Abstract
The main challenges of welding dissimilar relate to the range of different properties displayed by the different materials and how these effect the finished nature of the joint itself.
There is still much to learn about welding dissimilar materials but improving the related techniques in this complex technological subject can lead to great gains across many industry sectors.
The need for joining dissimilar metals has existed for a long time and has generally been considered to be beyond state of the art. Dissimilar metals have different chemistries, so they have different properties, such as melting temperatures. Many of these metals are alloys or a mixture of several elements, all of which melt at different temperatures. Therefore, when accomplishing a weld, it is virtually impossible to prevent a chemical change at the moment a melt of the parent metals occurs.
Welding the common austenitic stainless steels such as 304 and 316 to each other or themselves is routine and the easiest of fusion welding. Nevertheless, there are many situations where it is necessary to weld stainless steel to carbon steel or other even more unusual combinations.
Two common examples are balustrade posts attached to structural steel or doubler plates connecting supports to stainless steel vessels. There are differences in physical properties such as thermal conductivity and expansion, magnetic properties, metallurgical structure and corrosion resistance, which all require attention. This article outlines the necessary procedures for satisfactory welding, including reference to standards, and explains the necessary precautions. Appendix H of AS/NZS 1554.6:2012 has a more detailed technical discussion including advice on welding carbon steel to ferritic, duplex and martensitic stainless steels.
Dissimilar material welding is more complex than similar weld due to the necessity of the process being applied in zones where a requirement is to improve some properties. The main purpose of the paper B. I. Mendoza et al. is to know the mechanical behavior of a dissimilar weld between HSLA Steel and Super-duplex Stainless Steel (SDSS) to establish if the joint is feasible or not. The alloys were welded using the GTAW process using a 60-deg and 90-deg single -V groove test specimens in order to observe the effect of the weld pass. The filler metal was chosen with the aid of Schaeffler diagram.
It was found that the ER 25.10.4L filler metal provided the best equilibrium between ferrite and austenite phase in the Super-duplex Stainless Steel final microstructure and a band of martensite in the HSLA steel final microstructure. The dissimilar joint presented acceptable mechanical properties which are superior to the HSLA in the as-received condition, but lower than the SDSS in the as-received condition, proving that the filler metal was the adequate.
In Figure 1 it is possible to observe the difference on the microstructures in function of the thermal cycles promoted by the welding passes, such effect could be noticed in the heat affected zone (HAZ) of the API X-52, where the phase transformation can be observed in function of the contrast, as well as the weld metal.
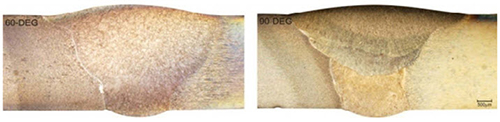
Figure 1: DMW with different number of welding passes Dissimilar metal welding (DMW) of the bio-compatible materials stainless steel (SS) and the shape memory alloy Nickel-Titanium (NiTi) is of particular interest within the bio-medical industry due to the exceptional mechanical properties of NiTi and the low cost of stainless steel 316. This particular material pair, however, suffers from significant intermetallic formation after mixing which results in brittle joints which are unable to withstand handling and use. A number of intermetallic phases exist even in the simplified binary Fe-Ti system.
The addition of alloying elements such as Cr and Ni found in SS and NiTi introduces further complexities in microstructure and phase formation. The dissimilar material pair between stainless steel and titanium alleviates some of these complexities by reducing the nickel composition from roughly 50 at% in the NiTi to only ~10 at% in the SS while still enabling the formation of Ti-Fe-based intermetallics.
Traditional joining methods such as arc welding when applied to dissimilar material pairs have been found to introduce excessive amounts of heat resulting in the formation of large volumes of intermetallics. Some success has been found through the use of laser welding due to its precise, localized heat input capabilities which allows for small heat affected zones, however, the joints still suffer from brittle intermetallic formation.
Laser fusion welded dissimilar joints between stainless steel 316 and titanium grade 2 have been investigated as a simplified model for the NiTi - stainless steel dissimilar material pair. Tensile strengths of the joints are observed to be lower than the base materials with failure occurring through brittle fracture. EDX and EBSD analysis indicated the formation of coarse intermetallic TiFe dendrites within a β-Ti matrix in the main weld pool and single-phase supersaturated β-Ti(Fe) in the lower weld zone.
Fracture surface analysis suggests that smooth interdendritic fracture between dendrites oriented perpendicular to the tensile load is the predominant mechanism of failure in the main weld pool while alternating failure along the SS-weld and Ti-weld interfaces was observed in the lower weld zone. Significantly greater surface area formation was observed in the lower portion of the weld suggesting that the single-phase supersaturated β-Ti(Fe) structure may be beneficial for fracture resistance.
The specific fracture morphologies observed and preferential cracking within the coarse dendritic microstructure observed near the stainless-steel base material in the main weld pool suggests that control over the weld pool geometry, heat flow, and quench rate may allow for robust dissimilar metal welds between titanium and stainless steel.
On the other hand, several problems arise when welding dissimilar steels, related mainly to the different physical, chemical and mechanical properties of the welded materials. Austenitic stainless steel and low carbon steel possess a good combination of mechanical properties, formability, weldability and resistance to corrosion. This combination of steels is extensively used in the power generation industry. Research on welding is carried out at various research institutions. The aim of our paper is to analyze and compare the properties of resistance spot welds of low carbon steel and austenitic stainless steel. Optical microscopy, microhardness measurements and EDX analysis were used to analyze the properties of the spot welded joints.
The macrostructure of the welded joint produced by using a welding current of 7.5 kA is documented in Figure 2. As the macrostructure suggests, the welded joint is asymmetrical. The fusion zone size on the stainless steel side is larger than the fusion zone on the low carbon steel side. Similar results were also observed in welds produced with welding currents of 7 and 8 kA. The heat-affected zone (HAZ) of the DC 01 steel is broader due to the higher thermal conductivity of the low carbon steel sheet. On the basis of macrostructure analysis, it can be stated that the higher the welding current that is used, the larger the fusion zone.
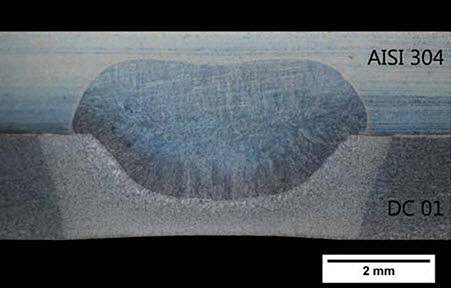
Figure 2: The macrostructure of a selected dissimilar resistance spot weld (IW = 7.5 kA) The microstructure of low carbon steel is fully ferritic. Grain refining was observed in the low temperature HAZ of carbon steel (see Figure 3). Some amounts of pearlite were also present.
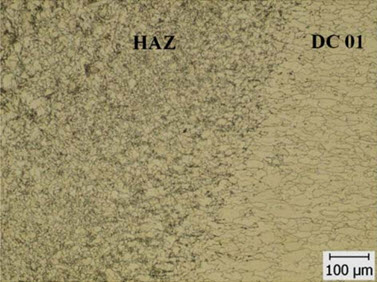
Figure 3: HAZ – DC 01 steel interface