Abstract
Aluminum hypoeutectic alloys are Al-Si based and offer a good compromise of positive characteristics including good castability and weldability as well as low thermal expansion and good corrosion resistance.
Eutectic transformation is the critical second stage of solidification of Al-Si alloys whereby the characteristic microstructural changes take place and can be specifically attributed to the eutectic Si particles in the α-matrix.
Aluminum foundry alloys can be tailored to cover a wide range of mechanical performance via chemistry and/or process control. There are four main families based on Al-Si(-Cu), Al-Cu, Al-Mg(-Si), and Al-Zn(-Si)- Mg systems The vast majority of cast Al components are based on the Al-Si system because of its good castability. Some Al-Cu, Al-Mg and Al-Zn alloys exhibit better properties than Al-Si alloys, but their casting properties are generally poor. In particular, they show a high tendency to hot tearing.
The hypoeutectic Al-Si based alloys are well-known casting alloys with a highly desirable combination of characteristics, such as castability, weldability, low thermal expansion coefficient, good corrosion resistance, and machinability. These properties lead to the application of Al-Si alloys in automotive industry, especially for automotive engines, crankcases, intake manifolds, cylinder blocks, cylinder heads, pistons, cast oil pans and valve lifters.
Mechanical properties are principally controlled by the cast structure. Microstructure evolution of hypoeutectic Al-Si alloys during solidification is in two stages: primary dendrite Al-phase formation (α-matrix), and the subsequent eutectic transformation (eutectic Si particles in α-matrix). Based on the Al-Si binary diagram, the volume fraction of Al-Si eutectic in commonly used hypoeutectic Al-Si alloys, such as AlSi7Mg0.3, AlSi9Cu3, AlSi6Cu4, can be more than 50 %. Typically, the Al-Si eutectic accounts for a volume fraction of 50-90 % of these alloys.
The aim of T. Szymczak, G. Gumienny, I. Stasiak, and T. Pacyniak study was to investigate the effect of simultaneously added Cr, V, and Mo on the crystallization process, microstructure and mechanical properties of hypoeutectic Al-Si alloy to pressure die casting.
The research was performed under the production conditions of the Innovation and Implementation Enterprise Wifama-Prexer Ltd., Poland. To the study 226 standard hypoeutectic aluminum alloy to pressure die casting was used. Its chemical composition is given in Table 1.

Table 1: The chemical composition of the 226 Al-Si alloy tested, wt.% [3] The additives tested were added as AlCr15, AlV10 and AlMo8 master alloys. Alloys tested were poured into DTA sampler as well as using pressure die casting. An amount of Cr, V and Mo additives in alloy poured into DTA sampler comprised within the range approximately 0.05-0.35%. Alloys to pressure die casting contained 0.05-0.20% Cr, V and Mo. The crystallization process was examined using the derivative thermal analysis (DTA).
It has been shown in the DTA curves of Al-Si alloy containing approximately 0.30 and 0.35% Cr, Mo, and V there is an additional thermal effect probably caused by a peritectic crystallization of intermetallic phases containing the aforementioned additives. These phases have a morphology similar to the walled and a relatively large size. The analogous phases also occur in pressure die casting alloys containing 0.10% or more additions of Cr, V and Mo.
The appearance of these phases in pressure die casting Al-Si alloys coincides with a decrease in the value of the tensile strength Rm and the elongation A. It has been shown die castings made of Al-Si alloys containing the aforementioned additives have a higher Rm and A than 226 alloy.
Figure 1 shows SEM microstructure and three dimensional morphology of the eutectic Si in as-cast AlSi6Cu4 alloy without, whit 1 000 and 10 000 ppm Sb. The microstructure seen in Figure 1a reveals fine, but still plate-like eutectic silicon. It is obvious in Figures 1a, 1b that the fine eutectic Si platelets decrease more and more in size after addition of Sb and changes morphology from compact plate-like to stick or fibrous. Si-particles in samples with 10 000 ppm coarsens probably as a result of over-modification (Figure 1c). [4] [2]
Morphology of eutectic Si in all heat treated samples (Figure 2) was observed as rounded particles. After deep etching we observed fragmentation of fine compact Siplate-like phase and its transformation to fine sticks-like phase (Figures 2a, 2b, 2c).
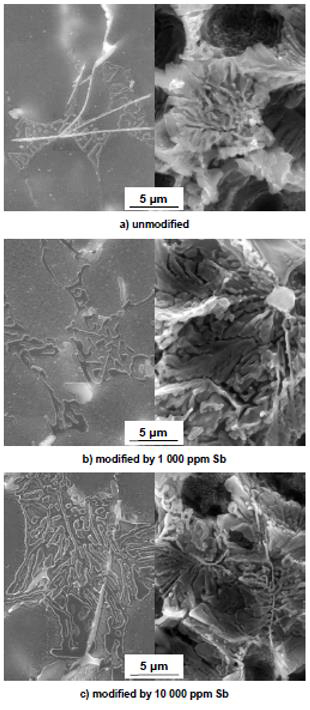
Figure 1: Morphology of eutectic Si, state, etch. 0.5 HF/deep etch., SEM
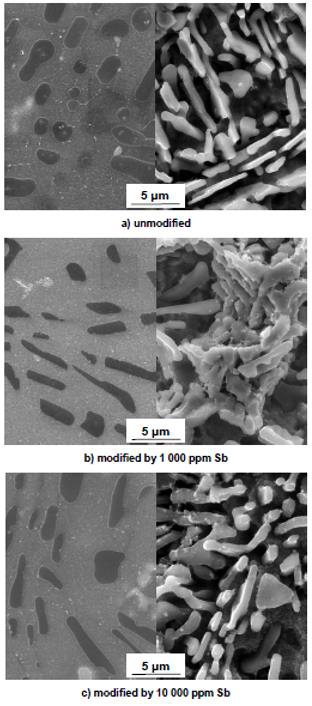
Figure 2: Morphology of eutectic Si as cast after heat treatment, etch. 0.5 HF/deep etch., SEM