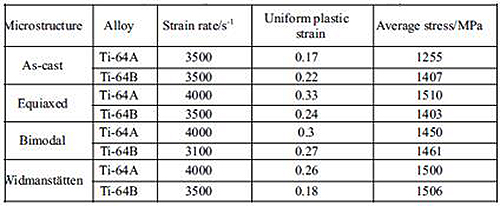
Table 1: Dynamic Properties of Ti-64a and Ti-64b Alloys
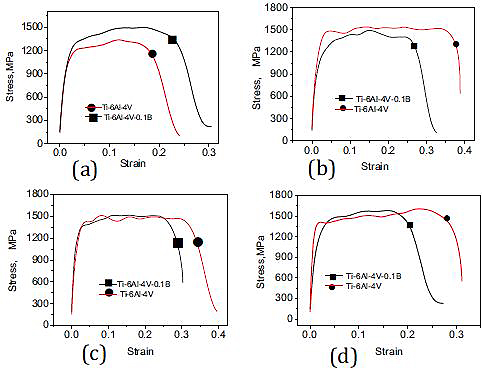
Figure 1: The dynamic true stress-strain curves of Ti-64A and Ti-64B alloy with different structure with strain rate of more than 3000s-1 (a) as-cast, (b) exquiaxed, (c) bimodal, (d) Widmanstätten
From the experimental investigation the following conclusions were made.
- Addition of 0.1% Boron evidently improved the dynamic properties of as-cast Ti-64A alloy.
- 0.1% Boron reduced the dynamic properties of Ti-64A alloy deformation microstructure. The order from strong to weak is Widmanstätten microstructure, exquiaxed microstructure, bimodal microstructure.
Effect of boron on microstructure
It is known that the addition of boron to cast Ti-6Al-4V (0.06 and 0.11 wt%) refines the coarse “as cast” microstructure. This fact was the subject of a study by R. Gaddam.
Initial studies on the effect of boron on microstructure were reported by Likhachev, et al. where small boron additions to α-Ti alloy (Ti-4Al-2V) resulted in a refinement of the microstructure by 2-3 times. Similar observations were noted in cast alloys such as CP-Ti, Ti-0.5Si, Ti-64, where adding less than 0.05 wt% boron produced a marked reduction in the prior β grain size. This has been attributed to the formation of TiB precipitates at the grain boundaries, which act as heterogeneous nucleation sites for β grains. However, from the equilibrium Ti-B phase diagram, it is seen that the solubility of boron in solid titanium is negligible (<0.02 wt% B). Hence, for grain refinement to take place there must be a critical amount of boron in order for TiB to form during cooling. Therefore, Tamirisakandala et al. proposed a mechanism, based on experimental observations, stating that boron contributes to grain refinement during solidification of titanium in four stages (see Figure 2). From Figure 2 the following can be observed:
i) inoculation of Tiβ nuclei at T<Tliquidus;
ii) growth restriction of β grains through the formation of boron rich layers on further cooling;
iii) during cooling below Teutectic the remaining liquid transforms to β-Ti and TiB precipitates at the β grain boundaries via eutectic reactions; and
iv) cooling below the Tβtransus, the β phase starts transforming to α phase, which under certain cooling conditions initially leads to the formation of grain boundary α with some TiB precipitates.
If the boron concentration is below the critical level, the boron rejected during solidification is dispersed into the remaining liquid without affecting grain refinement. According to the proposed mechanism, the TiB needles precipitate along the prior β grain boundaries, which was also observed in the present study.
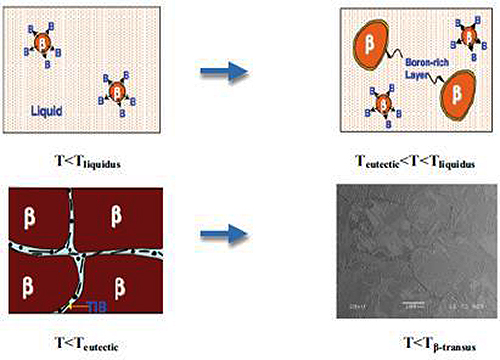
Figure 2: Schematic of the grain refinement process in boron-modified titanium alloys
According to this study, it can be concluded that the addition of 0.06 wt% and 0.11 wt% Boron to cast Ti-64 leads to:
- Formation of TiB particles predominantly located in the prior beta grain boundaries;
- Smaller prior beta grain size;
- Smaller alpha colony size;
- Shorter but thicker alpha lamellae.
At room temperature the compressive yield strength increased by approximately 15% when 0.06% Boron was added to the standard Ti-64 alloy. The main reason for this is the smaller alpha colony size.
The strengthening effect of the finer microstructure in the boron-modified Ti-64 versions diminishes at temperatures exceeding 500°C. The TiB particles have a long thin shape and are brittle in nature and fractured during the compression tests. The brittleness of these TiB particles is a serious drawback for the potential use of these kind of materials in aerospace applications, but further investigations are required to explore the fatigue properties of this material before this risk can be neglected.