Abstract
High manganese austenitic steels represent a significant advancement in metallurgical engineering, offering exceptional combinations of ductility, toughness, and wear resistance. This article examines the development, composition, and characteristics of these steels, particularly focusing on Hadfield steel, which contains 11-13% manganese and 1-1.3% carbon. The material's unique work-hardening properties, applications in high-impact environments, and processing requirements are discussed, along with its limitations and performance characteristics in various industrial applications.
Historical Development
Sir Robert Abbott Hadfield's 1882 discovery of manganese steel marked a breakthrough in alloy steel development. Through extensive experimentation, he established that optimal properties could be achieved with a manganese-to-carbon ratio of 10:1, specifically with 11-13% manganese and 1-1.3% carbon content.
Composition and Properties
High manganese austenitic steels demonstrate unique characteristics:
- Full austenitic microstructure at room temperature
- Yield strength: 345-415 MPa (as-quenched)
- Ultimate tensile strength: 965 MPa
- Elongation: 50% in 50mm
- Reduction of area: 40%
- Hardness: 190 HB (as-quenched), 500 HB (at fracture)
Table 1. Standard composition ranges for austenitic manganese steel castings
ASTM A128 |
C |
Mn |
Cr |
Mo |
Ni |
Si |
P |
A |
1.05-1.35 |
Min 11 |
- |
- |
- |
Max 1.0 |
Max 0.07 |
B-1 |
0.9-1.05 |
11.5-14.0 |
- |
- |
- |
Max 1.0 |
Max 0.07 |
B-2 |
1.05-1.2 |
11.5-14.0 |
- |
- |
- |
Max 1.0 |
Max 0.07 |
B-3 |
1.12-1.28 |
11.5-14.0 |
- |
- |
- |
Max 1.0 |
Max 0.07 |
B-4 |
1.2-1.35 |
11.5-14.0 |
- |
- |
- |
Max 1.0 |
Max 0.07 |
C |
1.05-1.35 |
11.5-14.0 |
1.5-2.5 |
- |
- |
Max 1.0 |
Max 0.07 |
D |
0.7-1.3 |
11.5-14.0 |
- |
- |
3.0-4.0 |
Max 1.0 |
Max 0.07 |
E-1 |
0.7-1.3 |
11.5-14.0 |
- |
0.9-1.2 |
- |
Max 1.0 |
Max 0.07 |
E-2 |
1.05-1.45 |
11.5-14.0 |
- |
1.8-2.1 |
- |
Max 1.0 |
Max 0.07 |
F(U91340) |
1.05-1.35 |
6.0-8.0 |
- |
0.9-1.2 |
- |
Max 1.0 |
Max 0.07 |
Microstructural Characteristics and Processing
The material maintains a stable, single-phase austenitic structure when properly heat treated.
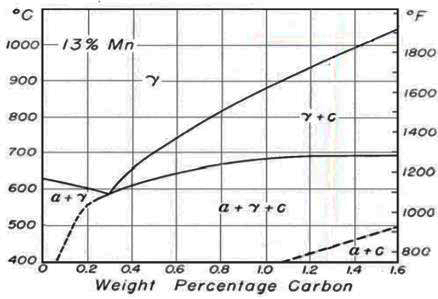
Figure 1: Phase diagram of steel containing 13% manganese
The steel requires austenitization above 1000°C followed by water quenching to dissolve carbides and produce homogeneous austenite. This process ensures carbon remains in supersaturated solid solution, crucial for optimal performance.
Applications and Limitations
Despite challenging machinability and relatively low initial yield strength, these steels excel in:
- Railway crossings
- Crawler treads for tractors
- Impact hammers
- High-wear environments
Surface hardening through mechanical working (hammering, pressing, cold rolling, or explosion shocking) significantly improves yield strength, creating a hard surface layer while maintaining a tough core structure.
Standard Specifications
ASTM Standard A-128-64 defines composition ranges:
- Carbon: 1.0-1.4%
- Manganese: 10-14% (typically limited to 12-13% for economic reasons)
- Work hardening reaches maximum at 13% Mn in 1.15% C alloys