Abstract
Asymmetric steel rolling is a key technique to help minimize defects that can occur in the rolling process as a result of process variations such as uneven heating of the strip or imprecise elements of rolling mill itself.
Asymmetric steel rolling helps counteract these issues by appling a large shear strain uniformly through the thickness of the plate, by maintaining a high degree of friction between the sheet and the rolls.
Rolling of flat products is one of the most frequently used processes of metal deformation. These products are required to have small tolerance of thickness on strip length and width. In industrial conditions we often encounter different diameters of working rolls, difference of neutral axis of strip and neutral axes of deformation zone, uneven heating of strip or imprecise elements of rolling mill. As a result, there occur defects of the strip in the form of side strain on its width.
It is not possible to improve these defects by squaring-up. In the real process of rolling, the size of rolled strip crossing in the temperature of rolling only approximately corresponds to the size of rolling gap during the pass process. The height of the gap during the rolling process is larger than its size during the rolling without load. This degree changes during the rolling process causing vibrations of the rolled strip. These changes are the consequence of the following causes:
- rolls and bearings have their own defects (eccentricity) as well as exploitation (e.g. growth of rolls diameter caused by heat expansion, oil film thickness oscillations – which occur in connection with the change of rolling rate together with temperature differences of lubrication),
- rolling mill stands, rolls and their bearings are getting worn out (frequently unequally), which induces changes of the size of the rolling gap,
- rolling mill is an elastic system, deformations of which are of different value depending on the velocity of load pressure. Velocity of load pressure oscillates in the next passes and also changes during deformation of strip.
Size deviations of rolled products which appear because of the aforementioned causes can be limited by using asymmetric rolling. As a result of such rolling total pressure of metal on rolls decreases and flatness improves, thickness inequality along the length of plate decreases and transverse section is better. The system of asymmetric rolling influences indirectly the strip in the zone of deformation, where due to introduction of asymmetry velocity of working rolls appear longitudinal tensile stresses. Their influence is identical to that of front-pull and back-pull in continuous rolling. They determine the decrease of unit pressure and leveling uneven breaking up of strip thickness at the cost of flexibility of mill. Regulation of thickness breaking-up on strip length, flatness and diametrical shape of strip takes place with minimized total pressure velocity of metal on roll. System of asymmetric rolling may be used interchangeably with the system of hydraulic gap control and working roll bending, but tolerance of asymmetry velocity value factor is limited by driving engine capacity and ability of strip slipping in the deformation zone and therefore it is not sufficient for realization of all functions which affect strip shape. The most appropriate is the combination of the abovementioned systems of shape regulation and thickness breaking-up of strip.
Thin strip produced in symmetric cold rolling has a wide application in electronic and instrumental industries.
Materials with ultrafine-grained structure and unique physical and mechanical properties can be obtained by methods of severe plastic deformation, which include processes of asymmetric rolling (AR). Asymmetric rolling is a very effective way to create ultrafine-grained structures of metals and alloys. Since the asymmetric rolling is a continuous process, it has great potential for industrial production of ultrafine-grained structure sheets.
The aim of asymmetric rolling is to apply a large shear strain uniformly through the thickness of the plate, by maintaining a high degree of friction between the sheet and the rolls. It can be used to improve the formability of material. One of the advantages of asymmetrical rolling is that the rolling force and torque can be decreased. An economic and technological reason, in particular the longitudinally asymmetric rolling is very important to determine the optimum process parameters.
Asymmetric rolling with peripheral speed or roll radius difference will result in a decrease of 30-40% rolling force.
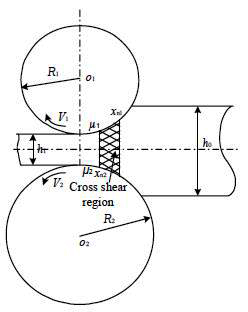
Figure 1: Asymmetric strip rolling