Abstract
Sheet metal has massive application worldwide and is a highly important form in most manufacturing sectors such as aerospace, automotive, food industry and across nearly all manufacturing industries.
Forming process are both abundant and varied in their application and can include more common examples such as drawing, stamping or roll forming but also less well known examples such as explosive and magnetic pulse forming.
Sheet metal forming involves a wide range of processes that manufacture parts for a vast amount of purposes, both seen and unseen. Sheet metal refers to metal that has a high surface area to volume ratio. Sheet metal work stock, used for sheet metal processes, is usually formed by rolling and comes in coils.
A distinction needs to be made between sheet metal and plate metal. Sheet metal is 1/4 inch or less in thickness, while plate is over 1/4 inch in thickness. Sheet and plate have different applications. Plate is generally used for larger structural parts like boilers, turbines, bridges and ships. Sheet metal is used in the manufacture of cars, trains, aircraft, farm equipment, office equipment, furniture, house appliances, computers, machine components and beverage cans to name a few.
Some of the sheet metal manufacturing processes may be applicable to plate metal as well, even though the work piece is referenced only as sheet metal. However plate, particularly thicker plate, will provide its own set of problems in processing. Therefore, some of the sheet metal operations discussed may not be applicable to plate.
Sheet metal manufacture is mostly performed on a press and parts are formed between two die. The top die is called a punch. Sometimes sheet metal parts are referenced to as stampings. Parts are usually economical and easy to mass produce. Sheet metal is usually formed cold, however warm or hot working of parts, (particularly plate), is possible.
Generally for sheet metal applications there is essentially no change, or negligible change, in sheet thickness. For some processes like deep drawing, there is a slight and expected change in thickness, but this may also be neglected in most cases. Sheet metal manufacturing produces parts that typically have high strength, good surface and accurate tolerances.
Sheet metal forming is used in almost every sector of industrial production:
- Automotive industry (e.g. doors, hoods, fenders)
- Aircraft industry (e.g. wings, fuselage)
- Home appliance industry (e.g. sinks, cooker hoods, freezers)
- Food industry (e.g. cooking pots, canned goods)
Sheet metal forming is used for industrial manufacturing in many sectors – from car door to tin can.
In sheet metal forming, the final shape of a part is made from a flat metal sheet. The desired shape is achieved through plastic deformation, without undergoing any machining like milling. In most cases, a certain amount of elastic deformation leads to springback which occurs after forming is complete.
According to DIN 8582, the process is divided corresponding to the stresses which typically appear in the sheet:
- Forming under compressive conditions
- Forming under combination of tensile and compressive conditions
- Forming under tensile conditions
- Forming under bending conditions
- Forming under shearing conditions
The forming of the sheet can be carried out using mechanical tools, with air or with liquids, magnetically or with explosives. Special sheet metal processes include superplastic forming and press hardening, as well as the hot forming of aluminum and magnesium. Table 1 shows the common characteristics of sheet metal forming processes.
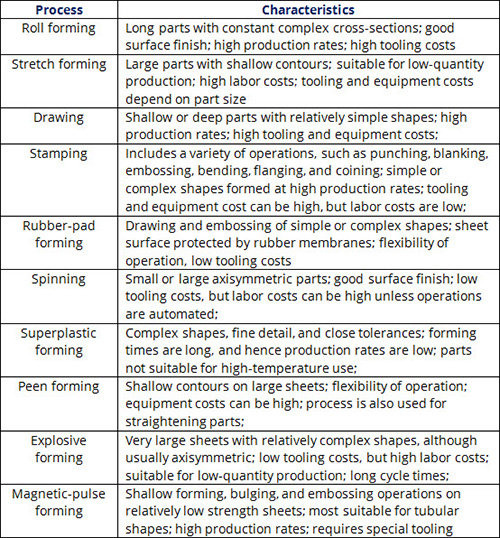
Table 1: The common characteristics of sheet metal forming processes