Abstract
Stress in a component or metal part can be caused by a number of different factors including welding, machining, cutting, drilling and this may have a detrimental effect on the parts finished properties.
There are a number of techniques to rectify stress related anomalies but the most basic parameters used to redistribute the effects of stress are a combination of time and temperature.
Stress Relief of Steels
Stress in metal components can be caused by various manufacturing processes such as welding, machining, cutting, drilling, and grinding. These stresses can adversely affect the finished properties of metal parts. To mitigate these stress-related anomalies, stress relieving techniques, primarily involving time and temperature, are employed.
Causes and Effects of Stress in Metal Parts
Manufacturing processes like welding, machining, cutting, drilling, and grinding induce stress in metal parts. This residual stress can lead to distortion during the manufacturing process and can be detrimental in service, causing issues like cracking and instability. Stress relieving helps to counteract these problems, enhancing the durability and performance of metal parts.
Stress Relieving Process
Stress relieving is applied to both ferrous and non-ferrous alloys. The process involves heating the metal to a specific temperature and holding it for a certain period, followed by controlled cooling. This reduces residual stresses and improves dimensional stability during subsequent machining operations.
Stress Relieving Temperatures and Times
Carbon Steels
Carbon steels are typically stress relieved by holding them at a temperature of 1100 to 1250°F (600 to 675°C) for 1 hour per inch (25 mm) of thickness. This process ensures greater dimensional stability during machining, resulting in increased dimensional reliability.
Temperature Ranges for Different Steels
Steel Type |
Temperature Range |
Unalloyed and Low-Alloy Steels |
1025°F to 1200°F (55°C to 650°C) |
Hot-Work and High-Speed Tool Steels |
1115°F to 1300°F (600°C to 700°C) |
For many alloy steels, stress relief is minimal below 500°F (260°C), but around 90% of the stress is relieved by 1000°F (540°C). The maximum temperature for stress relief is limited to 55°F (30°C) below the tempering temperature used after quenching.
Oven Stress Relief Temperatures and Times for Wire
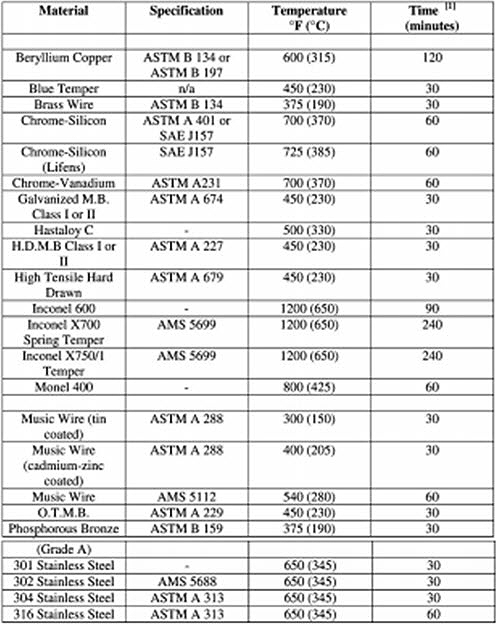
Table 1: Oven Stress Relief Temperatures and Times for Wire
As seen in Table 1 above, stainless steels may be stress-relieved. There are a variety of treatments which are presented in the table below:
Treatment Type |
Temperature Range |
Description |
Stress Redistribution |
290 to 425°C (550 to 800°F) |
Reduces peak stresses and increases tensile and yield strength without causing carbide precipitation. |
Stress Relief |
425 to 595°C (800 to 1100°F) |
Minimizes distortion and should be used for low carbon "L" grades or stabilized 321 and 347 grades. |
Full Stress Relief |
815 to 870°C (1500 to 1600°F) |
For assemblies requiring full stress relief, testing for IGA susceptibility is recommended. |
Table 2: Various stress-relieving treatments for stainless steels
Thermal stabilization treatments at 900°C (1650°F) for 1 to 10 hours are occasionally used to agglomerate carbides, preventing further precipitation and intergranular attack (IGA).
Industries Using Steel Stress Relieving
Steel stress relieving is crucial in various industries to ensure the integrity and performance of metal components. Key industries include:
- Power Generation
- Heat Exchangers
- Instruments
- Medical Devices
- Aerospace
- Tube & Pipe Manufacturing
- Stampings
- Tool & Die
- Electronics
- Defense
- Automotive
- Metal Fabrication
- Job Shops