Abstract
The V-Process was invented in Japan in 1971 as an improvement on conventional sand casting.
The original inventors of this proprietary vacuum process have established working agreements on a worldwide basis so that today individually licensed foundries using the V-Process can produce castings of all sizes and shapes.
Vacuum (“V”) Process
The V-Process was invented in Japan in 1971 as an improvement on conventional sand casting. In this process, a thin preheated sheet of plastic film material is placed over a pattern and a vacuum is applied to draw the sheet to the pattern contours. The flask containing the mould is then filled with dry unbonded silica sand which is compacted by vibration.
A second plastic sheet is placed at the back of the flask and the mould is further compacted under vacuum. With the vacuum process maintained, the pattern is then removed and the two halves of the mold are joined and secured for pouring. After the metal has solidified, the vacuum is removed and the casting is released.
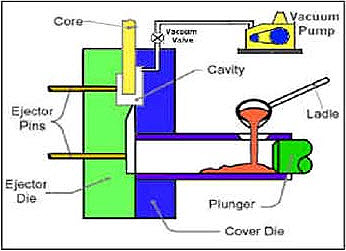
Figure 1: Vacuum casting process
The original inventors of this proprietary vacuum process have established working agreements on a worldwide basis so that today individually licensed foundries using the V-Process can produce castings of all sizes and shapes.
These ranges from thin-sectioned curtain walls in aluminum to cast iron pressure pipe fittings and stainless steel valve bodies to massive 8-tonne ship anchors. Other components being routinely cast include bathtubs, railroad bolsters and side frames, machine tools, engine parts and agricultural castings. Any metal (Grey, ductile, malleable iron, various grades of steel, or aluminum and copper-base alloys) may be poured in a V-process mold, with the possible exception of magnesium.
Advantages of Vacuum ('V') Process
- Gives good dimensional accuracy and surface finish with generally twice the accuracy of sand castings.
- Eliminates gas hole defects.
- Pattern life is longer because there is no contact between the sand and the pattern.
- Eliminates the use of binders and minimizes sand waste.
- Is suitable for a wide range of casting sizes from grams to tonnes.
- The process can be used for complex geometries and can be automated to achieve greater consistency and productivity.
- It can be highly cost competitive with other casting processes.
Limitations of Vacuum ('V') Process
- Requires plated pattern equipment.
- Close synchronization of mould and metal readiness is essential in foundry practice.
- Is not typically suitable for high rates of production.
- Is not suitable for some casting geometries due to flexibility limitations of the plastic.